Изготовление деталей для автомобиля — AVTOkapitan
Востребованные направления работ
Понятно, что браться за изготовление коленвалов, генераторов, КПП и других сложных конструктивных узлов нет смысла. Для решения задач такого плана подключаем проверенных поставщиков, способных найти комплектующие на любой автоэксклюзив. А вот мелочевка, нестандартные детали, изготовлением которых автопроизводители не занимаются, эти направления по силам нашим специалистам.
Сервис укомплектован оборудованием для сварочных, токарных, штамповочных работ, формовки из полимеров, деревообработки. Среди задач, с которыми к нам обращаются московские автовладельцы, выделим такие направления.
Производство конструктивных элементов для любителей экстрима
Стандартная комплектация большинства машин мало предрасположена для эксплуатации в условиях бездорожья. Любителям рыбалки, охоты, путешествий паркетники — не помощники. А мы решим эту проблему и подготовим вашу машину к сложным условиям.
Делаем и устанавливаем следующие конструктивные элементы:
- Алюминиевые и стальные силовые бамперы с комплектом крепления для лебедок.
- Металлическую защиту картера двигателя, редукторов, КПП, днища кузова.
- Силовые подножки и декоративные детали.
- Выпускные трубы (шноркели) с выводом патрубка на уровень крыши и выше.
Все узлы и крепежные элементы конструируем с учетом предполагаемых нагрузок. Используем металл, трубы с соответствующими прочностными характеристикам. Внешний вид силовых деталей подгоним под экстерьер машины, с применением различных технологий декоративно-защитной обработки поверхности.
Кузовные детали для ценителей тюнинга
Грамотно разработанные кузовные элементы улучшают внешний вид и динамические характеристики машины, сокращают расход топлива, повышают узнаваемость даже бюджетных авто в транспортном потоке. Именно по этим причинам тюнинг не теряет своей актуальности. В большинстве случаев делаем кузовные детали по индивидуальным чертежам с учетом вкусов автовладельца и особенностей машины.
Среди наиболее популярных направлений, по которым работает сервис, выделим:
- Аэродинамические обвесы, в том числе спойлеры и антикрылья.
- Молдинги и декоративные накладки на бока и крышу машины.
- Капоты и крышки багажника.
- Воздухозаборники для двигателя и охлаждения тормозных устройств.
- Накладки на передние фары и задние фонари.
- Боковые зеркала.
Делаем детали для спорткаров и ретроавтомобилей. При необходимости изготовим практически любой кузовной и конструктивный элемент, необходимый для восстановления старых машин. Работаем с металлом и различными видами пластика с последующей декоративной обработкой по желанию заказчика.
Комплектующие для инсталляции допоборудования
Установка нештатного оборудования — всегда эксклюзивное решение, в реализации которого автопроизводитель ничем не поможет. Именно на этот сегмент приходится большинство заказов по изготовлению деталей. В основном это несложная в техническом плане мелочевка, но без нее никак не обойтись.
Чаще всего у нас заказывают изготовление таких деталей:
- Для установки магнитол, усилителей, чейнджеров — переходные рамки и крепеж, подиумы и декоративные панели.
- Для инсталляции динамиков — проставочные кольца и подиумы, в том числе и со сложной формой, короба для сабвуферов с учетом требуемого акустического оформления.
- Для установки выносных мониторов — крепежные комплекты, включая и складывающиеся или выдвижные, индивидуальные подголовники для монтажа дисплеев.
Для изготовления используем дерево и фанеру, МДФ и металл. Декорируем с применением наиболее востребованных в интерьерном тюнинге салона покрытий. Каждая деталь обеспечит надежное крепление аппаратуры и будет смотреться в машине органично.
Эксклюзивные решения
Наряду с несложными деталями и комплектующими, делаем и сложные компоненты салона, способные повысить общий уровень комфорта в машине.
Среди реализованных проектов отметим:
- Водительские и пассажирские передние сиденья для легковых авто — обычные и анатомические, спортивные с увеличенной боковой поддержкой и расширенными регулировками.
- Задние пассажирские диваны с обустройством подлокотников для вывода в салон сабвуферов.
- Дверные карты под громкий фронт и установки нескольких динамиков.
- Элементы торпедо и центральные консоли под инсталляцию комплекса аппаратуры.
По каждому из заказов разработаем и реализуем индивидуальное решение, сделаем салон вашей машины неповторимым. В работе применяем пластики, металл, дерево с оклейкой или обтяжкой кожей, тканью, декоративными пленками.
Изготовление мелочевки, без которой не обойтись
В эту категорию относим в основном пластиковые детали, которые ломаются при демонтаже, теряются, пропадают (как это ни странно). Казалось бы, потеря крепежной клипсы или декоративной заглушки действительно мелочь. Но уже и обшивка начинает дребезжать, да и в глаза бросается отсутствие детали. Большая часть подобных комплектующих сделана из ABS или ПВХ пластика методом штамповки.
Мы предлагаем следующие решения по изготовлению таких элементов:
- Если речь идет о скрытых крепежных деталях, то необязательно восстановление в первоначальном виде.
Сделаем крепеж из металла или того же пластика, но с повышенным уровнем прочности. Прослужат такие элементы дольше, а внешний вид салона или кузова не пострадает.
- Заглушки, крышки, декоративные детали, корпуса зеркал восстанавливаем при помощи склеивания подходящих пластиковых заготовок или формированием новых с применением стекловолокна. После тщательной обработки поверхности покрасим с сохранением цвета и фактуры.
Если технической возможности по изготовлению сломанных или утерянных деталей нет или изготовление обойдется дорого, найдем другой, подходящий по стоимости вариант решения проблемы.
Какие технологии используем
Техническое оснащение сервиса позволяет решать задачи по изготовлению деталей различного уровня сложности. Не имеет значения форма изделий, перечень материалов, необходимых для производства, найдем решение для любых изделий. Количество текущих заказов на изготовление комплектующих подтверждает опыт мастеров, работающих в этом направлении.
Изготовление пластиковых деталей
На долю пластика приходится основная масса заказов. Детали отделки, кузовные элементы, крепеж, декор и защитные узлы все чаще делают с применением полимеров разных классов. Основная сложность — подобрать правильную технологию, ведь не все виды пластмасс поддаются пайке или склеиванию.
На практике применяем следующие способы изготовления деталей из пластиков:
- Штамповка при помощи специализированного оборудования.
- Склеивание и пайка отдельных элементов.
- Формирование деталей с применением стекло- и углепластика.
Получаемые изделия по прочностным характеристикам не уступают заводским элементам. А последующая шлифовка, покраска с применением предназначенных для пластиков лакокрасочных материалов позволяет реализовать любые дизайнерские задумки. Красим и в тон существующей отделке, и кардинально меняем цветовые акценты по желанию автовладельца.
Производство кузовных и декоративных деталей из металлов
Работаем и с цветными металлами, и со сталью. Выбор материала зависит от требуемой устойчивости к нагрузкам, воздействию коррозии, принятого вида декоративной отделки детали. При изготовлении применяем и листовые заготовки, и трубы, и прокат необходимого сечения. Гнем, режем, варим, в том числе и при помощи точечной или лазерной сварки. Есть оборудование для токарных и фрезерных работ. Поэтому делаем любые силовые и декоративные элементы.
В зависимости от назначения деталей применяем покраску, полировку, хромирование металлических изделий. По каждому из этих направлений имеется соответствующее оборудование. Обеспечим не только требуемый внешний вид, но и высокий уровень защиты металла от коррозии.
Деревянные элементы интерьера салона
Классический вид отделки, применяемый в автомобилях представительского класса. Деревянные вставки, элементы торпедо, центральной консоли, переходные рамки из дорогих материалов всегда актуальны в дорогих интерьерах салона. Но, учитывая стоимость таких декоративных элементов, к качеству подготовки и отделки поверхностей предъявляют более жесткие требования. И мы умеем работать по таким стандартам.
Изготовлением деталей занимается мастер, имеющий опыт работы краснодеревщиком. Макетирование и изготовление, шлифовка и полировка, тонировка и лакировка — каждый из этих этапов будет выполнен на эксклюзивном уровне. Вы можете убедиться в этом, оценив примеры наших работ.
Если у вас возникла потребность в изготовлении деталей для корпуса, кузова, отделки салона или инсталляции аппаратуры, приезжайте к нам. Поможем гарантированно. А в отдельных случаях подскажем более доступные по стоимости решения. Единственная просьба, оставьте заявку на сайте или позвоните заранее, это позволит подобрать удобное для вас время посещения сервиса.
Изготовление кузовных деталей | ZAVOD-DETALEJ.RU
Обращаясь в компанию Zavod-Detalej.ru вы обращаетесь к опытным специалистам занимающиеся изготовлением кузовных деталей. Мы в кротчайшие сроки произведем любые запчасти для кузовных автомобилей с учетом индивидуальных предпочтений.
Элементы деталей кузовов
Самым большим элементом каждого автомобиля считается его кузовная часть, она в большей степени устанавливает ключевые потребительские качества транспортных средств. Кузовная часть не является основным элементом конструкции, тем не менее, к его технологическим параметрам предъявляют довольно высокие требования, потому что, от качества изготовления кузова зависит несколько факторов:
- скорость машины;
- безопасность водителей и пассажиров;
- удобство;
- эстетические качества автомобиля.
Многие водители иногда сталкиваются с такого рода неприятностью, как повреждение кузовной части машины. Кроме деталей кузовов, мы предлагаем и изготовление деталей по образцу. Порча кузова полностью либо его единичных элементов, в основном наступает вследствие ДТП, некорректного использования автомобиля, хулиганских действий и других причин.
В отдельных случаях ремонт уже может не быть выходом из ситуации (возобновление геометрии кузовной части технически невозможен или экономически невыгоден) и необходима целостная замена элементов кузова.
Пришлите ваши чертежи или эскизы на [email protected]
Либо звоните 8-800-250-88-72. Доставка по России и СНГ!!!
Профессиональные сотрудники нашей компании помогут вам в подборе идеального варианта применения тех или иных элементов кузова вашего авто. Во многом благодаря современному техническому оборудованию, мы можем производить кузовные запчасти практически для всех автомобильных марок. Наши специалисты в короткие сроки и качественно произведут любые детали кузовной части из полимерного или металлического сырья:
- крыло,
- капот,
- крыша,
- двери,
- порог,
- обвес,
- бампер,
- радиаторные решетки,
- спойлеры и т.д.
Если вы желаете, то возможно изготовление кузовных деталей с измененными размерами и формой, а также создание обновленного кузовного дизайна.
Кузовные части автомобиля
Кузовная часть автомобиля – это один из основных составных. Обычно детали кузова производятся из высококачественной стали углеродистой. Даже имея незначительную толщину листа, они отличаются высокой прочностью, но повышенная влажность и дефекты могут приводить к образованию коррозии. Дорожно-транспортные происшествия также могут грозить куда более серьёзными проблемами.
Пришлите ваши чертежи или эскизы на [email protected]
Либо звоните 8-800-250-88-72. Доставка по России и СНГ!!!
В таких случаях необходима замена элементов, геометрическую форму которых восстановить не удается. В этом случае применяют специализированное оснащение, которое и помогает при изготовлении деталей трубопроводов и других изделий из металла. Нельзя обойтись и без фрезировальных, сверлильных, лентопилочных, шлифовальных установок. В период их подбора необходимо сосредоточить внимание на их качестве и кто производитель. Компания Zavod-Detalej.ru предлагает наилучшую технику, германские токарные станки обработки металла, которые обеспечивают выполнение множества технических процессов. За это время достигается необходимая степень безопасности, разгон скорости, первоначальная внешняя привлекательность облика запчастей, уют.
Кузовные элементы обязаны быть очень прочными. Важно также учитывать их лёгкость в производстве. В связи с этим применяют лиственную легированную. Недочетом этого материала считается высокая подверженность коррозии. Поэтому, после их штамповки и всех необходимых процедур проводят оцинковку. Чаще применяют специальный грунт. Перед его нанесением поверхность обрабатывают антижировым щелочным раствором. Затем наносят грунтовку, и деталь отправляют на сушку.
Алюминий же не имеет таких недостатков, именно поэтому потихоньку выталкивает сталь. Нельзя не сказать о лёгкости этого материала. Кузовная часть, изготовленная из алюминия, будет весить много меньше. Но также есть и другие особенности:
- низкая шумоизоляция,
- стоимость.
Для того чтобы избавиться от сторонних звуков и вибрации во время передвижения, необходима дополнительная шумоизоляция и качественное изготовление кузовных деталей. Ремонт таких элементов, производится с применением специализированного оборудования.
Изготовление кузовных деталей на заказ
Одной из услуг компании является изготовление кузовных деталей на заказ. Наше производство и профессиональный штат сотрудников поможет вам изготовить любые детали в хорошем качестве и не дорого для автомобилей – бампера, двери, капот, крышки багажника и все остальное. Наши производственные линии позволяют оперативно и точно в срок выполнять самые сложные заказы, как для стандартных авто, так и для раритетных (нестандартных моделей автомобилей).
Главные особенности работы
Предлагая заказчикам изготовление деталей на заказ – мы даем гарантию, что вся работа будет выполнена на самом высоком уровне и достойного качества.
Автомобильный кузов – это один из самых габаритных и дорогих частей автомобиля, именно от надежности кузова будет зависеть дальнейшая эксплуатация автомобиля. Вдобавок ко всему, кузов авто (детали) составляют основную эстетическую форму автомобиля, а также комфортность и, конечно же, безопасность автомобиля.
Пришлите ваши чертежи или эскизы на [email protected]
Либо звоните 8-800-250-88-72. Доставка по России и СНГ!!!
- Не всегда можно обойтись при повреждении кузова авто обычной починкой. В таких случаях будет требоваться индивидуальный подход для дальнейшей замены частей кузова авто.
- Безусловно, что на самые распространенные марки авто без труда сегодня можно подобрать запчасти практически в любом магазине, но если вы являетесь хозяином уникального и эксклюзивного раритета, то вряд ли сможете найти подходящую кузовную деталь – для этого обращайтесь к нам и мы выполним для вас изготовление кузовных деталей на заказ – оперативно и недорого.
Если вам необходимо в корне изменить внешний вид своего автомобиля, мы сможем подготовить для вас по индивидуальному заказу эскизы, чертежи по вашему пожеланию. К окончательной работе мы приступаем только после вашего согласования и утверждения проекта.
Если в восстановлении геометрии кузова после ДТП нет смысла, а кузовные части очень трудно найти, наши мастера недорого и быстро изготовят для вас самые качественные детали из разного заготовочного материала. В нашем цеху мы оперативно решаем любые сложные задачи и готовые предложить изготовление следующих видов деталей:
- Крылья.
- Капот.
- Крышу.
- Решетки.
- Бампера.
- Пороги.
- Спойлеры.
Почему доверяют именно нам?
Потому что изготовление кузовных частей и фрезеровка алюминия для нестандартных видов авто – это трудный технологический процесс, который требует обязательно командной, профессиональной работы – от дизайнеров до автомехаников. Не у всех компаний есть наличие такого персонала.
Предлагая клиентам ряд наших услуг – мы предлагаем гарантированный результат точно в срок. Обратившись к нам, вы получите прочные, надежные и долговечные кузовные детали для своего транспортного средства.
- Цена работ вас просто удивит. У нас нет скрытых и неоговоренных тарифов, работаем со всеми клиентами без исключения.
- Связавшись с нами, наш менеджер подробно по телефону объяснит вам, как будет состоять сотрудничество между нами и вами.
- Чтобы оставить заявку, свяжитесь с нами по почте или через сайт, дозвонитесь по телефону и можно считать, что вы наш клиент. Будем рады вашему обращению.
Самый дорогой и объемный элемент автомобиля – это его кузов. В большинстве случаев кузов является единым несущим элементом автомобиля, и в большей степени всегда определяет главные свойства (потребности) автомобиля.
Пришлите ваши чертежи или эскизы на [email protected]
Либо звоните 8-800-250-88-72. Доставка по России и СНГ!!!
От кузова зависит многое – эстетический вид авто, скорость, безопасность водителя и пассажиров, комфортная езда и т.д. По этой причине требования к кузову и его дополнительным характеристикам всегда должны оставаться на высоком уровне, поэтому детали должны быть выполнены качественно на всех этапах производства. Заказывайте у нас, и вы не пожалеете.
Изготовление кузовных деталей | ZAVOD-DETALEJ.![]() Обращаясь в компанию Zavod-Detalej.ru вы обращаетесь к опытным специалистам занимающиеся изготовлением кузовных деталей. Мы в кротчайшие сроки произведем любые запчасти для кузовных автомобилей с учетом индивидуальных предпочтений. Элементы деталей кузововСамым большим элементом каждого автомобиля считается его кузовная часть, она в большей степени устанавливает ключевые потребительские качества транспортных средств. Кузовная часть не является основным элементом конструкции, тем не менее, к его технологическим параметрам предъявляют довольно высокие требования, потому что, от качества изготовления кузова зависит несколько факторов:
Многие водители иногда сталкиваются с такого рода неприятностью, как повреждение кузовной части машины. Кроме деталей кузовов, мы предлагаем и изготовление деталей по образцу. В отдельных случаях ремонт уже может не быть выходом из ситуации (возобновление геометрии кузовной части технически невозможен или экономически невыгоден) и необходима целостная замена элементов кузова. Пришлите ваши чертежи или эскизы на [email protected]Либо звоните 8-800-250-88-72. Доставка по России и СНГ!!!Профессиональные сотрудники нашей компании помогут вам в подборе идеального варианта применения тех или иных элементов кузова вашего авто. Во многом благодаря современному техническому оборудованию, мы можем производить кузовные запчасти практически для всех автомобильных марок. Наши специалисты в короткие сроки и качественно произведут любые детали кузовной части из полимерного или металлического сырья:
Если вы желаете, то возможно изготовление кузовных деталей с измененными размерами и формой, а также создание обновленного кузовного дизайна.Кузовные части автомобиляКузовная часть автомобиля – это один из основных составных. Обычно детали кузова производятся из высококачественной стали углеродистой. Даже имея незначительную толщину листа, они отличаются высокой прочностью, но повышенная влажность и дефекты могут приводить к образованию коррозии. Дорожно-транспортные происшествия также могут грозить куда более серьёзными проблемами. Пришлите ваши чертежи или эскизы на [email protected]Либо звоните 8-800-250-88-72. Доставка по России и СНГ!!!В таких случаях необходима замена элементов, геометрическую форму которых восстановить не удается. В этом случае применяют специализированное оснащение, которое и помогает при изготовлении деталей трубопроводов и других изделий из металла. Нельзя обойтись и без фрезировальных, сверлильных, лентопилочных, шлифовальных установок. Кузовные элементы обязаны быть очень прочными. Важно также учитывать их лёгкость в производстве. В связи с этим применяют лиственную легированную. Недочетом этого материала считается высокая подверженность коррозии. Поэтому, после их штамповки и всех необходимых процедур проводят оцинковку. Чаще применяют специальный грунт. Перед его нанесением поверхность обрабатывают антижировым щелочным раствором. Затем наносят грунтовку, и деталь отправляют на сушку. Алюминий же не имеет таких недостатков, именно поэтому потихоньку выталкивает сталь. Нельзя не сказать о лёгкости этого материала.
Для того чтобы избавиться от сторонних звуков и вибрации во время передвижения, необходима дополнительная шумоизоляция и качественное изготовление кузовных деталей. Ремонт таких элементов, производится с применением специализированного оборудования. zavod-detalej.ru Изготовление деталей для автомобиля — AVTOkapitanВостребованные направления работПонятно, что браться за изготовление коленвалов, генераторов, КПП и других сложных конструктивных узлов нет смысла. Для решения задач такого плана подключаем проверенных поставщиков, способных найти комплектующие на любой автоэксклюзив. А вот мелочевка, нестандартные детали, изготовлением которых автопроизводители не занимаются, эти направления по силам нашим специалистам. Сервис укомплектован оборудованием для сварочных, токарных, штамповочных работ, формовки из полимеров, деревообработки. Производство конструктивных элементов для любителей экстримаСтандартная комплектация большинства машин мало предрасположена для эксплуатации в условиях бездорожья. Любителям рыбалки, охоты, путешествий паркетники — не помощники. А мы решим эту проблему и подготовим вашу машину к сложным условиям. Делаем и устанавливаем следующие конструктивные элементы:
Все узлы и крепежные элементы конструируем с учетом предполагаемых нагрузок. Используем металл, трубы с соответствующими прочностными характеристикам. Внешний вид силовых деталей подгоним под экстерьер машины, с применением различных технологий декоративно-защитной обработки поверхности. Кузовные детали для ценителей тюнингаГрамотно разработанные кузовные элементы улучшают внешний вид и динамические характеристики машины, сокращают расход топлива, повышают узнаваемость даже бюджетных авто в транспортном потоке. Именно по этим причинам тюнинг не теряет своей актуальности. В большинстве случаев делаем кузовные детали по индивидуальным чертежам с учетом вкусов автовладельца и особенностей машины. Среди наиболее популярных направлений, по которым работает сервис, выделим:
Делаем детали для спорткаров и ретроавтомобилей. При необходимости изготовим практически любой кузовной и конструктивный элемент, необходимый для восстановления старых машин. Комплектующие для инсталляции допоборудованияУстановка нештатного оборудования — всегда эксклюзивное решение, в реализации которого автопроизводитель ничем не поможет. Именно на этот сегмент приходится большинство заказов по изготовлению деталей. В основном это несложная в техническом плане мелочевка, но без нее никак не обойтись. Чаще всего у нас заказывают изготовление таких деталей:
Для изготовления используем дерево и фанеру, МДФ и металл. Эксклюзивные решенияНаряду с несложными деталями и комплектующими, делаем и сложные компоненты салона, способные повысить общий уровень комфорта в машине. Среди реализованных проектов отметим:
По каждому из заказов разработаем и реализуем индивидуальное решение, сделаем салон вашей машины неповторимым. В работе применяем пластики, металл, дерево с оклейкой или обтяжкой кожей, тканью, декоративными пленками. Изготовление мелочевки, без которой не обойтисьВ эту категорию относим в основном пластиковые детали, которые ломаются при демонтаже, теряются, пропадают (как это ни странно). Казалось бы, потеря крепежной клипсы или декоративной заглушки действительно мелочь. Но уже и обшивка начинает дребезжать, да и в глаза бросается отсутствие детали. Большая часть подобных комплектующих сделана из ABS или ПВХ пластика методом штамповки. Мы предлагаем следующие решения по изготовлению таких элементов:
Если технической возможности по изготовлению сломанных или утерянных деталей нет или изготовление обойдется дорого, найдем другой, подходящий по стоимости вариант решения проблемы. Какие технологии используемТехническое оснащение сервиса позволяет решать задачи по изготовлению деталей различного уровня сложности. Не имеет значения форма изделий, перечень материалов, необходимых для производства, найдем решение для любых изделий. Количество текущих заказов на изготовление комплектующих подтверждает опыт мастеров, работающих в этом направлении. Изготовление пластиковых деталейНа долю пластика приходится основная масса заказов. Детали отделки, кузовные элементы, крепеж, декор и защитные узлы все чаще делают с применением полимеров разных классов. Основная сложность — подобрать правильную технологию, ведь не все виды пластмасс поддаются пайке или склеиванию. На практике применяем следующие способы изготовления деталей из пластиков:
Получаемые изделия по прочностным характеристикам не уступают заводским элементам. А последующая шлифовка, покраска с применением предназначенных для пластиков лакокрасочных материалов позволяет реализовать любые дизайнерские задумки. Красим и в тон существующей отделке, и кардинально меняем цветовые акценты по желанию автовладельца. Производство кузовных и декоративных деталей из металловРаботаем и с цветными металлами, и со сталью. Выбор материала зависит от требуемой устойчивости к нагрузкам, воздействию коррозии, принятого вида декоративной отделки детали. При изготовлении применяем и листовые заготовки, и трубы, и прокат необходимого сечения. Гнем, режем, варим, в том числе и при помощи точечной или лазерной сварки. Есть оборудование для токарных и фрезерных работ. Поэтому делаем любые силовые и декоративные элементы. В зависимости от назначения деталей применяем покраску, полировку, хромирование металлических изделий. Деревянные элементы интерьера салонаКлассический вид отделки, применяемый в автомобилях представительского класса. Деревянные вставки, элементы торпедо, центральной консоли, переходные рамки из дорогих материалов всегда актуальны в дорогих интерьерах салона. Но, учитывая стоимость таких декоративных элементов, к качеству подготовки и отделки поверхностей предъявляют более жесткие требования. И мы умеем работать по таким стандартам. Изготовлением деталей занимается мастер, имеющий опыт работы краснодеревщиком. Макетирование и изготовление, шлифовка и полировка, тонировка и лакировка — каждый из этих этапов будет выполнен на эксклюзивном уровне. Вы можете убедиться в этом, оценив примеры наших работ. Если у вас возникла потребность в изготовлении деталей для корпуса, кузова, отделки салона или инсталляции аппаратуры, приезжайте к нам. avtokapitan.ru Изготовление ремонтных вставок сложной формы. — Community «Кузовной Ремонт» on DRIVE2Всем привет! Я приведу пример того, как именно были изготовлены две детали, сложившиеся в целую ремвставку чтобы проиллюстрировать сам принцип работы. А уж адаптировать его к конкретной задаче труда не составит ни у кого, я так думаю. Итак, задача: восстановить гнутую тонкостенную трубу и участок ее прохода через внутреннюю арку в БМВ е30. Zoom Деталей придется делать две — саму трубу и фрагмент арки, ее обрамляющий. Самый правильный и простой способ с трубой — найти такую же и согнуть. Но в реальности этот способ практически неосуществим, тонкостенные трубы лично для меня великая редкость, а уж тем более подходящего диаметра. Поэтому делаем трубу сами: Берем лист стали толщиной 0.8мм и подходящую по диаметру круглую оправку: Zoom С помощью молотка и тисков оборачиваем лист вокруг оправки, получаем заготовку для нашей трубы: Zoom В тисках же ставим прихватки, чтобы шов не расходился: Zoom И обвариваем полностью: Zoom Зачищаем, получаем такую вот трубу: Zoom Теперь трубу нам нужно согнуть, да еще и в двух плоскостях. Для этого делаем надрезы, оставляя небольшую перемычку, чтобы труба не рассыпалась на сегменты: Zoom Гнем по образцу: Zoom Постоянно контролируя форму в обеих плоскостях, подгибая перед каждым шагом расставляем прихватки: Zoom Провариваем все швы, зачищаем, получаем готовую трубу: Zoom Дальше нужно сделать фрагмент внутренней арки, сквозь который проходит труба. Zoom Дальше вырезаем с запасом лист 0.8мм, делаем в нем пропил: Zoom Прижимаем лист к спешл-тул с помощью мощных струбцин и подходящих прокладок: Zoom Используя подходящую круглую железку как пуансон и кувалду прессуем начерно выход для трубы. Я использовал молоток в качестве пуансона: Zoom После прессования выглядит сверху так: Zoom Снизу так: Zoom Правим получившуюся заготовки, переворачиваем и повторяем процесс. Сразу скажу, на словах все просто, а в жизни это многоходовка, в которой нужно чувстовать матер www.drive2.com Кузовные детали для корейцев, не оригинальные…кое что важное…) — DRIVE2Полный размер Неоригинальные кузовные детали (Фары, фонари, пластиковые детали – бампера, решетки радиатора и т.д., железные детали – крылья, капоты и т.д.) — иногда незаслуженно подвергаются «гонению» со стороны мастеров-жестянщиков, а точнее «недомастреров» с копытцами вместо рук – сегодня на рынке вполне возможно приобрести неоригинальную кузовную деталь вполне приличного качества. Нужно понимать, что стоимость оснастки для производства кузовных деталей – крайне высока, например, стоимость пресс-формы для бампера от 100 до 200 тыс.долларов. Таким образом, ни один производитель не в состоянии собрать у себя полный ассортимент запчастей собственного производства – существует большой рынок обмена запчастями у всех азиатских производителей, а отсюда детали близнецы от разных заводов, и даже из разных стран…Пресс-форма на какой-либо бампер или фару может существовать в единственном экземпляре в Азии, максимум в 2 или 3 -х экземплярах (на очень распространенные автомобили, такие как Нексия). На этом по кузовным деталям – пока все…Обещаю детективное продолжение этой темы в следующий раз )))… www.drive2.ru Металшейпинг. Изготовление крыла своими руками. ч1. — DRIVE2Ну, что ж дорогие читатели, сегодня я начну знакомить вас с безграничным миром металшейпинга. А если вы до сих пор не знаете, что это такое, то я вам поясню. Металшейпинг — это формовка изделий из листового металла. Вот например; есть у вас пикап 60х годов, а задних крыльев на него нет. Тут в дело вступаем мы с доктором Ватсоном и изготавливаем вам эти самые крылышки из обычного прямого листа кузовного декопира 0.8 Смотрите как это делается, все очень просто. для начала заимеем пикап. Он нам понадобиться, чтоб на нем сделать макет этих самых крыльев. как видно на этой фотографии крыльев ему ой как не хватает. . как только у нас появляется пикап, то у нас автоматически появляется возможность макетировать. Здесь главное не переусердствовать и ограничить свою фантазию чем-нибудь, например выбранным стилем. Итак. . затем на ней строим каркас. проволоку гнем об колени или еще обо что-нибудь, что будет под руками\ногами. наращиваем «кости» и с помощью сварочного полуавтомата в итоге получаем каркас-макет. . . на этом серьезная веха крылостроения закончена. Поздравляю! далее с макета снимаются выкройки. я разбил крыло на 5 элементов: низ перед, низ зад, середина, передняя щека, задняя щека. и стал газетные выкройки переносить на декопир. рутина . в итоге имеем это . в следующих постах я расскажу, как из прямого листа получить это . www.drive2.ru Кузовные запчасти. Критерии выбора — база знаний Kuzovnoy.Ru
Как известно, кузовной ремонт может включать в себя замену тех или иных элементов кузова. Иногда намного проще заменить, например, капот или крыло, нежели проводить сложные действия по восстановлению детали. ОригиналДля изготовления оригинальных деталей, которые поставляются для сборки автомобиля, используется определенная технология. Благодаря этому производятся детали, соответствующие всем конструкционным особенностям конкретного автомобиля и техническим требованиям, заложенным конструкторами. Кроме того, металлические оригинальные детали подвергаются специальной антикоррозийной обработке, которая надежно защищает деталь от появления коррозии. Цена душевного покоя
Приобретая оригинальную деталь, вы можете быть уверены в том, что при ее установке зазоры на автомобиле будут соответствовать заводским стандартам. Именно нарушения геометрии бывают причиной отказа некоторых мастеров от работы с неоригинальными запчастями. НеоригиналНеоригинальные детали до сих пор вызывают некое недоверие к качеству. А возникло оно в тот момент, когда российский рынок переполнили дешевые и некачественные китайские товары.
Понятие «неоригинал» стало именем нарицательным и звучало как синоним к слову «китай». Однако в последние годы отношение к неоригинальным кузовным деталям кардинально изменилось. На российском рынке автозапчастей широко представлена продукция европейских стран, отличающаяся очень хорошим качеством. Кроме того, хорошо зарекомендовали себя сертифицированные тайваньские запчасти известных брендов. К сожалению, подавляющее большинство китайских производителей и сейчас значительно уступает в качестве продукции своим конкурентам. Мифы и заблуждения
Технологический процесс изготовления оригинальных и неоригинальных деталей не отличается.
Часто можно услышать, что неоригинальные кузовные запчасти быстрее ржавеют. Из этого делается вывод, что в таких деталях металл тоньше. Но дело совсем в другом. Как уже было сказано, при изготовлении оригинальных деталей происходит очень эффективная антикоррозийная обработка. При изготовлении аналоговых деталей антикоррозийная обработка не проводится. И те и другие детали покрываются транспортировочным грунтом. Визуально оба покрытия выглядят одинаково, но при этом оригинальные запчасти защищены от ржавления, а аналоговые нет.
Далеко не все мастера добросовестно относятся к своей работе. Часто осуществляют покраску детали прямо поверх того самого транспортировочного грунта. Детали покрываются лакокрасочным покрытием только с внешней стороны. А с внутренней происходит беспрепятственное воздействие окружающей среды на всю площадь детали.
Такие «мастера» часто пеняют на некачественный неоригинал, хотя причина была в неправильной и некачественной обработке исходной детали при проведении ремонта. Несомненно, бывают случаи, когда запасная часть значительно не подходит по размерам. Причиной попадания бракованного изделия под реализацию является недостаточный контроль за качеством продукции (этим грешат малоизвестные бренды). Такие детали подлежат возврату. Основные производители аналогов на Российском рынкеНаилучшее качество показывают такие производители как Klokkerholm (Германия), AKG (Германия), R2A (Италия), Seima (Италия). Хорошим качеством обладают детали производства Capat (Италия), ARS (США), API (Тайвань), APR (Тайвань), TYG (Тайвань), Cryomax (Тайвань), AKSTE (Литва).
К деталям удовлетворительного качества можно отнести Aragon (Испания), ARP (Турция), ATL (Китай), TECHRAD (Китай). Также встречаются компании, которые закупают готовые детали и переупаковывают их под своим брендом. Поставщиками для них являются, в основном, китайские и тайваньские производители (хотя присутствуют и европейские бренды типа Klokkerholm или Capat). К таким компаниям относятся, в частности, «Signeda» и «Polcar». Среди ассортимента этих брендов можно встретить запчасти как хорошего, так и плохого качества. Заключение:Среди производителей неоригинальных запчастей есть главное различие — это качество продукции. Выбирая неоригинальные запчасти, помните, в погоне за ценой легко забыть о качестве детали. Это может значительно осложнить ремонт автомобиля. kuzovnoy.ru Из чего изготавливают кузов автомобиля? Какие материалы используются при производстве?Добрый день, сегодня мы расскажем о том, из чего изготавливают автомобильный кузов, какие материалы применяют при производстве, а также при помощи, каких технологий осуществляется этот важный процесс. КАК СОБИРАЮТ АВТОМОБИЛИ LEXUS И TOYOTA? Кузов любого автомобиля играет роль несущей конструкцией, в котором использовано при производстве огромное многообразие различных материалов и комплектующих. Чтобы кузов машины отслужил свой срок службы надежно, а также качественно, необходимо понимать, как за ним правильно следить и эксплуатировать. Чтобы это понимать, нужно знать из чего изготовлена несущая конструкция транспортного средства, а также какая технология сварки и производства применялась. Справочно заметим, что для изготовления кузова нужны сотни отдельно взятых запасных частей, компонентов и деталей, которые затем необходимо очень точно, а также грамотно соединить в единую конструкцию, которая будет объединять в себе все элементы транспортного средства. Чтобы изготовить прочный, при этом безопасный, легкий и по приемлемой стоимости кузов современного автомобиля, нужно постоянно искать различные компромиссы, а также новые технологии с материалами. 1. Изготовление кузова автомобиля из стали: преимущества и недостатки Большинство кузовов автомобиля, а точнее его детали изготавливается из разных сортов стали, алюминиевых сплавов и даже пластмассы с добавлением стекловолокна. Но основным материалом на сегодняшний день все же выступает низкоуглеродистая листовая сталь с примерной толщиной в 0,7-2 миллиметра. Благодаря использованию тонкого листа стали, автопроизводителям удалось уменьшить общую массу транспортного средства и при этом увеличить жесткость кузова. Высокая прочность кузова получается благодаря специальным свойствам и составу стали, а также его способностью к глубокой вытяжке, то есть можно изготавливать детали сложных форм. Кроме того, нельзя забывать, что новые технологии в сварке помогают получать высокотехнологичные соединения. Однако сталь обладает высокой плотностью и слабой коррозионной стойкостью, поэтому такой материал требует специальных дополнительных мероприятий для защиты от коррозии.
— низкая стоимость материала в сравнении с другим сырьем;
Отрицательные стороны стали при производстве автомобильных кузовов:
К таким видам материала относят такую марку стали, как TWIP, которая содержит большое количество марганца в своем составе, доля вещества может доходить до 25 процентов. Сталь такого типа обладает высокой пластичностью, устойчивостью к частым деформациям, благодаря чему материал можно подвергать относительному удлинению. Удлинение «ТВИП-стали» может происходит на 50-70 процентов, а пределом прочности служит показатель в 1450 МегаПаскаль. Для сравнения, прочность обычной стали составляет не более 250 МегаПаскаль, а высокопрочной до 600 МегаПаскаль. ЧТО ТАКОЕ КРУПНОУЗЛОВАЯ СБОРКА АВТОМОБИЛЕЙ? 2. Изготовление кузова автомобиля из алюминия: преимущества и недостатки Что касается автомобильных кузовов из алюминиевых сплавов, то их стали производить совсем недавно, примерно около 15 лет назад, для промышленности это считается маленьким сроком. Как правило, алюминий в автомобилестроении применяют для изготовления отдельных частей кузова, реже всего целиком. В большинстве случаев алюминий используется для производства капотов, крыльев, дверей, крышки багажника, а также прочих элементов и деталей. Автопроизводителями на сегодняшний день сплавы из алюминия используются в ограниченном количестве. Все это из-за того, что жесткость и прочность алюминиевых сплавов намного ниже, чем у той же стали. В связи с чем толщину деталей из этого материала производители увеличивают, поэтому значительного снижения массы готового кузова получить почти невозможно. ![]() Что касается производственного процесса, на котором изготавливают готовый алюминиевый кузов, то он очень схож с ранее описанной процедурой создания несущей конструкции из стали. На первой стадии, детали из листа алюминия подвергают штамповке, а затем собираются в единый цельный узел. При сварке применяется аргон, детали соединяются при помощи специальных заклепок или клея. На завершающей стадии, основные участки будущего кузова подвергают точечной сварке, а затем к стальному каркасу, изготовленному из труб разного сечения, прикрепляются кузовные панели и машино-комплекты. Положительные стороны алюминия при производстве автомобильных кузовов: — появляется возможность производства кузовных элементов любой формы и сложности;
Отрицательные стороны алюминия при производстве автомобильных кузовов: — высокая сложность ремонта деталей;
3. Изготовление кузова автомобиля из стеклопластика и пластмассы: преимущества и недостатки Что касается производства кузова из стеклопластика, то имеется в виду такой материал, как волокнистый наполнитель, который специально пропитывается полимерными смолами. Справочно заметим, что примерно 85 процентов пластмасс, которые применяются в автомобилестроении, приходятся на 5 основных видов материалов, такие как полиуретаны, поливинилхлориды, ABS-пластик, полипропилены и стеклопластики. Около 15 оставшихся процентов приходится на полиэтилены, полиакрилаты, полиамиды, поликрбонаты и прочие материалы.
— имея высокую прочность, деталь имеет небольшой вес; — внешняя поверхность элементов обладает оптимальными декоративными параметрами; — простота изготовления элементов, которые имеют сложную форму; — имеется возможность производства деталей крупных размеров. Отрицательные стороны стеклопластика при производстве автомобильных кузовов: — сравнительно высокая цена на наполнители; — высокие требования к точности форм, разметке и готовой детали; — производство деталей осуществляется продолжительное время; — высокая сложность в ремонте при повреждении деталей.
autoblogcar.ru Изготовление деталей из стеклопластика — Opel Astra, 1.6 л., 2011 года на DRIVE2Практическое руководство для тюнеров! Материалы 2. СмолаВыбирайте те, которые больше подходят для наземного транспорта: не слишком хрупкие, обладающие некоторой эластичностью после застывания. Смола не должна быть слишком густая, нужно чтобы она легко пропитывала стекломат.Д ля мелких деталей смолу лучше использовать специализированную, а для порогов, бамперов, сабвуферов сгодится дешевые разновидности для судостроительства, склеивания и даже для заливки и выравнивания полов в помещениях (этот сорт я встречал на рынках, продается в крупной таре) также Полиэфирные смолы 3. 4. Разделительный составЭто может парафин (из него бывают наборы, им лыжи и сноуборды натирают), полироль для паркета (один из лучших вариантов), стеарин (из него свечки делают), специальные составы. Наносится на поверхность детали (матрицы) и спустя некоторое время энергично располировывается шерстяной тканью или войлоком. Изготовление макетов при помощи монтажной пены. «Пример» Изготовления накладок на бампер Бампер защищается от брызг. На живой машине с дорогой краской вообще все заклеивается. Затем контуры будущего бампере заполняются монтажной пеной. Не стоит пену сразу оклеивать стеклотканью. Обрезанную пену сначала шкурят (чем ровнее она будет, там меньше расход шпатлевки), а затем оклеивают плотной бумагой. Затем все оклеевается тонкой стеклотканью пропитанной эпоксидкой… Сначала лучше оклеить порошковым стекломатом, для ровности, а уж затем эмульсионным. Смолу готовить порциями не более 500 грамм, иначе затвердеет. Максимальной прочности смола достигнет за 24 часа. Количество слоев стеклоткани зависит от предполагаемых нагрузок. Шкурить орбитальной шлифовалкой с зерном не более 80. Первый слой шпатлевки ТОЛЬКО со стекловолокном. Иначе потрескается от мелких ударов. Затем шкурить поверхность шкуркой с зерном 220 или 320. ![]() Конечный результат, без покраски. Изготовление лепных макетов Изготовление различных деталей при использовании каркасов и радиоткани Информация взята с fiber-xl.narod.ru/fiber.htm#peno Если понравилось, не забудь ткнуть пальцем www.drive2.ru Изготовление стеклопластиковых деталей для автомобилейСреди всех товаров компании «Стеклопластик СПб» кузовные детали из стеклопластика обладают особой популярностью. Стеклопластик широко применялся для тюнинга деталей, это объясняется простотой обработки материала. Например, стоит задача снизить вес автомобиля. Замена кузовных элементов на стеклопластик — идеальное решение. Но со временем становилось все меньше кузовных деталей из металла и появлялось все больше из пластика. Важно не путать стеклопластик с АБС-пластиком. Для промышленных масштабов АБС-пластик идеальный материал, с ним легко работать и не требуется ручная обработка. Стеклопластик более сложен в производстве, но его характеристики лучше. Теоретически, данный композитный материал можно изготовить самостоятельно в домашних условиях. Установка деталей из стеклопластикаПрочность стеклопластиковых кузовных деталей во многом зависит от качества изготовления. Не стоит бездумно заменять металлические элементы кузова на стеклопластик. Никто не проводил краш-тесты автомобилей, в которых заменены детали на другой материал. Ведь установка неоригинальных деталей кузова — это воздействие на конструкцию автомобиля. Не всегда это серьезное воздействие. Замена передних крыльев никак не повлияет на безопасность. Но установка стеклопластиковых порогов или навесного железа — опасное мероприятие, не стоит вносить изменения в запрограммированную клетку сминаемых зон. Многих автовладельцев заинтересовали стеклопластиковые детали низкой ценой и высокой прочностью. Чаще всего их волнует — не будет ли проблем с установкой, не появятся ли зазоры. Проблемы с установкой возникают только в том случае, если кузовные элементы изготовлены не качественно. Производство деталей для авто«Стеклопластик СПб» производит кузовные детали из стеклопластика для многих автомобилей. Несколько лет назад выбор был ограничен. В основном деятельность была направлена на автомобили, ресурс которых зависел от состояния кузова. Сейчас компания предлагает детали на все популярные автомобили. На данный момент самыми востребованными элементами кузова из стеклопластика являются:
stekloplastik.spb.ru Информация о неоригинальных кузовных деталяхНеоригинальные кузовные детали (Фары, фонари, пластиковые детали – бампера, решетки радиатора и т.д., железные детали – крылья, капоты и т.д.) — иногда незаслуженно подвергаются «гонению» со стороны мастеров-жестянщиков, а точнее «недомастреров» с копытцами вместо рук – сегодня на рынке вполне возможно приобрести неоригинальную кузовную деталь вполне приличного качества. Правда нужно знать кое-какие нюансы, о которых речь пойдет ниже: Нужно понимать, что стоимость оснастки для производства кузовных деталей – крайне высока, например, стоимость пресс-формы для бампера от 100 до 200 тыс.долларов. Таким образом, ни один производитель не в состоянии собрать у себя полный ассортимент запчастей собственного производства – существует большой рынок обмена запчастями у всех азиатских производителей, а отсюда детали близнецы от разных заводов, и даже из разных стран…Пресс-форма на какой-либо бампер или фару может существовать в единственном экземпляре в Азии, максимум в 2 или 3 -х экземплярах (на очень распространенные автомобили, такие как Нексия). autoparts69.ru Детали кузова для вторичного рынкаНа первый взгляд, кузовные детали может выпускать любой механический завод, имеющий прессовое производство. Но такое впечатление обманчиво. Кому из производителей можно доверять ? «Кузовщина» – дама капризнаяДа, капризная. И мастера кузовного ремонта знают это лучше других. Жестянщик не всякое крыло возьмется ставить, а если и возьмется, предупредит: изделие не «родное», вот тут зазор будет увеличенным. Или, положим, у этого капота «родовая травма», он деформированный. К правому брызговику прилегает нормально, а у левого образует горб. А на двери, которую вы привезли, пятна ржавчины и щелевая коррозия в отбортовках. Почему? А потому, что металл просто «черный», не защищенный фосфатированием и грунтованием. Полежала деталь под открытым небом и «зацвела». Ладно, скрепя сердце соглашается мастер, поставлю вашу деталь, покрашу, но претензий не принимаю. Адресуйте их тому, кто эту «жестянку» выпускает. Что делать владельцу битой «Лады»? Искать кузовные детали, выпущенные АВТОВАЗом? Вовсе необязательно, и мы постараемся это доказать в следующих разделах статьи. Альтернатива «оригиналу»Координатно-измерительное оборудованиеОбратим взор на производителя, чья продукция не уступает тольяттинской. Это ПО «Начало» из Набережных Челнов. Вот уже более двух десятилетий эта компания снабжает наши автомобили тормозными колодками, дисками сцепления, шаровыми опорами, рычагами подвески и другими автокомпонентами. Есть в ассортименте предприятия и кузовные детали. Впрочем, есть – это слабо сказано. По данной продукции ПО «Начало» безусловный лидер вторичного рынка. Судите сами: ежегодно предприятие выпускает около миллиона кузовных деталей, охватывая большинство марок и моделей российских автомобилей и рестайлинговых модификаций. Ассортимент насчитывает более 100 наименований – это двери, капоты, крылья, панели крыши, разнообразные защиты картера, рамки радиатора, балки и другие изделия и комплектующие (например, усилители капота). Внушительно. Впрочем, широтой да размахом нашего читателя не удивишь. Он человек прагматичный, а потому сразу поинтересуется: а как там с качеством? Чтобы ответить на этот вопрос, определимся со слагаемыми этого самого качества. Применительно к деталям кузова они таковы: – высококачественная листовая сталь с «правильной» микроструктурой; – точная штамповая оснастка, мощные прессы и неукоснительное соблюдение технологических требований; – контроль качества изделий, гибкая обратная связь с производством. А теперь пройдем по означенным пунктам. МеталлСталь, применяемая в листовой штамповке, должна быть достаточно пластичной, чтобы «течь» в штампе и не рваться даже при глубокой вытяжке. В ней недопустимы посторонние включения, выходящие за рамки ТУ, – это изначальное условие коррозионной стойкости будущей детали. Требуемым условиям полностью отвечает холоднокатаный листовой прокат из низкоуглеродистой качественной стали по ГОСТ 9045-93. Именно такая сталь поставляется для производства кузовов на автозаводы. Она же поступает в цеха ПО «Начало». Это – первая причина, по которой кузовные детали, выпускаемые под торговой маркой «Начало», полностью соответствуют оригинальным запасным частям производителя автомобилей. Первая, но не единственная. Усилитель капотаШтамповая оснасткаШтамп – точнейший инструмент. То, что он призван обеспечивать размеры и геометрию изделия, понятно. Но это еще не все. Важно, чтобы по окончании штамповки в детали не возникали паразитные остаточные напряжения. Тогда крыло, встав на кузов, не пойдет винтом, а капот не станет «горбить». Как учесть эти тонкости? Начнем с того, что кузовные детали марки «Начало» производятся по оригинальным ТУ и чертежам. Для большей части ассортимента предприятие изготавливает штампы самостоятельно, в собственном инструментальном цехе. Разработка и проектирование штампов ведется с помощью систем автоматизированного проектирования – САПР. Впрочем, сегодня в ходу англоязычная аббревиатура CAD – Computer Aided Design. Но сути это не меняет. Для обеспечения идеальной «стыковки» детали с заводским кузовом (да простят меня читатели за «космические» термины) применяется математическое моделирование рабочих поверхностей штамповой оснастки. И вот цифровая модель штампа в памяти компьютера. Наступает этап ее «материализации». Это поручается высокоточному фрезерному станку с ЧПУ (по-английски – Computer Numeric Control, сокращенно CNC). В итоге точность полученного штампа – идеальная, время освоения новых изделий – минимальное, человеческий фактор практически отсутствует. Но что важно: на стадии подготовки производства штамповал и сварочная оснастка проходит многократные проверки на соответствие 30-модели, созданной по заводскому чертежу детали. Для контроля используется современное координатноизмерительное оборудование HERA SP 12-9-7 (Италия) и КИМ FARO Platinum 10 с лазерной сканирующей головкой (Швейцария). В итоге форма и размеры штампуемых кузовных деталей в точности соответствуют оригинальным изделиям. Так что со штамповой оснасткой в ПО «Начало» полный порядок. Прессы и технологииДля штамповки кузовных деталей на заводе ПО «Начало» используются немецкие и отечественные кривошипные прессы усилием от 400 до 1000 тс, установленные в три линии. Во главе каждой – прессы двойного действия усилием 500 и 1000 тс, позволяющие получать сложные детали, в том числе требующие операции глубокой вытяжки. Подобную «тяжелую артиллерию» может себе позволить далеко не каждое предприятие. Сама схема кривошипно-шатунного механизма позволяет получать выгодные кинематические характеристики ползуна, в частности – скорость инструмента, называемую еще скоростью деформирования. А она тесно связана с другой характеристикой – скоростью деформации самого материала изделия, чрезвычайно важной для правильного «течения» металла. Кинематика, точная настройка оборудования плюс прецизионный штамп, о чем уже говорилось, – вот главные условия, чтобы в момент окончания штамповки деталь не имела остаточных напряжений – тогда ее точно не поведет. Едет крышаСкажем и о новинках – ведь ассортимент предприятия непрерывно расширяется. Как ни странно, при авариях нередко повреждается крыша автомобиля. Да настолько, что требует замены. Идя навстречу пожеланиям рынка ремонтных услуг, ПО «Начало» в мае 2013 года освоило производство панели крыши для автомобилей «десятого» семейства (каталожный номер 2110-5701012-10). А в этом году предприятие начало выпускать панель крыши для автомобилей 2108 (каталожный номер 2108-5701012). Е1овые изделия являются полными аналогами панелей заводского производства, что подтверждено многочисленными испытаниями. При освоении указанных панелей возникла интереснейшая задача – обеспечение точных сопряжений с остовом заводского кузова. Flo если вы внимательно прочитали предыдущие разделы, то уже поняли – задача эта была успешно решена. И вот деталь изготовлена – в допуске, без паразитных напряжений. Перед отправкой потребителю ее надо оградить от внешних воздействий, прежде всего атмосферных. Для этого на предприятии имеются цеха гальванопокрытий и окраски. Например, для защиты от коррозии деталь обезжиривают в щелочном растворе, фосфатируют, покрывают грунтовкой BMЛ и подвергают горячей сушке при температуре 180°С. Для обработки используется метод окунания, благодаря чему грунтовка ложится ровно, без подтеков, заполняя все полости, недоступные для кисти и распылителя. Говоря о контроле, отметим, что на заводе давно действуют системы качества ISO. Это означает, что отслеживание качества изделий происходит на всех производственных этапах, вплоть до упаковки, транспортировки и анализа отзывов потребителей. ЭпилогНадеемся, что читатели убедились в привлекательности кузовной продукции, выпускаемой героями нашего рассказа. А мы отметим, что ПО «Начало» намерено и дальше расширять ассортимент деталей. И поскольку это предприятие все делает самостоятельно, в строгом соответствии с нормативами автозавода, и к тому же применяет новейшие технологии, можно не сомневаться: качество «началовских» изделий всегда будет идентично оригинальным «вазовским», а стоимость – существенно ниже, что по достоинству оценено рынком запчастей. Так что мастер, упомянутый в начале нашего рассказа, ворчал на другую «жестянку». Не ту, что выпускает ПО «Начало». abs-magazine.ru |
Кузовные детали из степлопластика заказать в Минске
Мы занимаемся изготовлением кузовных деталей из стеклопластика.
Заказ по телефонам:
Стеклокомпозит все чаще заменяет металл в автомобильной индустрии благодаря своим характеристикам: обладает высокой прочностью, выдерживает высокие температуры и влажность, при этом значительно меньше весит.
В случае отсутствия детали на складе изготовим под заказ в течении трех суток.
Стеклопластик — недорогой композитный материал из стекловолокнистого наполнителя. Активно применяется в промышленности, строительстве, машино- и судостроении как замена стали. Наделен рядом преимуществ:
- прочность;
- устойчивость к перепадам температуры и высоким показателям влажности;
- не трескается;
- не поддается коррозии;
- малый вес.
Кузовные детали из стеклопластика изготавливаются на замену металлическим. Крыло или дверца автомобиля, выполненное из стеклокомпозита будет прочнее, чем заводское из стандартных материалов. Выдержит, к примеру, попадание крупным камнем. Там, где на металле уже давно появится вмятина, на стеклопластике, скорее всего, придется лишь немного обновить поцарапанную краску.
Двери из стекловолокна в Минске
Выправление возможных вмятин также представляется возможным. Необходимости заново менять деталь из-за небольшого повреждения не возникнет.
Изготовленные из стеклопластика детали автомобиля не подвержены коррозии, что обеспечивает более высокий срок службы без финансовых затрат.
Заказывая у нас стеклокомпозитные капоты, дверцы, крылья, клиент получает деталь, уже имеющуюся на складе. Если необходимого элемента нет в наличии, изготовление занимает до трех дней.
На данный момент компания «Савим-авто» изготавливает только детали из указанного на сайте перечня по актуальным ценам. Производство отточено, а потому любая деталь становится на нужное место без зазоров и скосов, смотрится, как заводская.
Изготовление деталей из стеклопластика
ВНИМАНИЕ! СОТРУДНИЧАЕМ С КЛУБАМИ! РАЗРАБОТКА, ИЗГОТОВЛЕНИЕ, «КЛОНИРОВАНИЕ» РАЗЛИЧНЫХ КУЗОВНЫХ ДЕТАЛЕЙ АВТОМОБИЛЕЙ, МОТОЦИКЛОВ и СНЕГОХОДОВ СРЕДНИМИ И МАЛЫМИ ТИРАЖАМИ.E-mail: [email protected]
Новые примеры работ буду выкладывать на форуме и на моей страничке
Если суммировать, сколько труда, нервов, времени,
денег, материалов было потрачено на то, чтобы получить опыт, которым я поделюсь
в этой статье, и вложить в одну машину, то получится такая ультра-телега,
что мне и представить страшно :-))) Обрывки материалов были добыты из Интернета
(большей частью не русскоязычного), литературы, часть у мастеров тюнинговых
контор, большинство которых упорно не хотели делиться ценным опытом (не относится
к некоторым мастерам фирм ТРИ-ABC™ и LIT-company™)
и мне зачастую приходилось изображать из себя любопытного и придирчивого клиента,
какая-то доля материала была великодушно передана мне такими же энтузиастами
как и я, теми, кто питается только пиццой и шаурмой с пивом и спит по два
часа в сутки, и наконец к какой-то части решений пришел я, по несколько раз
переделывая одну и ту же деталь :)) Надеюсь, что из-за этого «сверхсекретного»
материала я все же не подвергнусь преследованию со стороны тюнинговых контор
— производителей обвесов.
Стеклопластиковые детали практически любой сложности можно изготовить буквально на коленке в гараже. Они не требуют специального оборудования и помещений. Стеклопластик очень универсальный материал. Из него можно изготовить все, начиная от ресничек на фары и кончая кузовными панелями. Стеклопластиковые детали при правильном изготовлении очень прочны и долговечны. Было бы также полезно знать, что цена таких изделий при самостоятельном изготовлении очень низка, гораздо ниже той, по которой они продаются. На одном провинциальном заводике по производству ламината (что-то типа шифера, только из стеклопластика) я был свидетелем изготовления копии обвеса от фирмы
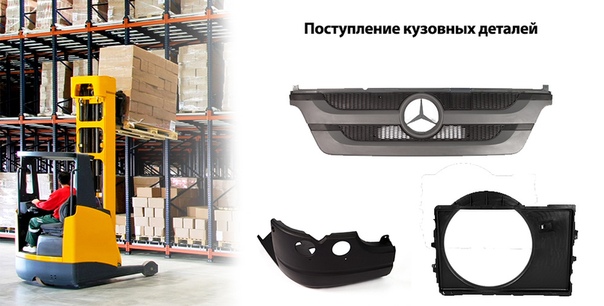
Прежде чем браться за работу прикиньте, есть ли для этого условия? Условие первое: наличие времени. Если жена, дети под ногами путаются, отвлекают, то возникнут проблемы. С ними надо разобраться до начала работ. Любовь нечаянно нагрянет, когда жену совсем не ждешь… Мне было проще: у меня никого, кроме желания сотворить что-нибудь прикольное, нет. Работа по ночам меня совсем не пугала. «Первым делом мы испортим самолеты, ну а девушек…». Условие второе: рабочее место. Если негде делать, то лучше и не пытаться. Когда-то мне приходилось работать и зимой в неотапливаемом гараже, и на улице, и в коридоре в квартире. Придумайте какую территорию захватить на время творчества. Итак, вступление окончено, можно начинать. Имейте в виду, что на этот процесс можно подсесть не хуже чем на наркотик, из Вашей головы будет идти пар как из чайника со свистком, все только начинается.
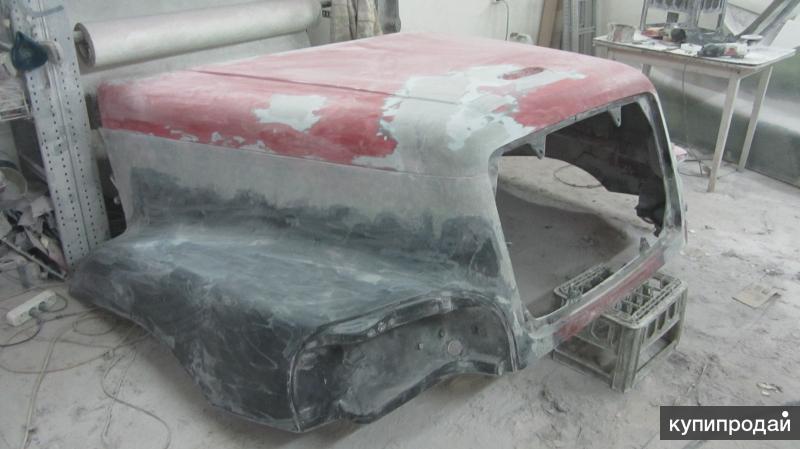
1. Инструмент.
2. Материалы.
3. Вступление
4. Макетирование.
5. Изготовление макетов из пенопласта
6. Использование монтажной пены.
7. Адаптация бамперов и их фрагментов.
8. Лепные макеты.
9. Использование радиоткани.
10. Раскройка листовых материалов.
11. Матрицирование.
12. Выклейка изделия.
13. Дополнения.
14. Покраска
Для начала стоит ознакомится с тем инструментом,
который понадобится в любом случае, вне зависимости от типа детали и способа
изготовления:
1. Хорошие портновские ножницы.
Придется очень часто резать стеклоткань и от качества выкроек зависит и качество
конечного изделия. Особенно к качеству выкроек требователен порошковый стекломат.
Подготовка «комплекта» армирующих материалов, специально раскроенных
по форме используемой матрицы, экономит время и снижает количество отходов.
2. Канцелярский нож и набор лезвий к нему.
То же что и п.1.
3. Металлическая линейка 40-50 см.
Пригодится при резке выкроек и замерах.
4. Набор кистей. Служит
для укладки стеклоткани и пропитки ее полиэфирной смолой. Можно также запастись
роликами (наподобие тех, что применяют в шиномонтаже) и валиками (для прокатки
больших площадей). Иногда может пригодится губка.
5. Болгарка (отрезная машинка).
Можно конечно обойтись и ножовкой, но края у матриц и готовых изделий удобнее
подрезать болгаркой. Запаситесь к ней кругами по камню, так как стекловолокно
очень быстро сжирает диски по металлу.
6. Дрель. Пригодится
для изготовления сборных матриц, замешивания эпоксидки, заворачивания саморезов
и прочего дыркосверления. Очень приветствуется наличие сверл и фрез диаметром
20-80мм.
7. Лист стекла
(40х40см). На нем удобно пропитывать кусочки стеклоткани эпоксидкой.
Ни капли не пропадет зазря.
8. Шлифовальный брусок.
Шлифок. Очень хорошо если у Вас будет набор различных размеров и форм (для
вогнутостей цилиндры, для больших плоскостей «рубанок» приблизительно
6х40 см и т.д.). Помимо всех прочих полезно иметь еще и резиновый брусочек
6х10 см. Очень облегчат работу пневматические или электрические инструменты:
круглая орбитальная шлифовальная машинка и «рубанок». Если деталь
большая (капот, крыло) без шлифмашинки за работу лучше не браться.
9. Набор шпателей. Металлические
и резиновые. Для больших плоскостей (капоты, крышки багажников, прямые участки
бамперов и др.) нужен металлический шпатель шириной примерно 40 см.
10. Емкость для смолы.
Если используется хорошая смола застывающая за 30-40 минут, то вполне хватит
емкости до одного литра. Требования к емкости простые: чем больше площадь
и меньше глубина, тем лучше: смола дольше не схватывается. Я использовал пластиковые
банки из-под соленой селедки, они гибкие и из них легко вытряхнуть застывшую
смолу.
11. Лобзик электрический.
Его ждет изготовление каркасов, шаблонов, растяжек матриц и тому подобное.
В случае его отсутствия придется пилить все ножовкой.
12. Ножовка (по металлу).
Полезное дополнение, а иногда и замена пунктам 5 и 11.
Материалы, используемые при изготовления деталей из стеклопластика.
Их конечно лучше приобрести в фирмах занимающихся их поставкой, там обычно
все объясняют, подберут то что больше подходит в Вашем случае. Я брал все
материалы в www.igc-composite.com.
Итак:
1. Армирующие материалы.
В это определение входят три вида материала. Первый: Стекловуаль.
«Легкий и воздушный» подвид эмульсионного стекломата. «Эмульсионного»
потому что лучше всего использовать для работы нетканый стекломат, волокна
которого скреплены эмульсией, растворяющейся под действием смол. Такой вид
материала легче принимает требуемую форму чем ткань, хотя ткань прочнее. Итак
стекловуаль. Нам потребуется с плотностью от 30 до 100 г./м.кв. Её используют
для наружных слоев, так как она позволяет изготовлять изделия с высокой сложностью
поверхности. Второй вид: стекломат плотностью от 300 г./м.кв.
до 450 г./м.кв. Он позволяет набрать толщину изделия. Цитата: «Маты различной
плотности из рубленых комплексных нитей на основе низкощелочного стекла Е.
Материал мягкий, легко поддается формованию и используется при производстве
изделий сложной формы. Ламинаты, изготовленные из данных матов, демонстрируют
хорошие механические свойства и высокую сопротивляемость атмосферным условиям
в течение длительного периода.
» И третий вид: порошковый
стекломат плотностью от 300г./м.кв. Иногда его называют поликором. Вклеивая
его между несколькими слоями эмульсионного стекломата Вы придадите изделию
гораздо большую прочность. Он практически не впитывает смолу и обладает приличной
толщиной. Зачастую вклеивается лишь отдельными полосками. Я пользовался стекломатом,
выполненным на основе микросфер. Цитата: «Маты различной плотности из
рубленых комплексных нитей на основе низкощелочного стекла Е, на порошковом
связующем. Быстро пропитываются и обеспечивают получение гладкой поверхности.
Ламинаты, изготовленные с использованием порошковых стекломатов, обладают
высокой прозрачностью (технический термин, не путать с прозрачностью стекла),
хорошими механическими свойствами и устойчивостью к атмосферным воздействиям.»
Приходилось использовать Kevlar 9065K и Kevlar K931(Тканый
материал саржевого переплетения на основе арамидных волокон. Плотность — 190
и 340 г/м.) Получается еще не карбон, но уже не стеклопластик. Бампера обладают
повышенной деструктивной способностью 🙂
2. Смола, она
и в Африке смола. Правда смолы разных фирм могут весьма ощутимо отличаться
по свойствам и качеству. Выбирайте те, которые больше подходят для наземного
транспорта: не слишком хрупкие, обладающие некоторой эластичностью после застывания.
Смола не должна быть слишком густая, нужно чтобы она легко пропитывала стекломат.
Я использовал CRYSTIC 196 PA компании SCOTT BADER™. Это
предускоренная ортофталевая полиэфирная смола с высокими прочностными, механическими
и электрическими свойствами. Короче, то что доктор прописал. К смоле соответственно
должен прилагаться отвердитель и по возможности катализатор, ускоряющий процесс
полимеризации (застывания). Требуемое для изготовления ламината количество
смолы можно рассчитать путем взвешивания предполагаемого к использованию армирующего
материала. Для рубленого стекломата отношение смолы к стекловолокну должно
находиться в пределах от 2,3:1 до 1,8:1 (содержание стекла 30-35%). Для тканого
ровинга рекомендуется соотношение 1:1 (содержание стекла 50%), тогда как отношение
смолы к стекловолокну при использовании комбинированных материалов различно
и зависит от структуры отдельного вида используемой ткани. Для снижения вязкости
смолы ее можно нагреть градусов до 50 С или разбавить ацетоном, растворителем
для лаков и денатурированный спиртом (лучше растворитель, один вдох и ощущение
— как будто проглотил заячью шапку с ушами) Количество растворителе не должно
превышать 5% от массы смолы. Долг, к сожалению, платежом красен: при добавлении
в смолу 5% растворителя для лаков ее прочность падает на 35% — серьезный удар
по механическим свойствам. Растворитель может вызвать усадку смолы. Присутствие
растворителя в смоле может повредить поверхность макета.
Многие материалы
( например , пенополистирол) хорошо переносят эпоксидную смолу , но не переносят
присутствия в ней растворителей . Поэтому прежде чем добавить в смолу растворитель
, заранее убедитесь в его безвредности для макета.
И еще: приняно все смолы называть эпоксидными, но я работал и с ПОЛИЭФИРНЫМИ
СМОЛАМИ, которые существенно дешевле. Не стоит пренебрегать различными наполнителями
для смол, например добавка в смолу графитового порошка дает поверхность гладкую
и очень напоминающюю карбон (особенно при использовании прозрачного гелькоута
и смолы, тканых армирующих материалов).
Д ля мелких деталей смолу лучше использовать специализированную, а для порогов,
бамперов, сабвуферов сгодится дешевые разновидности для судостроительства,
склеивания и даже для заливки и выравнивания полов в помещениях (этот сорт
я встречал на рынках, продается в крупной таре).
3. Гелькоут. Покрытие
матриц и конечных изделий защищающее и улучшающее поверхность. Помогает устранить
рельеф, вызванный структурой стеклоткани и в какой-то степени помогает избавиться
от пузырьков воздуха на поверхности детали. Его наносят первым слоем, дают
ему схватится, а уж затем приступают к выклейке изделия. Я использовал CRYSTIC
65 PA водо- и атмосферостойкий предускоренный тиксотропный изофталевый гелькоут
для ручного нанесения. Но часто обходился без него, компенсируя его отсутствие
смолой с мелким наполнителем (графитовый порошок, гипс) или жидкой шпатлевкой.
Ей можно покрывать как конечную деталь, так и матрицу (не забудте вышкурить
800й шкуркой с водой).
4. Разделительный состав.
Это может парафин (из него бывают наборы, им лыжи и сноуборды натирают),
полироль для паркета (один из лучших вариантов), стеарин (из него свечки делают),
специальные составы. Наносится на поверхность детали (матрицы) и спустя некоторое
время энергично располировывается шерстяной тканью или войлоком. Служит например
для того, чтобы Вы без труда смогли извлечь готовую деталь из матрицы. Если
есть возможность покупайте Mirror Glaze #8 фирмы Meguiar`s (им ботинки хорошо
еще чистить), но можно использовать полироли для кузова на основе воска или
силикона, например такие как ABRO silicone car wax. Такими полиролями не удастся
заполнить все поры и дефекты покрытия, но они могут быть неплохим дополнением
к парафину. Я слышал о использовании полиролей для обуви (с гуталином не путайте)
и мебели на восковой основе, но не могу ничего сказать о достигнутых результатах,
скорее всего они удолетворительные. Два экстремальных состава: солидол и мыло.
Их используют когда поверхность с которой снимают слепок, очень плохого качества.
Мыло можно чуть-чуть смочить водой.
Также в таких случаях подойдет тонкая
пищевая пленка.
5. Шпатлевка. Я использовал
продукцию фирм CAR SYSTEM, Dyno Coat и иногда BODY. «Шпатля» бывает
следующих видов: Fiberglass (со стекловолокном), там где пребуется прочность
или наносится толстый слой, SOFT или EXTRA там где приходится много шкурить
или для конечной отделки. NITRO (лучше брать качественную, от известных фирм-меньше
вероятность появления трещин) очень помогает разобраться с мелкими дефектами.
Также пригодится жидкая шпатлевка для окончательной доводки детали. Никогда
не позволяйте себе делать слои шпатлевки более 3мм — лучше в этом месте положить
еще пару слоев стеклоткани.
6. Прочее. Весьма пригодится
запас саморезов укомплектованный отверткой и набор струбцин для фиксации,
пара мотков скоча обычного и малярного, шкурка всех калибров (приличные материалы
у 3М и Mirka, русской шкурка быстро забивается, особенно при использовании
низкосортной шпатлевки), тряпки, растворитель 646 или 650, ацетон, обезжириватель.
Могут понадобится грунтовка, краска, фанера, листовой пластик, пенопласт,
гипс, металлические уголки ну и много всего другого. По ночам еще спать очень
хочется… в итоге был приобретен сахар-песок (два бархана) и кофе в ампулах
Я не смогу описать все детали, которые можно
изготовить из стеклопластика — это нереально. Не смогу также описать все способы
работы со стеклопластиком, все тонкости этого ремесла, так как это равносильно
написанию целой книги. Внутри каждой большой задачи сидит маленькая, пытающаяся
пробиться наружу. Как смогу опишу все те способы, которыми пользовался я сам
в различное время и подводные камни с которыми сталкивался. Своих фотографий
для иллюстраций всех процессов у меня не хватило, так что я использовал подходящие
из Интернета. Прошу меня за это не винить, как говориться: «Лучше один
раз увидеть, чем сто раз услышать». Сразу признаюсь: учитель из меня
неважный, мне легче сделать, чем научить это делать. Заранее прошу прощения
за некоторую непоследовательность, материал часто добавлялся по мере вспоминания.
Так что сначала прочитайте все целиком, а затем уже начинайте что-то делать.
Чем ближе вам факты, описываемые в статье, тем очевиднее ошибки в подаче этого
материала (прошу сторого не судить). Материал рассчитан на тех, у кого есть
хотя бы элементарные навыки работы и чуть-чуть воображения. Человек, хоть
раз в жизни сталкивавшийся с каплей воды, и способный мыслить логически, вполне
способен сделать вывод о возможности существования океанов и водопадов, даже
если он не видал ни того, ни другого…
Итак, начнем. Изготовление любой детали, будь то
бампер, накладка на него, антикрыло, капот или корпус сабвуфера вне зависимости
от способа изготовления необходимо начинать с МАКЕТИРОВАНИЯ.
Это самум, ураган, тайфун, землетрясение и падение индекса Доу-Джонса в одном
флаконе. Под этим подразумевается изготовление макета будущего изделия в масштабе
1:1 из подручных материалов. А вот материалы и способ макетирования зависят
от формы желаемого изделия. Допустим, что нужно изготовить бампер. Начинается
все с эскиза и рабочих чертежей. Желательно прорисовать бампер в нескольких
проекциях, включая вид сверху, сбоку, спереди. Имея их можно приступать к
анализу фигур из которых состоит бампер. Чтобы лучше вникнуть в суть процесса
присмотритесь к фотографиям:
Бампера
и пороги на этой машине бросаются в глаза благодаря своей угловатости
и правильности форм. Немного напрягая пространственное воображение можно
заметить, что верхние части обоих бамперов в точности повторяют штатные,
пороги состоят из набора продолговатых брусков, а нижней частью обоих
бамперов является что-то вроде лекала, на самом деле, являющееся проекцией
с верхней части бампера. |
||
Макеты
бамперов и порогов для этих машин могут быть сделаны методом раскройки
подходящего листа пластика или фанеры. Все, что требуется тщательно
обмерить автомобиль и сделать выкройку (развертку). Затем смонтировать
это все на каркасе (скажем из дерева). Со швами, стыками и закруглениями
расправляемся опять же при помощи скульптурных аксессуаров 🙂 Гипса,
шпатлевки, шпателей и шкурки. Особого внимания заслуживают места прилегания
бампера к кузову и фрагменты колесных арок. |
||
Бампера
этих машин изготовлены путем модификации нижней части. Причем на обоих
сделана практически одна и та же работа (на восьмерке деталь получилась
чуть сложнее). |
||
На этих фотах один из простых вариантов: изготовление макета с использованием фрагментов уже готовых бамперов. На первой фотографии штатный бампер распилили и сделали вставку. На второй же макет получился из фрагментов двух штатных бамперов. Этот способ привлекателен тем, что не приходится возиться с местами крепления бамперов, кузовными зазорами, симметрией и т.д. Иногда выносят нижнюю часть бампера вперед- дорожный просвет не уменьшается, а вид получается более агрессивный.(Фото X-LIGHT) |
||
Такая форма бампера может быть получена путем наращивания штатных бамперов (то же что и предыдущий способ изготовления макетов) + добавление несложной геометрической фигуры (крыло-отсекатель со стойками на левой фотографии и рамка-дефлектор на правой) (Фото журнала Тюнинг Автомобилей) |
Как я уже говорил, для начала было бы иметь эскиз. Не важно как он выглядит,
главное, чтоб на нем со всех сторон было видно, что Вы хотите сотворить…
КОТ В САПОГАХ
— А еще меня уверяли, — сказал Кот в сапогах Великану, — но этому-то я никак
не могу поверить, — что вы будто бы умеете превращаться даже в самых маленьких
животных. Ну, например, сделаться мышью. Должен сказать поправде, что считаю
это совершенно невозможным.
— Ах вот как! Невозможным? — переспросил Великан. — А ну-ка, погляди!
И в то же мгновение ока Великан превратился в мышь. Кот погнался за ней, но
мышь, злорадно хихикая, улетела под потолок, потому что оказалась летучей.
МОРАЛЬ: Если вы хотите добиться правильного и быстрого исполнения задуманного,
то формулируйте себе техническое задание возможно более точно.
Изготовление
макетов из пенопласта. В Интернете таких макетов обвесов за
всю жизнь видел только два. Как выяснилось бытует мнение, что с пенопластом
очень трудно работать и он не очень подходит для наших целей. Это не так,
просто нужно знать некоторые тонкости технологии… Резка пенопласта используется
как самостоятельная технология, приложение к изготовлению макетов из монтажной
пены и как изготовление каркасов для обтяжки радиотканью. Итак:
1)Подбор материала.
Лучшим следует признать упаковочный мелкошариковый пенопласт, достаточной
толщины, но такого ни разу не видел, видимо, не судьба… Приемлемых результатов
можно достичь, используя плиты строительного шарикового пенопласта, но есть
одно НО -пенопласт не следует брать толще 50мм, поскольку в более толстых
листах резко возрастает вероятность напороться на несвпенившиеся гранулы полистирола,
обидно (хотя раз на раз не приходится, как раз сегодня изрезал 2 листа пенопласта
2000х1000х100мм и ни разу не натолкнулся на уплотнения). .. Нужное количество
пенопласта на заготовку можно набрать из тонких листов склеивая их клеем для
пенопластовой потолочной плитки. Были эксперименты с импортным синим и розовым
пенопластом — он прочнее и более стоек к эпоксидным смолам и грунтовкам.
2)Чем резать?
Обычный термо-резак, по образу и подобию лучковой пилы или стационарный вариант
типа пилорамы, со струной толщиной 0.8мм. Струну можно раздобыть в утюге,
тостере, фене или электроплитке. Иногда можно приспособить и обычную проволоку.
Нагрев регулируем ЛАТР-ом (лабораторным трансформатором), либо иными подручными
средствами, например я использовал зарядное устройство для аккумулятора, сам
аккумулятор
или батарею аккумуляторов, подсоединенных последовательно. Цель — получить
небольшое отставание струны в центре при минимальном подплавлении. Признак
правильной температуры — тянущиеся за резаком волоски.
P.S. На картинке мои»последнии» модели терморезаков, сделанные из
натянутой спирали калорифера (электрообогревателя) длиной 350 мм, трех реек,
пружины и ручки от лыжной палки. Проволока такой длины хорошо нагревается
от зарядного устройства для 12 вольтовых акуммуляторов (у меня было обычное,
с трансформатором, с переключателем на 4 и 6 ампер). Обязательно ставьте стягивающее
устройство из пружины или резины. Скрученная веревка, как у лучковых пил,
не годится, так как при нагревании спираль существенно провисает. Один резак
для раскроя пенопласта между двумя шаблонами и резки от руки, вторым же можно
резать пенопласт с требуемым углом, пользуясь только одним шаблоном.
P.S.S.
Если есть хороший источник питания, из тонкой латунной (нихромовую, извините
не достал) пластины можно сделать резак для гнутых деталей. Толщина проводов,
подающих на неё питание, должна быть такая, чтоб грелась пластина, а не провода. ..
3)По чему резать?
Есть мнение, что по металлическим шаблонам… Можно и так, но можно спокойно
резать и по фанерным шаблонам, при условии тщательной обработки кромок, и
натирания их графитом (карандаш можно расковырять…) На шаблонах делаем разметку,
с обеих сторон, делений 20-30 будет вполне достаточно. Это пригодится при
резке сильно изогнутых деталей. Да, и еще, шаблоны должны иметь заходную и
выходную части длиной 15-20мм. Можно и без них, но с ними деталь получается
более качественной. Также если руки не дрожат, можно некоторые фрагменты резать
от руки.
4)Как резать?
На ровный стол кладем заготовку с закрепленными шпильками длиной 150-200мм
шаблонами, прижимаем чем-либо, и начинаем резать. Вдвоем, с помощником, он
у одного края, вы у другого, или наоборот, движение следует синхронизировать,
для этого и пригодится разметка на шаблонах. Желательно проходить метки одновременно.
При некотором опыте даже при резке ну очень изогнутых фрагментов волны почти
не возникает…
Как-то мне нахаляву достался набор для фотолюбителя. Резак
для фотобумаги пригодился для резки листовых материалов. Валик для прикатывания
стеклоткани. На электроглянцевателе я держу ванночки со смолой-они нагреваются
как раз до нужной температуры и смола всегда достаточно текучая. Мензурки
и ванночки были использованы для приготовления и хранения смолы (не думайте,
что смешивая отвердитель и смолу на глаз Вы добьетесь хороших результатов.
Избыток отвердителя сделает деталь хрупкой, а недостаток слишком эластичной
и «долгосохнущей»), а вот из фотоувеличителя (или как там его),
вернее из его штатива, я сделал прекрастную «пилораму» для пенопласта.
Описывать конструкцию не буду, думаю сами обо всем догадаетесь. Пока не придумал,
куда приспособлю красный фонарь :-))
Пенопласт можно обрабатывать мелкозернистой шкуркой,
желательно машинкой и на высоких оборотах, но не следует допускать плавления
пенопласта. Клеить его можно, как я уже говорил, поливинилэфиркаким-то клеем
для пенопластовой потолочной плитки или клеем ПВА. А при изготовлении сложных
составных деталей клеить придется часто. Пенопласт трудно шпатлевать привычными
способами, так что уж старайтесь сделать все с первого захода. Грунтовать
его нужно осторожно, были случаи когда грунтовка и нитрошпатлевка его разъедала.
Если нужно , то есть вариант предварительно оклеить пенопласт тонкой бумагой
на разведенном водой клее ПВА или обтянуть лавсаном. Я покрывал как-то мебельным
лаком (вроде НЦ), получил очень гладкую и качественную поверхность.
Из
пенопластовых листов набрана заготовка подходящего размера. |
Затем с
помощью резака были выведены все грани и плоскости, а также прорезаны нужные
отверстия. |
И наконец с помощью наждачной бумаги, шлифовальной машинки и небольшого количества шпатлевки создана требуемая форма. |
Изготовление макетов при помощи монтажной пены.
Весьма распространенный способ, довольно-таки простой, но тоже имеющий свои
хитрости. Пену нужно наносить слоями, а не весь тот обьем который нужен. Это
позволяет экономить недешевую монтажную пену и получать более пригодный к
обработке материал. Большое количество пены застывает в течении 2-3 дней,
а внутри получаются пустоты и очень крепкие уплотнения. Пена хорошо шкурится,
режется ножом, смоченным маслом, и ножовкой. Можно как и в случае с пенопластом
применять шаблоны. Очень хорошее подспорье при работе с пеной это набор лекал(шаблонов)
и электорлобзик с длинными (15-30 см) полотнами. Их можно изготовить из обычных
полотен по металлу, только переточив хвостовик на наждачном круге. Этот нехитрый
инструмент весьма полезен при работе не только с пеной, но и с пенопластом.
Также пена легко обрабатывается болгаркой, ей удобно делать различные закругления.
Недостаток монтажной пены в том, что получается очень пористая поверхность,
непригодная ни к поверхностной оклейке ни к матрицированию. Предварительно
поверхность макета из пены приходится подготавливать при помощи оклейки бумагой
или стеклотканью с последущей тщательной обработкой поверхности. Перед стеклотканью
пену хорошо бы пропитать байдой, которой строители промазывают бетонные стены
перед оклейкой обоями. В качестве руководства по изготовлению макетов и конечных
деталей приведу статью, которые являются практическим руководством, следуйте
за чарующими звуками моего голоса:
Такая машина была изначально.
|
||
Затем бампер был установлен под тем углом, с каким стоял
на машине. Высоту от земли P.S.
Имея большой опыт подгонки стеклопластиковых бамперов берусь утверждать,
что бампер (порог, спойлер) подогнанный на один автомобиль совсем не
обязан подойти на другой точно такой-же. И это не битые машины с проверенной
на стапеле геометрией. Зачастую разница в зазорах превышает 10-15 мм.
Идеально подходящий к одной машине, встающий с зазорами в 5мм по всему
периметру, бампер может даже не встать на крепления на другой машине
(проверенно на BMW 3й, 5й серии, Merceres CLK, Honda Prelude).
|
||
Бампер защищается от брызг. На живой машине с дорогой
краской вообще все заклеивается. Затем контуры будущего бампере заполняются
монтажной пеной. P.S. Чтобы было легче вывести нижнюю плоскость рекомендую
класть на пол
|
||
Через два дня получилось следующее… Контрольное вскрытие
показало: пена засохла.
|
||
Это нечто, именуемое засохшей пеной, разметили и обрезали
согласно чертежам. |
||
Тщательно все зашкуриваем, чтоб потом избавится от лишнего гемороя. Пустоты в пене заново запениваем. |
||
Не стоит пену
сразу оклеивать стеклотканью. Обрезанную пену сначала шкурят (чем ровнее
она будет,
|
||
При оклейке
старайтесь, чтоб ткать легла как можно ровнее. Вот в принципе и готовое изделие, которое можно покрасить
и ездить, а можно и пойти иным путем. Более грамотным и практичным.
Сделать матрицу и уже в ней выклеить бампер. А можно поступить промежуточным
способом: оклеивать заодно с накладкой и бампер, а полученную «скорлупу»
(по сути дела матрицу) использовать как бампер, после того как извлечете
из нее пену и сам бампер :-)) |
||
В этой версии бампера было решено сделать декоративные отверстия… Размечаем. Выпиливаем… |
||
Затягиваем
сеткой… На стеклопластиковые бампера сетку удобно крепить при помощи
шпатлевки со стекловолокном, эпоксидки и стекломата, термопистолета
с клеем. На пластик: герметик (лучше стекольный), качественные пластиковые
хомуты, если позволяют условия, то саморезы. Придать нужную форму сетке
легко при помощи киянки и деревянного бруска. Резать ее лучше не ножницами,
а болгаркой по шаблону, с припуском 1 см для крепления. Сетки (или грили)
если Вы живете в Москве можно купить в компании Алькор. |
||
Залитый жидкой шпатлевкой, готовый к грунтовке бампер или же готовый к матрицированию пуансон (болванка она же макет). Смотря что является Вашей конечной целью. |
||
Тщательно удалить пыль от шпатлевки… Загрунтовать слоя в 2. Пройтись матировочной губкой или 1000й шкуркой с водой. |
||
Вот что
у меня получилось после недели упорных стараний… Я конечно бымог и лучше сделать, но мне помогали 🙂 |
Использование
фрагментов других бамперов. А также адаптирование бамперов.
Especially for Real Bad boys. Один
из самых прикольных способов обратить внимание окружающих на машину. Эта тема
актуальна, если у Вас уже есть бампер или матрица для выклейки, но изначально
предназначенная для другой машины. Я встречал ВАЗ 2110 в полном обвесе для
Mitsubishi Lancer Evolution (не путайте с тольяттинским обвесом, пародией
на EVO) — даже у меня, повидавшего много подобных переделок, челюсть отвисла
до земли. Операция, требующая развитого пространственного воображения. Вопреки
распространенному мнению совсем несложная. В процессе адаптации очень пригодится
монтажная пена, возможно пенопласт, пластилин и может быть гипс (алебастр).
Не стоит зацикливаться именно на фрагментов бамперов. Иногда можно подобрать
очень интересные фигуры и в прочих изделиях. Часто используются для таких
целей пластиковые трубы, оребрения для решеток вентиляции, различные пластиковые
емкости.
Погуляйте по строительным и хозяйственным рынкам — там много подходящих
детелей. Главное, чтобы Ваш макет не напоминал кирпичный сортир, крытый шифером.
Если не жалко, можно купить антикрыло из алюминия (например дешевое PRO.SPORT)
и использовать его в качестве отсекателя. Шансы разбить нижнюю часть бампера
о сугроб резко падуют. Симпатично и прочно.
Первый пример. Установка бампера от SUBARU Impreza WRX (да,
да нравятся они мне)на ИЖ 2126 «Ода». Скульптурные работы почти не понадобились.
Бампер нужно было подрезать посередине, чтоб компенсировать разницу
в ширине и немного подправить его в районе колесных арок. Изнутри места
соединений проклеиваются стекловолокном и устанавливаются крепления
на штатные места ИЖа.
|
||
Вариант два. Более сложный случай. Устанавливаемый
бампер нуууу очень не похож на родной. В данном случае я ставил слепок
(скорлупу) с бампера HONDA Prelude на ВАЗ 2108. Верхнюю часть слепка пришлось полностью спилить,
а вместо нее с помощью монтажной пены был адаптирован слепок с родного
бампера «восьмерки», который Вы видите на левой фотографии.
|
||
Вариант три. Установка целиковых бамперов. Для их установки придется пойти несколько иным способом – модифицировать саму машину, как в случае с мерсом на правой фотке или только крепления и прилегающую к кузову часть бампера-имплантанта, как на левом снимке. Если почитать REDLINE, то там довольно-таки часто описыватся этот способ… |
||
Почти первый случай, только чуть сложнее, так как
устанавливаемый бампер не больше, а меньше требуемого. Установка слепка
накладки с BMW 3 на AUDI V8. Эта инсталляция потребовала
изготовления новых боковин бампера, и удлинения центральной части. |
||
Ну а в заключение зарисовка на тему “Bad Boys Forever!” Из кусков почти нового бампера от Audi A8 и
остатков родного бампера была собрана болванка для бампера. Собирались
куски при помощи саморезов и металлических планок с дырками (конструктор).
Изнутри фрагменты скреплены стеклотканью. Планки снимаем, а бампер шпатлюем.
Лучше шпатлевкой для бамперов, обычная на ABС-пластике
и полиуретане трескается. После подготовки поверхности и обработки разделительным
составом можно снимать матрицу. Ездить с такими бамперами не рекомендуется,
только если нууу очень хочется. Обратите внимание на капот этой машины
и крышку багажника предыдущей.
|
Вот такие бампера можно изготовить примерно
за неделю. |
|
Изготовление
лепных макетов. Лепить можно из глины. Глину для работы используют
пластичную, но не очень мягкую. Сначала следует сделать каркас из фанеры или
листового пластика. Он будет задавать форму, играть роль «маяков».
Затем каркас заполняют, вжимая в него отдельные куски глины. С пластилином
примерно такая же история. Для работы используют скульптурный (он же архитектурный)
или автопластилин. Взять его можно либо в художественных магазинах или же
в автомагазинах (в последних он обычно раза в 3 дороже). Трудность работы
с пластилином и глиной в том, что не имея опыта работы с ними практически
невозможно получить требуемую деталь большого размера. То есть Вы идеально
вылепливаете левую часть бампера, а правая получается не совсем такая. Исправить
эту проблему поможет каркас. Выглядит он примерно следующим образом: с помощью
чертежа делаются сечения детали в нескольких местах и по ним выпиливаются
шаблоны-маяки, а уже пространство между ними заполняется материалом, который
Вы используете для лепки. Между тем лепные макеты очень полезны при изготовлении
корпусов сабвуферов, подиумов, иногда дверных карт. Пластилин и глина укладываются
руками, обрабатываются при помощи шпателей и специальных скребков (они напоминают
одноразовые станки для бритья).
Для лепки можно использовать гипс и алебастр. Перед работой их разводят водой
до состояния близкого к пластилину. Гипс позволяет изготовлять тянутые изделия.
Для их изготовления понадобятся павилА-лекала, которые можно изготовить из
фанеры, ДСП или металла. ПравилА-лекала представляют из себя что-то вроде
фигурных шпателей, которые передвигают вдоль шаблона. Профиль
такого шпателя должен соответствовать форме будущей детали. После окончания
лепки глина, гипс обрабатываются шкуркой, шпатлюются, грунтуются. Не приступайте
к шлифовке слишком рано, дайте материалу просохнуть. А это может занять 3-4
дня. Пластилин для получения более ровной поверхности можно слегка оплавить
промышленным феном.
Таким образом удобно изготавливать расширители арок колес (фендеры, flares) и прочие детали имеющие закругления.Не думаю, что я хороший художник, но надеюсь технология понятна. |
||
При
определенной практике можно изготовить простые «юбки» на бампера (двигая
шаблон вдоль лекала-отсекателя или самого бампера), накладки на пороги
с постоянным сечением (двигая шаблон вдоль рейки или доски) и т. |
||
Пункт
следующий: изготовление различных деталей при использовании каркасов и радиоткани.
Думаю, все сталкивались с тряпками, которыми обтягивают колонки музыкальных
центров? Это тонкая радиоткань. Бывает еще карпет. Им обтягивают подиумы,
корпуса сабвуферов. Этот материал более толстый. Продается во многих магазинах,
связанных с Car Audio. В Москве видел на Горбушке, на Митинском радиорынке
и т.п. Бывает разных производителей, фактур, цветов и плотности. На цвет и
производителя нам в принципе наплевать. Плотность зависит от требуемой детали.
Ткань надо будет пропитать эпоксидной смолой, а тонкая ткань при этом более
склонна к провисанию. Из тонкой ткани делают накладки на стойки ветрового
стекла с подиумами для высокочастотных динамиков, а из толстой корпуса сабов.
Короче чем деталь больше тем плотнее должна быть ткань. Тонкая ткань приятна
тем, что после застывания смолы, благодаря мелкой фактуре не приходится тратить
много времени на подготовку детали к покраске. Тонкую ткань в маленьких деталях
с успехом может заменить нейлоновый (или из чего их там сейчас делают) чулок.
Если Вам повезет, то можно натолкнуться на МЕЧТУ ТЮНЕРА: стеклоткань с эластичными
волокнами. Я как то купил такую на строительном рынке. Ей кажется, стены оклеивают.
Она легко принимает нужную форму, но в отличие от стекломата, при этом имеет
способность натягиваться. Еще можно попробовать использовать стеклоткань (не
мат) в деталях с несложной формой. Когда во мне проснулся экспериментатор
я пробовал «нетканый укрывной материал» для теплиц — с положительным
результатом.
Смысл способа заключается в том, чтобы изготовить каркас будущей детали (бампер,
панель приборов, сабвуфер, подиум) и обтянуть его пропитанной эпоксидной смолой
тканью. Не стоит пропитывать после: ткань, скорее всего, растянется и ее придется
натягивать заново. Каркас делают из дерева, пенопласта, пены и всего, что
под руку попадется. Не стоит пытаться натянуть ткань одним куском, иногда
полезнее сделать каркас из нескольких частей. Смотрите по обстановке. При
натягивании ткани очень пригодился бы аэрозольный клей. Спрашиваейте его там
же, где продается радиоткань.Спортивная ходьба по магазинам Вам поможет. Правда
клей дорогой, зараза. Подиумы, сабы, расширители колесных арок зачастую делают
одним куском, а сложные бампера из верней и нижней части. После того как смола
застыла, радиоткань усиливают полноценным слоем стекломата. Таким образом
очень легко сделать копию плоской детали, например капота. Тонкую пропитанную
ткань натягивают на капот (предварительно тщательно покрытый разделительным
составом или обтянутый тонкой пленкой), стянув края с обратной стороны. После
застывания смолы загнутые края аккуратно подрезают и снимают получившуюся
скорлупу. Затем ее проклеивают стеклотканью или стекломатом. Можно покрыть
топкоутом. И заключающий этап: шпатлевание. Предварительно поверхность шлифуют
шкуркой с зерном 80-150 (капот нужно шлифовать при помощи бруска-рубанка).
Следите за тем, чтобы не очень сильно вгрызаться в поверхнось, не сошлифовать
радиоткань. Так как радиоткань после застывани оказывается довольно-таки ровной,
то порой можно обойтись только нитрошпатлевкой. Наносится она слоями не толще
0,5 мм и в количестве не более 5 слоев. Конструируя саб не забывайте, что
корпус подвержен довольно-таки сильным механическим нагрузкам и толстый слой
шпаклевки на нем долго не продержится. А так получается дешево и сердито.
Вот Вам готовая заготовка для изготовления капота в стиле «Bad Boy». Можете
натягивать его на фары, резать воздухозаборники и отдушины, оставив родной
капот в покое. Тем более новый будет раза в два легче. Вот в принципе и все,
остальное, думаю, ясно из картинок. На верхних показан процесс изготовления
корпуса саба, двернух карт и подиумов, а на нижних трех еще два примера готовых
изделий и автомобиль, но котором колесные арки, пороги и бампер изготовлены
по этой технологии (на них можно кликнуть для увеличения).
И последний способ, о с которым я сталкивался.
Раскройка листовых материалов. Хорошо себя зарекомендовали
листовой пластик (ПВХ) и тонкий (до 5мм) ДВП с гладкой поверхностью. Имеет
место использование фанеры, но ее поверхность приходится предварительно вышлифовать.
Гофрированный и обычный плотный картон также в списке используемых материалов.
Суть
процесса обьяснять не мне. Если Вы сталкивались с изготовлением моделей самолетов,
кораблей и машин из раскроек (например, которые в свое время печатал журнал
«Моделист-конструктор»), то без проблем сможете соорудить макет
бампера.
ПВХ легко режется электролобзиком и гнется при помощи промышленного фена.
ДВП, фанера и картон обладают примерно такими-же свойствами, но только возможности
с искривлению у них несколько меньше. Фанера толщиной 3мм позволяет подручными
средствами (без распаривания и вымачивания) сделать гнутую деталь с минимальным
радиусом закругления около 300 мм. Раскройка крепится на деревянный каркас
или на родной бампер. При придании изделию конечного вида можно использовать
парафин, скотч, пену, пластилин и т.д. Собирать детали можно на мебельных
уголках, использовать «конструктор» для крепления «сайдинга»
и т.п.
Прямые детали, ради прочности, можно изготовить из толстой фанеры. Иногда
на аникрылья и сойлеры идут доски или ДСП. На панели для «уплощения»
днища (защита днища, обтекатели на детали подвески) идет листовой ПВХ или
сотовый поликарбонат.
Технологией работы с деревом я обладаю на уровне чуть выше уроков труда средней
школы так, что для тех, кого эта тема заинтересовала один совет: ищите сайты
по работе с этим материалом. Благо, есть поисковые серверы.
Итак несколько картинок, которые могут служить иллюстрацией этого способа:
Как дополнение к этому способу, хочу упомянуть
еще один интересный подвид макетирования. Вы наверняка видели как строители
заливают опалубку бетоном. Так вот, изготовленные шаблоны из пластика, ДВП
и т.п. можно использовать в качестве опалубки, предварительно обработав разделительным
составом. Эту опалубку можно заполнить шпаклевкой, гипсом, монтажной пеной.
Этот способ позволяет не тратить время на выведение углов и плоскостей, как
например, Вам пришлось бы это делать при классическом изготовлении макета
из монтажной пены.
Примечание. Не старайтесь всегда сделать деталь одним
куском. Иногда гораздо легче сделать составной макет. Например, очень
трудно вышкуривать различные воздухозаборники и прочие отверстия в бамперах,
плоскости, расположенные в труднодоступных местах и т.д. |
Конечно существует еще несколько способов,
которыми я пользовался, но которые тут не описал. Например, использование
3D-фрейзера. Это станок, позволяющий создать макет на компьютере и изготовить
матрицу не прибегая к макетированию. Если у Вас есть знакомые, имеющие доступ
к такой технике, то это существенно упрощает процесс. Меня это наводит на
мысль, что большинство тольяттинских обвесов на ВАЗы, изделия фирм RIGER™
и MS DESIGN™ делаются именно так. Большой ассортимент
и никакого вкуса. Прикольно наблюдать, как какой-нибудь обладатель ригеровского
бампера, с задраным от гордости носов, видит обезбашенный бампер, например
от VEILSIDE™ или Ecosse™. Сопли,
слюни и полное разочарование жизнью Короче,
изготавливая макет Вы видите все недостатки будущего изделия заранее, многое
приходится пересматривать и т.д. А серийное изделие, есть серийное.
Итак макет готов. Пора
приступать к изготовлению конечного изделия. Для начала поверхность
макета еще раз проверяется на наличие дефектов поверхности. Затем макет «вощится»
— покрывается слоем разделительного состава. Он поможет отделить матрицу от
макета и устранит мелкие неровности. А делается это так: при помощи шерстяной
ткани или специальных полировальных салфеток наносится тонкий слой разделительного
состава. После того как он просохнет располировываем его. Операция КРАЙНЕ
утомительная. Все нужно делать вручную, это позволит тщательно контролировать
процесс. Одновременно обрабатывать можно кусок не более 10х10 см, при такой
площади полироль лучше разогревается и проникает в поры поверхности. Операцию
повторяем 2-3 раза. Забегая вперед скажу, что при обработке раздилительным
составом матрицы операцию повторить придется 3-5 раз!!! Всегда не хватает
времени, чтобы выполнить работу как надо, но на то, чтобы ее переделать, время
находится.
Не стоит этим пренебрегать, так как легкость с которой Вы извлечете изделие
все окупит. В противном случае Вам грозит долгое ковыряние отверткой или повреждение
мантрицы с макетом. Лучше потратить день на полировку, чем неделю на шпатлевание
и вышкуривание детали.
После завершения полировки макета перед нами стоит выбор:
изготовить МАТРИЦУ или сделать изделие не прибегая к ней. Выклеивание композитных
«корок» можно осуществлять как внутри, на снятой с болванки (макета)
вогнутой форме (матрице), так и снаружи на болванке (макете). Второй способ
я уже практически описал в разделе МАКЕТИРОВАНИЕ,
в статье про изготовление макета при помощи монтажной пены. Макет оклеивается
стекловолокном, полученная скорлупа снимается и подготавливается к покраске.
Процесс подготовки очень долгий, так как приходится бороться с фактурой стекловолокна
🙂 Поверхность детали имеет фактуру ткани и требует шпаклевания и вышкуривания.
Итак напомню процесс:
1. Изготовление, подготовка макета, покрытие его разделительным слоем. |
|
2. |
|
3. Обрезаем все лишнее, вышкуриваем поверхность, шпатлюем (сначала шпатлевка со стекловолокном, потом обычная, затем если нужно то нитро) и опять все тщательно вышкуриваем. |
|
4. Покрываем деталь жидкой шпатлевкой, вышкуриваем, грунтуем, шлифуем, красим, лакируем и наконец полируем. Все. |
Зачастую, более сложный способ матрицирования бывает более
быстрым и позволяет получить более качественное изделие (например, если Ваш
макет уже до такой степени ровный и гладкий, что душа радуется))). Для выклеивания
деталей по второму способу (матричному) нужно прежде всего изготовить саму
«негативную» форму. Обычно она представляет собою толстостенную
«скорлупу», выклеенную из стеклоткани. Все работы с эпоксидными
(да и полиэфирными) смолами нужно проводить в резиновых перчатках в помещении
с хорошей вентиляцией! Итак матрицирование:
Покрываем макет слоем гелькоута, пользуясь кистью или распылителем
(можно использовать те пистолеты, что предназначены для антикора). После того,
как гелькоут в достаточной степени отвердился, наносится, как можно более
равномерно, обильный слой смолы. Стеклоткань нарезается на выкройки, которыми
можно было бы оклеить болванку без образования складок. Затем крепко прижимается
и уплотняется кистью или валиком первый слой. Это дает смоле возможность пропитать
стекломат и растворить скрепляющее волокна связующее, после чего армирующий
материал легко принимает форму макета. Как только первый слой стекломата полностью
пропитается, то, при необходимости, перед нанесением последующих слоев армирующего
материала, добавляется дополнительное количество смолы.
Армирующий материал пропитывается с помощью
кисти или валиков из мохера или полиэфирного волокна. При использовании кисти
необходимо производить точечные движения ею, поскольку любые перемещения кисти
в боковом направлении приводят к смещению волокон и нарушению произвольного
характера их расположения. Использование валиков эффективно при работе с крупногабаритными
матрицами. Существуют валики с длинной и короткой рукояткой. Валики с длинной
рукояткой способны принимать большее количество смолы и требуют более точного
контроля за соотношением смолы и стекломатериала. Процесс уплотнения ламината
более эффективен, если производится с помощью валиков. С этой целью было разработано
несколько их видов. Существуют металлические валики с продольным и поперечным
ребром, угловые валики. Из них наиболее эффективным для удаления попавших
в смолу пузырьков воздуха оказалось использование валиков с поперечным ребром.
Если деталь крупная, то избежать нудного выдавливания
пузырьков воздуха поможет целофановый пакет. Поместив туда изделие и
откачав воздух мощным пылесосом Вы получите более качественную поверхность
и более прочную деталь. |
Для того, чтобы матрица лучше держала форму, к ней можно приформовать ребра из фанеры, дерева и т.п. После полного высыхания смолы извлекаем макет.
Примечание: Если деталь сложная, делаем составную
или разъемную матрицу. При ее изготовлении делаются специальные перегородки
вокруг макета, разделяющие его не сегменты. Выклеив первую часть матрицы,
ждем ее высыхания, и обработав края сегмента разделительным составом,
приступаем к выклейке второй части. |
1. Чем лучше будет качество поверхности макета, тем меньше
потребуется отделочных работ для каждого изделия в дальнейшем! Стараютесь
довести поверхность до зеркального блеска, чтобы готовые, отформованные
в этой матрице детали нуждались только в окраске. |
Итак после завершения
матрицирования приступаем к выклейке готового изделия. Предварительно
устраняем все дефекты матрицы и покрываем ее разделительным составом. О важности
тщательной полировки упоминалось не раз. Покрываем матрицу слоем гелькоута.
Гелькоутом на выклеиваемом изделии увлекаться сильно не стоит, он может со
временем растрескаться и Вам придется перекрашивать изделие. Дальше как при
изготовлении матрицы: после того, как гелькоут в достаточной степени отвердился,
наносится, как можно более равномерно, обильный слой смолы. Над смолой не
дышать! Иначе после этого вы вернетесь домой в состоянии летающих аквалангистов…
Затем крепко прижимается и уплотняется кистью или валиком первый слой стекломатериала
— стекловуали. Как только первый слой стекломата полностью пропитается, то,
при необходимости, перед нанесением последующих слоев армирующего материала,
добавляется дополнительное количество смолы. Важно, чтобы первый слой не содержал
пузырьков с воздухом, поскольку любое попадание воздуха непосредственно между
гелькоутом и последующим слоем ламината может привести к вспучиванию поверхности,
особенно, если в течение периода своей эксплуатации формуемое изделие будет
подвергаться воздействию тепла или воды. Другими словами, если делаете деталь
интерьера, можно чуть-чуть схалявничать, но детали же обвеса вам этого не
простят.
Последующие слои смолы и армирующего материала наносятся
до получения требуемой толщины, при этом необходимо обеспечить тщательную
пропитку и надлежащее уплотнение каждого слоя. Во избежание скопления избыточного
количества выделяемого при ламинировании тепла рекомендуется единовременно
наносить не более четырех слоев смолы и армирующего материала. Обвесы не требуют
такого количества материала, но при изготовлении сабов и подиумов под динамики
придется действовать постепенно. Высокие экзотермические температуры могут
привести к растрескиванию гелькоута, преждевременному высвобождению изделия
из матрицы, деформации или обгоранию детали. При изготовлении ламинатов большой
толщины после нанесения четырех слоев, перед нанесением последующих, ламинат
необходимо выдержать для выделения тепла, после чего охладить. Перегрев может
разрушить разделительный слой и безнадежно погубить матрицу. Продолжительных
временных задержек между нанесением слоев, однако, следует избегать, за исключением
случаев использования смол с длительным «периодом созревания». «Период созревания»
— термин, используемый для описания периода времени между загустеванием и
отверждением смолы, в течение которого она находится в размягченном, высокоэластичном
состоянии.
В таком состоянии ламинат может быть легко подогнан по форме матрицы,
а обрезная кромка заделана в матрицу для ускорения данного процесса.
Упрочнение формуемого изделия достигается
введением в него ребер жесткости. Момент введения зависит от формы, толщины
и конечного назначения изделия. В качестве общего руководства рекомендуется
размещать их непосредственно перед нанесением последнего слоя армирующего
материала. Если использовать пенопласт, оклеенный стеклотканью, то это позволит
значительно усилить деталь незначительно увеличив массу. Так делают капоты
и крышки багажников. Я так на даче дверные косяки и оконные рамы вклеивал
по привычке. Прочность неимоверная, герметичность 100%. Строителей, видевших
это, пришлось отпаивать литром самогона. Для порогов, бамперов и спойлеров
вполне достаточно слоя порошкового стекломата около 5мм. Элементы, образующие
ребра жесткости, покрываются армирующим матом и тщательно пропитываются смолой.
После чего, для придания обратной поверхности однородности, на всю поверхность
формуемого изделия может наноситься заключительный слой армирующего материала.
Иногда в качестве фиксирующих или опорных точек и т.д. используются металлические
вставки, вводимые на этапе выклейки. Советую делать крепления бамперов только
из металла, стеклопластик, просто привернутый саморезами, часто ломается.
Если предполагается подвергать изделие воздействию значительных нагрузок,
то толщина формуемого изделия, начиная с места вставки, должна постепенно
уменьшаться в целях распределения нагрузки. Металлические вставки необходимо
размещать как можно ближе к середине ламината, а поверхность контакта ламината
со вставкой должна быть по возможности максимально большой. Не увлекайтесь
толщиной бамперов. Я имел возможность видеть машину с поврежденными крыльями
и рамкой радиатора от незначительного удара, только потому, что бампер был
10мм толщины и армирован латунной сеткой.
Сам бампер только поцарапался. Стеклопластик
очень крепкий материал, так что выбирайте: новый бампер или жестянка.
Если для покрытия поверхности матрицы необходимо соединить
между собой части армирующего материала, то может использоваться стыковое
соединение или соединение внахлест. Стыковые соединения необходимо производить
с особой осторожностью, таким образом, чтобы не оставалось расстояния между
двумя краями материала. Соединения внахлест не должны перекрываться более
чем на 25 мм, если иное не требуется в целях повышения жесткости. Сделать
места соединения рубленого стекломата менее заметными можно путем распределения
излишнего количества мата, находящегося по обе стороны соединения, с помощью
небольших круговых движений кистью вдоль линии стыка.
Обратная поверхность формуемого изделия может быть довольно шероховатой, особенно,
если в качестве армирующего материала применяется рубленый стекломат.
После того, как смола окончательно затвердеет, очень аккуратно
извлекаем готовое изделие. В матрице же можно выклеивать еще 5-8 изделий.
Если ее переодически ремонтировать и тщательно покрывать сазделительным составом,
то наааамного больше.
Скажу честно, матрицирование и выклейка изделий очень доходная
сторона «теневого» бизнеса 🙂 Через мои руки проходило очень большое
количество всевозможных деталей обвесов, оптики и т.д. Что-то привозили на
ремонт, что-то на подгонку, покраску и установку. Тем более несколько моих
друзей сами барыжили тюнинговыми бамперами и охотно сотрудничали. Приведу
примерные подсчеты. Бампер «Миллер-Пилот» от Lit-company™
для ВАЗ 2108-99. Официальная цена (2005 год): 250 зеленых бумажек
с изображением президента. Затраты на матрицирование и изготовление менее
100 бумажек. Продав одно изделие за пол-цены окупается все производство. А
наштамповать их можно несколько в день. Бампер фирмы Riger™
или Seidl™ для BMW. Цена в Москве около 400 бумажек.
Затраты на матрицирование и изготовление те же, что и для восьмерки. Выходит
цена изделия зависит только от модели автомобиля, а не от затрат на производство.
Теперь интереснее: комплект тюненой «листвы» (молдинги) для MB W140.
Цена в Москве около 800 долларов. Цена изготовления в «подпольных условиях»
около 70 долларов. Я имел честь убедится, что половина HAMANN`овских, BRABUS`овских,
HARTGE`овских и тому подобных обвесов и модульной оптики делается в подмосковье.
На своем опыте знаю, что копию, по цене процентов на 30 дешевле оригинала,
оторвут с руками… Продать, «копеечную» в копировании, накладку
на бампер BMW X5 можно за 1000 у.е. и это не вызовет подозрений обывателя.
Делайте выводы.
Заключительный
момент -покраска. Я обладаю этим умением на начальном уровне
и красил всегда только для себя. Процесс, требующий расходов на материалы
и не такой простой, как кажется на первый взгляд. В действительности все не
так, как на самом деле 🙂 Кого интересует более подробная информация, может
поискать подобные материалы в Интернете. Только вот не нарвитесь на материалы
3-5 летней давности, сейчас многие вещи, благодаря новым материалам, делаются
гораздо проще.
ГРУНТОВАНИЕ. Самые трудоемкие операции
— подготовительные (очистка, выравнивание, шпатлевание). Именно
они отнимают до 90 % времени. Грунтование и нанесение эмали — дело быстрое.
Если, конечно, не напортачить — тогда придется сошкуривать неудачно наложенную
краску и начинать процесс сначала.
Первым слоем на зашпатлеванную и вылежавшуюся не менее суток деталь нанесем
специальным пистолетом (или из балончика, сейчас развелось столько фирм, что
в баллончики Вам нальют чего вы только не пожелаете) грунт. Его можно спокойно
наносить в несколько слоев (с выдержкой 10-15 мин), «накрывая» по ходу дела
все оставшиеся поры и царапины. Недорогая и достаточно хорошая грунтовка есть
у фирм NOVOL и DYNO COAT. Большинство грунтовок содержат антикорозионные добавки,
которые иногда не очень хорошо влияют на эпоксидную смолу. Так что лучше использовать
специальные грунтовки для пластика.
ШЛИФОВАНИЕ. После грунтования следует выждать
4-16 часов (точнее см. инструкцию к материалу), а затем отшлифовать всю поверхность,
чтобы выровнять «выжившие» после предварительной обработки микрорисочки.
Сначала воспользуйтесь шкуркой с индексом зернистости «Р 800» по «мокрому»
с бруском, потом — «Р 1000», причем все нужно делать вручную. Качество поверхности
оцениваем «проявкой», используя, или обычный баллончик с нитрокраской или
специальный порошок — «сухую проявку». Если используете нитрокраску,
не забудте потом ее смыть или сошкурить. Напоследок пройдемся по всем поверхностям
так называемым скотчем Брайтона — его зернистость порядка «Р 1500» Этот скотч
напоминает по фактуре мочалку для мытья посуды. Он не убирает дефекты, а просто
наносит определенную риску для лучшей адгезии с краской. И, наконец, протрем
обрабатываемую поверхность специаль ной салфеткой, смоченной обезжиривателем
(как это уже делали в первой части). Можно еще обдуть деталь сжатым воздухом
и, таким образом, начисто избавимся от пыли. Запомните: пыль Ваш враг номер
один.
ПОКРАСКА. Наконец, мы подошли непосредственно
к нанесению краски — приступим. Первым делом нужно выбрать цвет краски и тип
эмали. Сейчас применяют три основных вида эмалей: нитро, алкидные и акриловые.
Считается, что самые прочные и удобные -акриловые. В свою очередь, они могут
быть простыми и «эффектными»: «металлики», «хамелеоны» и т. д. Ноги в руки
и бегом на фирму, занимающуюся цветоподбором. Там Вам подберут и краску, и
лак, и грунт, и все остальное. Предположим, на сей раз это будет модная и
достаточно сложная трехслойная перламутровая краска. Состоит она из так называемой
«базы» (первого слоя краски, создающей фон), цветообразующей эмали и лака,
придающего покрытию зеркальный блеск.
Расход материала примерно на 50 кв. дм 150 г «базы». Этого
вполне должно хватить на средний бампер, хотя для каждого вида краски, ее
цвета или даже оттенка расход исходного материала все-таки разный. Очень многое
зависит от «укрывистости» краски, т. е. способности ее свежего слоя становиться
непрозрачным. Разные компоненты имеют разную «укрывистость»: иногда поверхность
можно укрыть в полтора слоя, иногда — в семь или даже в восемь. Разведем краску
специальным растворителем. Кстати, каждая из трех составляющих требует своего
особого растворителя. Ну, а затем процедим краску через фильтр с сеточкой
190 микрон. Для создания «базы» достаточно нанести три тонких слоя — они высыхают
очень быстро (15-20 минут). Определить, что краска высохла, просто: она перестает
блестеть, становится матовой. Кстати, без лака краска вообще блестеть не обязана.
После высыхания «базы» кладем три слоя цветообразующей эмали. Не беда, если
после первого слоя остается некоторая «яблочность» (так называют эффект, когда
соседние участки различаются по цветонасыщенности). Мы избавимся от этого
неприятного эффекта с помощью последующих слоев. Но не очень-то полагайтесь
на них — важно наносить слои аккуратно, чтобы не образовались потеки краски.
Если «база» или сама краска все же потекли, придется, после того как краска
просохнет, всю поверхность вновь обработать шкуркой. Еще хуже, если потечет
лак. В этом случае его сначала просушивают до полного затвердевания (на воздухе
это длится сутки, в камере при 60 градусах — 40-60 мин), потом зашлифовывают
дефектное место и, наконец, тщательно полируют. Если при этом краска протрется
до «базы», придется начинать процесс покраски «с нуля». Обратите внимание
на подставку на фотке, на ней очень удобно подготавливать и красить деталь.
ЛАКИРОВАНИЕ. Лак (100 грамм) разведем отвердителем.
Пропорция легко определяется при помощи специального стаканчика с мерной линейкой.
Лак наносим в полтора слоя из того же пистолета, что и краску. Первым слоем
чуть «припылим» (в полслоя) поверхность и выждем одну-две минуты. Потом покроем
основным -полноценным слоем до растекания. Если же положить сразу много лака,
он запросто может потечь.
При лакировании качество глянца зависит от скорости движения пистолета и подачи
лака. Если вести пистолет достаточно быстро, слой ложится как бы наполовину
толщины. Если тут же повторить задувку, лак опять-таки может потечь… Спросите,
что значит «быстро», достаточно «быстро», полноценный и неполноценный слой?. .
Навык пользования малярным пистолетом приобретается с опытом. Наберетесь его
— и узнаете все ответы на ваши вопросы. Но есть и незыблемые, и понятные всем
правила: сначала следует красить края, торцы, и уж затем другие участки поверхности.
«Решетку» делать не стоит, движениями надо как бы повторять контуры
детали, при этом перекрывая на полфакела предыдущую полосу краски. Нельзя
покрывать один и тот же участок дважды. В труднообозреваемых местах, или в
случае, когда нельзя отстраниться от покрашенной детали, чтобы оценить качество
глянца, можно сделать так: подставить к нужному участку руку и по ее отражению
проверить, не образовалась ли на поверхности «шагрень» — структура поверхности,
напоминающая апельсиновую кожуру. Начинающим малярам можно посоветовать первый
слой нарочито покрывать «шагренью», подождать 10-15 минут и вновь покрыть
деталь лаком — до глянца. Поверхностям нужно дать высохнуть (не менее 40 минут),
и только потом можно приступить к их полировке.
Полезные советы.
Первое. Краску с отвердителем смешивать точно в указанной пропорции и во всех
прочих вопросах следовать рекомендациям производителя .
Второе. Перемешивание краски с отвердителем никогда не может быть излишним
. После тщательного перемешивания , как рекомендовано изготовителем , дайте
смеси постоять , чтобы запустилась реакция и затем еще раз пермешайте в течение
нескольких минут . Даже если после чтения инструкции на банке у вас есть сомнения
в необходимости этого — напрасно .
Третье. После запуска реакции краску перед применением надо процедить . Вы
будете удивлены , когда обнаружите , что иногда может остаться на сетке .
Четвертое. Максимально «ускоряйте» краску до предела , рекомендованного
производителем (если красите из пистолета и сами готовите краску). Чем скорее
она встанет , тем лучше для окончательного результата и меньше шансов , что
к ней что-то прилипнет. При покраске бамперов крайне желательно добавлять
пластификатор, рекомендуемый изготовителем краски.
Пятое. Избегайте любых контактов с полиуретановой краской . Не вдыхать , не
прикасаться . Я уже говорил об этом ранее и повторю еще раз. Очень важно иметь
защиту для органов зрения в виде каких-либо очков , чтобы отраженные частицы
краски не попали в глаза. Неплохо иметь для этого маску , закрывающую все
лицо . Полиуретановые и акриловые краски содержат изоцианат , именно он придает
им красоту и долговечность и одновременно превращает в убийц.
Шестое. Перед грунтовкой или покрытием детали жидкой шпатлевкой не пользоваться
шкуркой со слишком мелким зерном . Большинству двухкомпонентных грунтов необходима
для адгезии определенная шершавость поверхности . Мой опыт показывает , что
для большинства типов грунтов максимальное зерно — 320 , хотя во многих случаях
вполне хватает и 220-го .
Седьмое. Перед покраской всегда протирать поверхность тканью , чтобы удалить
малейшие следы шлифовальной пыли.
Восьмое. Смолы плохо переносят солнецный свет и воду, так что очень рекомендую
не только окрасить деталь снаружи, но также покрыть ее (например антигравием)
изнутри.
Ну вот, теперь действительно вроде все, буду очень рад если Вам эта статья
хоть в чем-то помогла.
X-LIGHT (Малышев Ярослав) © 1995-2005
С ссылкой на источник разрешено любое использование данной информации.
X -tra ThankZ за помощь:
Оборотень
Messadot
Maddog
Falcon
Женя Гладков из GLADKOV-SERVICE
Андрюха «Толстый» из True Perfomance Solutions
Илья «Watto» Фещенко из AB-Tuning
Андрюха «Jump» Кочев
Гена «Paradox»
Roma GTR (Роман Семенов)
Rat
Ванес «Sin»
Андрюха «Кондрат»
Серега «Слесарь» Добренков из «Кортекса»
Роман из журнала «Меню удовольствий»
Саня «Хохол»
Толян (UA)
Толян (PZ)
Saifullin
LIT-company
ТРИ-АБС tuning
MJ-tuning
маляры из ДВ-Моторс
DSM-tuning
G&S electrics
«Балтика»
«Очаково»
«Ярпиво»
«Nescafe»
Philip Morris Products S. A.
Радиостанции «NEXT FM», «KJAH», «MSX FM», «Динамит
FM», «KISS FM»
Виды пластиков применяемых в автомобилестроении
По статистическим исследованиям автомобилестроение занимает ведущее место после разработок военно-промышленного комплекса и производства оргтехники, в сфере которого внедряются самые современные инновационные разработки. Для многих стран эта область промышленности является важнейшей бюджетной отраслью. Естественно, в силу экономических требований в автомобилестроении широко предпринимаются попытки совмещения высокой технологичности используемых материалов и оборудования со снижением стоимости их производства.
Одним из таких продуктов, эффективно позволившим совместить в себе простоту изготовления, высокие эксплуатационные характеристики и низкую себестоимость является пластмасса. Когда немецкий химик Байер (ныне это название известного концерна) в 1872 г. смешал формальдегид и раствор фенола, то получил смолообразную, вязкую массу. При нагревании она превращалась в твердое, нерастворимое вещество, которое повторно уже не плавилось. В то время ученый еще не мог предвидеть, какое огромное значение приобретет впоследствии полученный им продукт – далекий прародитель современных пластиков.
В соответствии с отечественным государственным стандартом «пластмассами называются материалы, основной составной частью которых являются такие высокомолекулярные органические соединения, которые образуются в результате синтеза или же превращений природных продуктов. При переработке в определенных условиях они, как правило, проявляют пластичность и способность к формованию или деформации». Главное преимущество пластмасс по сравнению с металлами заключается в том, что их свойства легче регулировать и поэтому пластмассы быстрее и лучше можно приспособить к требованиям практики. К преимуществам пластмасс относятся также низкая плотность, отсутствие у большинства из них запаха и вкуса, высокая коррозионная стойкость по отношению к атмосферным воздействиям, к кислотам и щелочам, бензину и агрессивным различным продуктам химии, пластики обладают отличными электро- и теплоизоляционными свойствами. Кроме того, изделиям из пластмассы легко можно придать любую форму самыми разнообразными способами. Их можно отливать и прессовать, прокатывать и протягивать, выдувать и вспенивать, прясть, сваривать и склеивать. Пластмассы хорошо поддаются механической обработке — их можно строгать, фрезеровать, обтачивать и сверлить. Наконец, возвращаясь к теме статьи, большинство пластмасс превосходно поддается окрашиванию. Неудивительно, что столько преимуществ пластика находят широкое применение, в автомобилестроении. Многие владельцы автомобилей, с тоской взирающие на многочисленные участки коррозии на кузове своих «стареющих» машин, согласятся с мнением: голубая мечта автолюбителя – полностью пластмассовый автомобиль! В продолжение шутки, можно вспомнить, что такие попытки предпринимались. Например, кузов малолитражки «Трабант», выпускавшейся в ГДР более 30 лет назад на заводе в Цвиккау, целиком изготавливался из слоистого пластика. Это материал наряду с крезолоформальдегидной смолой содержал отходы хлопчатобумажной пряжи, поступавшие на завод с текстильных фабрик.
Для получения этого пластика 65 слоев очень тонкой ткани, чередующихся со слоями размолотой смолы, спрессовывались в очень прочный материал толщиной 4 мм при давлении 40 атм. и температуре 160 °С в течение 10 мин. До сих пор трехцилиндровые детища того серийного производства, ставшие притчей во языцех, лежат на многих свалках страны. Лежат, но не ржавеют! Кузовные детали современных автомобилей, изготовленные из самых технологичных типов пластика, уже не вызывают подобной улыбки. Стойкость этих материалов к ударным нагрузкам, способность их реформированных участков к самовосстановлению, высочайшая антикоррозионная стойкость и малый удельный вес,– преимущества, уже не достигаемые металлом.
Можем не сомневаться, еще пять-десять лет и процент замещения металлических элементов пластмассовыми как и, соответственно, количество ремонтов на пластике и металле практически сравняются. В автомобилестроении полимерные материалы используются практически во всем ассортименте. Применяемые разновидности пластиков настолько разнообразны, что не будь каких-то универсальных материалов, способных создавать качественное декоративное покрытие со многими из их типов, наверное, малярам пришлось бы получать специальное образование по химии. Как мы заранее в начале статьи предупредили читателей, все окажется значительно проще. Материал, из которого сделана пластмассовая деталь, будь то бампер вашей машины или крышка мобильного телефона, можно определить по маркировке на внутренней поверхности. Тип пластика, как правило, заключен в характерные скобки и может выглядеть следующим образом: >PUR<, <ABS>, >PP/EPDM<.
Подобная аббревиатура может иметь огромное число вариантов.
Полипропилен >РР<
Это самый распространенный в автомобилестроения тип пластика. Подавляющее большинство бамперов и кузовных элементов производятся именно из полипропилена. Сама молекула полимера, конечно, не только полипропилена, состоит из практически бесчисленного числа таких соединенных в единое целое кусочков. Она может включать в себя от нескольких тысяч до нескольких миллионов звеньев. С определенной долей правды и, конечно, неопределенной – чувства юмора, можно сказать, что бампер – это одна молекула! Полипропилен обладает, пожалуй, совокупностью всех преимуществ пластмассы: низкой плотностью, высокой механической прочностью, долговечной химической стабильностью, повышенной теплостойкостью, хорошей способностью к восстановлению, возможностью к регенерации. Кроме всего этого, полипропилен является экологически чистым материалом. За столь ценные свойства он получил титул «короля пластмасс». Производство полипропиленовых деталей требует сложного технологического оборудования, но экономически это вполне оправдано огромными объемами производства. Этот материал наиболее часто используется при изготовлении бамперов, деталей салона, спойлеров, панелей приборов, различных емкостей для технологических жидкостей. В быту даже чемоданы изготавливаются из полипропилена.
При литье большинства из перечисленных деталей чаще всего применяется не «чистый» полипропилен, а его различные модификации, то есть различные его композиции, смеси с каучуком, резиной. Это, так называемые термопластичные эластомеры. Самый распространенный и всем известный продукт этих модификаций —>PP/EPDM< (Polypropylene / Ethylen PropyleneDiene Monomer).Окрашиванию поддается только модифицированный полипропилен! Любые модификации полипропилена, какой бы длинной не была аббревиатура его маркировки, первыми двумя буквами обозначен все равно, как >PP…<. Например, передние крылья Renault Clio имеют маркировку >PPE+PA66<.
Немодифицированный полипропилен >РР<,применяемый в автостроении, из которого, например, изготавливаются бачки омывателей, расширительные емкости, не рекомендуется окрашивать. Адгезионные свойства покрытия будут очень слабыми. Можно добавить, что одноразовая посуда, различные стаканчики для прохладительных напитков, пластиковые емкости для приготовления краски многих производителей, пользующихся большой популярностью на пунктах подбора автоэмалей, изготовлены именно из, условно скажем, «чистого» полипропилена >РР<.
Полиуретан >PUR<
Многие мастера связывают с этим типом пластика известную марку Мерседес. Бамперы, боковые накладки дверц, порогов (в обиходе листва) практически на всех моделях изготавливались до недавнего времени из полиуретана. До широкого внедрения в производство полипропилена полиуретан был самым популярным материалом, при производстве эластичных деталей автомобиля: рулевых колес, грязезащитных чехлов, покрытия для педалей, мягких дверных ручек. Выпуск деталей из этого типа пластмассы требует менее сложного оборудования. В настоящее время многие небольшие частные компании, как за рубежом, так и в странах бывшего Союза предпочитают работать именно с этим типом пластика для изготовления бесчисленного разнообразия деталей тюнинга автомобилей, многих других изделий для производства и быта.
Стеклопластики
Стеклопластики являются одним из важнейших представителей группы полимерных материалов, объединяемых названием «армированные пластики». Высокие физико-механические показатели, а также стойкость к воздействию различных агрессивных сред определили широкое использование этих материалов во многих областях промышленности. Всем известный продукт, используемый в производстве кузовов американских минивэнов. Стеклопластики изготавливаются на базе эпоксидных или полиэфирных смол со стеклотканью в качестве наполнителя. При изготовлении стеклопластиковых изделий с широким спектром требований возможно применение технологии изготовления изделий типа «сэндвич», когда детали состоят из нескольких слоев различных материалов, каждый из которых несет заданные параметры (прочности, химстойкости, абразивоустойчивости). Неудивительно, что широчайшая область применения, популярность пластиковых материалов подразумевает собой реальную экономическую выгоду. Этим аргументом легко объясняется масштабное изготовление кузовных деталей не только у оригинального производителя, но и на многих других заводах по всему миру, не имеющего ничего общего с автопредприятиями. Понятно, качество такого пластика, как и сама технология производства, мягко говоря, несколько различны. Техпроцесс изготовления пластиковых деталей на таких предприятиях максимально упрощен. Но крайне низкая цена готовой продукции с лихвой компенсирует эти недостатки. Редко какой владелец подержанного автомобиля будет иметь претензии к недосконально точным геометрическим формам бампера, увеличенным зазорам по сопряжению с другими кузовными элементами, если такой бампер в три раза дешевле оригинального. Но с другой стороны, его ведь надо еще и покрасить. Отслаивающаяся покровная эмаль вряд ли удовлетворит клиента. Не большая проблема, если для установки противотуманных фонарей придется подпиливать участки бампера. Но краска на нем держаться должна в любом случае. При литье или прессовании пластиковых деталей прессформы увлажняются специальными веществами, которые, естественно, оставаясь на пластмассовой поверхности бампера, при окраске не способствуют адгезии лакокрасочного покрытия. Подготовка к покраске таких «нефирменных» деталей требует предварительной подготовки.
Мойка пластиковых деталей
В специализированных производствах для очистки поверхности пластика от различных технологических жидкостей применяются специальные ванны с раствором очистителей. Представить такую, как минимум, двухметровую ванную литров на пятьсот на СТО не очень реально. Да и нет в том необходимости. Первым этапом удаления таких загрязнений, а иначе в данном случае эти важные некогда технологические продукты уже не назовешь, вполне подойдет большая и жесткая малярная кисть или щетка и ведро воды с любым активным моющим раствором: жидким мылом, автошампунью.
Выпаривание
Поверхностные загрязнения мы удалили. Но незначительная часть их может остаться во внутреннем верхнем слое. Хороший прогрев при высокой температуре поможет части загрязнениям испариться или выйти на поверхность. Их будет проще позже удалить обезжириванием. Иными словами, не всегда обязательным, но лишним не будет для качественного ремонта прогреть бампер в окрасочной камере. Понятно, совсем не обязательно включать этот процесс в отдельный технологический цикл. Вполне можно загрузить в камеру несколько пластиковых деталей и прогреть их одновременно с сушкой какого-либо окрашенного автомобиля. Рационально используйте энергоноситель! (Солярка как-то грубовато звучит.) Напомним, данные рекомендации разумны в применении для новых деталей сомнительных производителей. Сертифицированный бампер Volvo в красивой упаковке, купленный на сервисном центре в Стокгольме за полторы тысячи евро, в этом явно не нуждается!
Обезжиривание
Перед первой шлифовальной операцией на пластмассовых деталях, будь то подготовка к грунтованию или шпатлевание – необходимо применять обязательное обезжиривание. Это касается и упомянутого выше бампера.
Дальнейшие операции проводятся в соответствии со стандартным процессом подготовки и окраски. Одно лишь уточнение, на первый взгляд излишне педантичное, но обезжиривание нового пластикового элемента рекомендуется проводить как с внешней, так и с внутренней стороны.
Ремонт поврежденного пластика
Наверное, самый распространенный метод склеивания треснувших участков пластиковых деталей в мастерских, связана с работой паяльником. Понятно, если речь ведется о нескольких сантиметрах поврежденного участка это вполне оправдано. Только далеко не каждый тип пластика подвергается такому примитивному варианту ремонта. Полипропилен, например, достаточно лоялен к такой процедуре, а вот полиуретан будет легко плавиться, но спаяться с другим участком «откажется». Самой разумной рекомендацией при ремонте треснувших участков будет использование при ремонте неармированных пластиков наборов специальных полимерных клеев, или ремонтных материалов на основе полиэфирных или эпоксидных смол со стеклотканью при работе со стекловолокнистыми пластиками.
Шлифование
Рекомендации по выбору зернистости абразивных материалов при обработке пластмассовых деталей незначительно отличаются от принятых стандартов. Адгезионные свойства покрытия напрямую зависят от шероховатости и структуры зашлифованной поверхности, и лишь косвенно от градации примененного на ней абразивного материала. Это не оговорка. Параметр шероховатости поверхности обработанной одним и тем же абразивным материалом одной и той же градации на металле и пластике будет значительно отличаться. Шлифовальные риски на мягкой пластмассе будут более выраженными и глубокими, с большим количеством заусениц. Особенно наглядно это можно наблюдать, обрабатывая пластик крупными абразивами Р80, Р100. Совет по правильному выбору зернистости совсем прост. При работе с пластмассовыми деталями используйте абразивные материалы на одну ступень градацией выше, т.е. с более мелким абразивным зерном.
Шпатлевание
Сплошное выведение шпатлевкой равномерной плоскости по всей поверхности пластикового элемента, будь то бампер или капот – занятие рискованное. При деформации, пластик ведет себя совсем не так, как металл. Если при аварии пластмассовая деталь не растрескивается, то на большинстве разновидностях пластика деформированный участок достаточно легко можно восстановить и придать первоначальную форму с помощью выдавливания с нагревом термопистолетом, ИФК-сушкой и др. Армированные, стеклопластики практически во всех случаях растрескиваются или разрываются. Так или иначе, но шпатлевание пластиковых поверхностей необходимо сводить к минимально возможному: сколы, царапины, склеенные участки, незначительные неровности. Выполнять эту операцию необходимо специальными шпатлевками, обладающими, прежде всего, высокими эластичными свойствами.
Грунтование
Одно простое правило поможет маляру избавиться от проблем с адгезией лакокрасочных материалов с пластиковыми поверхностями. Если пластмассовая деталь изготовлена из различных модификаций полипропилена (напомним, в обозначении пластика это всегда будет отражено двумя первыми буквами >PP…<) обязательно надо в качестве первичного использовать адгезионный грунт для пластика Sealer Plast 80. Sealer Plast 80 рекомендуется наносить двумя равномерными слоями широким факелом по всей поверхности детали. Не рекомендуется предварительно тщательно прокрашивать тонким факелом периметр, ребра жесткости и торцы элемента. Именно в этих местах следует опасаться превышения нанесенного слоя и возможного стекания грунта. Это ведь очень жидкий материал, состоящий на 93% из органических растворителей. Для достижения качественной адгезии с полипропиленовой поверхностью вполне достаточно 5 мкм сухой пленки. Значительное превышение этого параметра может стать причиной ухудшения адгезии всего покрытия. В местах превышения толщины Sealer Plast 80 возможно сжатие следующих слоев наносимых грунтов и даже позже – краски. На все другие типы пластика во всех их композициях можно применять все остальные грунты-подклады, наполнительные грунты во всех применяемых версиях практически без ограничений. Вот неполный перечень самых распространенных типов пластика, которые не требуют предварительного нанесения адгезионного грунта Sealer Plast 80.PVC, PMMA, PC, ABS, PA, PUR, PBTB, POM, PE, Kevlar, Gelcoat и др.Вот так все просто. В принципе, какие могут возникнуть проблемы, если полиуретановый грунт наноситься на полиуретановый бампер? И, конечно, не забывайте всегда добавлять в грунты, применяемые на пластмассовых деталях пластификатор RM Flex в количестве от 20 до 50% в зависимости от жесткости пластика.
Эта необходимость объясняется не только эластичностью самого пластика — при эксплуатации бамперы ведь не изгибаются постоянно. Дело в том, что пластик имеет высокий коэффициент температурного расширения и соответственно сжатия. Пластификатор помогает придать этот параметр лакокрасочным материалам, нанесенным на поверхность пластмассы. Нетрудно сделать вывод, что качественное покрытие с пластиками достигается благодаря высоким адгезионным свойствам используемых грунтов. Можно немного порассуждать на этот счет об антикоррозионных грунтах. Многие из читателей давно пользуются продукцией R-M и знают прекрасные адгезионные свойства антикоррозионного грунта на эпоксидной основе Euroxy. Мы можем с большой долей уверенности сказать, что, благодаря этим свойствам, он вполне мог бы использоваться в качестве первичного материала на пластмассовых деталях, не смотря на свое прямое предназначение использования на металл. Читатели могут не сомневаться: адгезия этого грунта со многими типами пластика будет прекрасной! И, тем не менее, есть одно ограничение в этом не совсем логичном действе. Euroxy не обладает достаточной эластичностью, а RM Flex с этим грунтом не используется. Тем не менее, если вам вдруг придется иметь дело с жесткими пластмассами, например, при ремонте углепластика гоночных болидов (Carbon fibre), применение в качестве грунта Euroxy должно носить обязательный характер. И еще один, очевидный всем факт, но остановиться на нем стоило бы. Каким бы сложным не был ремонт пластика, использование на нем жидкой шпатлевки должно быть полностью исключено. Вняв такому количеству информации, читатели, вероятно, будут разочарованы. Как? Все грунты на все типы пластика? Все настолько просто и универсально? Да, это так! Только универсальность эта достигнута благодаря высокой технологичности материалов для подготовки и окраски, выпускаемой ведущим производителем лакокрасочных материалов — компанией RM, позволяющим легко и без особой сложности выполнять ремонты на всем многообразии пластмассовых деталей одними и те ми же продуктами.
Сушка
Многие специалисты рекомендуют использовать при окраске пластика естественную сушку или температуру не более 40-45С. Должны признать, такая «перестраховка» достаточно оправдана. И все же, поверьте нашему многолетнему опыту, при правильном подходе к ремонту, который был так подробно описан выше, более интенсивный прогрев при 60ОС не выявит никаких проблем. А качество покрытия от этого только улучшиться. С ИФК – сушкой же будьте осторожны! Температуру нагрева поверхности пластмассовых деталей вы не сможете контролировать.
Проверка адгезии
Все мы живые люди. Случайная царапина на свежеокрашенной дверце при ее установке на автомобиль никогда не влечет за собой «слезание» краски со всей поверхности. С пластиком же такое может произойти запросто. И маляр приходит в ужас: все покрытия с бампера после сушки можно играючи снимать, как кожу после чрезмерного загара! Все ведь делалось по технологии! Что же делать? Причин для беспокойства совершенно нет! Если все сделано правильно, пройдет несколько дней, и адгезия на пластике достигнет своих нормальных параметров. Баллада о неизвестном пластике Вот вы держите в руках пластмассовую деталь, не имеющую никаких опознавательных знаков. Но как бы красиво она смотрелась, окрашенная в выбранную вами краску! Многие пластиковые детали изготавливаются из различных типов полимеров, которые могут неадекватно реагировать с растворителями, присутствующими в грунтах и красках R-M. Например, полистирол. Различные неответственные элементы салона, иногда зеркала внешнего вида, спойлеры, колпаки колес, большой спектр ремонтных запчастей, нелицензионно выпускаемые детали могут изготавливаться из композиций различных пластмасс, проще говоря, отходов или продуктов вторичной переработки и как правило уже не маркироваться.
Стандартное использование на них грунта может привести даже при отличной последующей адгезии к деформации пластика или поверхностному выявленью его внутренней структуры (различные разводы, микросетка и пр.). Визуально это не очень красиво. Для определения последовательности работы с необозначенным типом пластмассы мы рекомендуем провести так называемый «сольвент-тест». Протрите «безымянный» пластик обильно смоченной в обезжириватель RM Pre Cleano 900 тканью и, если будет выявлено явное растворение поверхности пластмассы, вы должны следовать следующим рекомендациям. Использование в этом случае Sealer plast 80 нецелесообразно. Лучше применить сразу грунт-наполнитель или грунт-подклад с его последующей сушкой и шлифовкой. Наносить грунты рекомендуется тонкими аккуратными слоями. Версию окраски «мокрое на мокрое» лучше не применять. При определении технологии окраски пластика многие мастера часто руководствуются личным опытом: паяльником плавится, растворителем не растворяется, темного цвета — полипропилен – надо начинать с Sealer plast 80. Если бы все было так просто! Был забавный звонок: «Мы хотим покрасить какие-то кронштейны при каком-то очередном тюнинге. Пластик не плавиться паяльником, не горит, не растворяется растворителем. Надо ли наносить предварительно Sealer plast 80?» Ничего другого не оставалось, как ответить: «Попробуйте сначала напильником!» Действо тут же произвелось, не вешая трубки, и ответ был забавным и все объясняющим: «Спасибо! Значит Euroxy надо». Пластики обычно горят, плавятся или растворяются. Но сказать марку пластика, руководствуясь одним, несколькими или совокупностью этих весьма субъективных параметров нельзя. Анализ пластмасс производится в лабораториях по различным показателям: по спектрограмме сгорания, реакции на различные реактивы, запаху, температуре плавления и пр. Так что сольвент-тест в таком случае самый надежный метод. Не указан тип пластика, не реагирует на Pre Cleano 900 – начинайте с Sealer Plast 80.
Руководство по производственным процессам для пластмасс
Ротационное формование (также называемое ротационным формованием) — это процесс, который включает нагрев полой формы, заполненной порошкообразным термопластом и вращающейся вокруг двух осей для производства в основном больших полых объектов. Также доступны процессы центробежного формования термореактивных пластиков, но они менее распространены.
- Загрузка: Пластиковый порошок загружается в полость формы, а затем устанавливаются остальные части формы, закрывая полость для нагрева.
- Нагрев: Форму нагревают до тех пор, пока пластиковый порошок не расплавится и не прилипнет к стенкам формы, при этом форма вращается вдоль двух перпендикулярных осей, чтобы обеспечить однородное пластиковое покрытие.
- Охлаждение: Форма медленно охлаждается, в то время как форма остается в движении, чтобы гарантировать, что оболочка детали не провиснет или не разрушится до полного затвердевания.
- Удаление детали: Деталь отделяется от формы, любые высечки удаляются.
Ротационное формование требует менее дорогих инструментов, чем другие методы формования, поскольку в процессе заполнения формы используется центробежная сила, а не давление. Формы могут быть изготовлены, обработаны на станке с ЧПУ, отлиты или сформированы из эпоксидной смолы или алюминия с меньшими затратами и намного быстрее, чем инструменты для других процессов формования, особенно для крупных деталей.
Ротационное формование позволяет получать детали с почти одинаковой толщиной стенок. После того, как инструменты и процесс настроены, стоимость детали очень низкая по сравнению с размером детали.Также в форму можно добавлять готовые детали, такие как металлическая резьба, внутренние трубы и конструкции.
Эти факторы делают ротационное формование идеальным для мелкосерийного производства или в качестве альтернативы выдувному формованию для небольших объемов. Типичные изделия, изготовленные методом центробежного формования, включают цистерны, буи, большие контейнеры, игрушки, шлемы и корпуса каноэ.
Ротомолдинг имеет некоторые конструктивные ограничения, а готовая продукция имеет более низкие допуски. Поскольку вся пресс-форма должна быть нагрета и охлаждена, процесс также имеет длительное время цикла и является довольно трудоемким, что ограничивает его эффективность для приложений с большим объемом.
Наиболее распространенным материалом для ротационного формования является полиэтилен (ПЭ), который используется в 80% случаев, в основном потому, что ПЭ можно легко измельчить в порошок при комнатной температуре.
Обычно к пластикам, полученным роторным формованием, относятся:
- Полиэтилен
- Полипропилен
- Поливинилхлорид
- нейлон
- Поликарбонат
Отливка из пластмассы 101: описание типов
В сегодняшнем постоянно развивающемся мире производства пластмассы используются для изготовления всего, от деталей автомобильных кузовов до синтетических деталей человеческого тела.Для создания критически важных компонентов и обеспечения оптимальной производительности многие производители предпочитают использовать литье пластмасс под давлением.
Для удовлетворения различных потребностей отрасли существует несколько других типов пластиковых формованных изделий, каждый из которых обладает уникальными характеристиками и преимуществами. Конкретные спецификации и требования приложения определяют, какой тип процесса формования лучше всего подходит для конкретной детали.
Ниже приведены несколько наиболее распространенных различных стилей литья пластмасс.
Выдувное формование
Процесс выдувного формования следует тем же основным этапам, что и в искусстве выдувания стекла. Для выдувания детали производитель надувает заготовку — нагретую пластиковую массу, обычно в форме трубки — воздухом. Заготовка надувается до тех пор, пока не заполнит форму и не примет ее форму. Таким образом, пластик приобретает желаемую форму. После охлаждения вновь сформированная пластиковая деталь выталкивается из формы.
Выдувное формование особенно полезно для экономичного производства цельных полых предметов в больших объемах, поскольку этот процесс позволяет быстро создавать однородные тонкостенные контейнеры, идеально подходящие для небольших предметов, таких как бутылки, а также для более крупных, таких как контейнеры для хранения и бочки.
В зависимости от конкретного применения производители могут использовать различные термопласты при выдувном формовании, чтобы создать более индивидуальный продукт. Обычно обрабатываемые материалы включают полиэтилен низкой плотности, полиэтилен высокой плотности, полиэтилентерефталат, полипропилен и поливинилхлорид.
Компрессионное формование
Компрессионное формование включает помещение нагретого пластика внутрь нагретой формы с последующим закрытием ее для придания пластику желаемой формы.После охлаждения деталь вынимается из формы. Процесс нагрева, называемый отверждением, помогает гарантировать, что конечный продукт сохранит свою целостность и форму.
Компрессионное формование предлагает множество уникальных преимуществ; это одновременно рентабельно и высокоэффективно. Этот процесс также довольно универсален, что позволяет производителям создавать детали, которые сильно различаются по толщине, длине и сложности.
Поскольку при компрессионном формовании часто используются передовые композиты для пластика, этот процесс позволяет получать более прочные и долговечные детали, что делает его популярным в различных отраслях промышленности.Например, при компрессионном формовании часто используются высокопрочные материалы, такие как термореактивные смолы, стекловолокно и армированные пластмассы, в результате чего получаются более прочные и эластичные изделия, чем изделия, предлагаемые другими процессами формования.
Позволяя создавать высокопрочные детали, компрессионное формование используется для производства компонентов для широкого спектра применений, включая автомобильные детали, бытовую технику, застежки для одежды и бронежилеты.
Экструзионное формование
В то время как другие формы формования пластика используют экструзию для вставки пластмассовых смол в форму, при экструзионном формовании расплавленный пластиковый материал экструдируется непосредственно в матрицу.Этот процесс уникален тем, что форма штампа, а не пресс-формы, определяет форму конечного продукта.
Экструзионное формование идеально подходит для изготовления деталей постоянной длины и одинакового поперечного сечения. Подобно машине для литья пластмасс под давлением, машина для экструзионного формования имеет винт, который поворачивается, чтобы подавать пластиковую смолу в питатель. Расплавленный пластик затем проходит через фильеру, образуя длинную трубчатую форму. Форма матрицы определяет форму пластиковой трубки.Как только экструзия остынет, ее вынимают из машины.
Экструзионное формование хорошо подходит для изготовления длинных полых изделий, таких как трубы, трубы и соломинки. Кроме того, производители могут создавать эти детали самых разных форм, включая Т-образные, U-образные, квадратные, двутавровые, L-образные и круглые сечения.
Литье под давлением
Из различных доступных процессов формования литье под давлением считается наиболее универсальным, поскольку с его помощью можно создавать самые разные детали, как по размеру, так и по форме.Прессы также бывают разных размеров в зависимости от давления, которое они оказывают, и их мощности.
Основные принципы литья под давлением довольно просты, но реальный процесс может быть довольно сложным, когда дело доходит до поддержания однородности деталей. Процесс включает в себя впрыскивание расплавленного пластика в форму, которая сделана из стали. Сама форма имеет полости, которые будут формировать детали; после впрыска расплавленный пластик заполняет полости и остальную часть формы. После охлаждения детали выталкиваются штифтами.
Благодаря своей универсальности, литье под давлением можно использовать для создания всего, от крупных автомобильных деталей до небольших сложных деталей, используемых в хирургическом оборудовании. Литье под давлением также обеспечивает высокий уровень настройки, поскольку можно использовать различные пластмассовые смолы и добавки, что позволяет дизайнерам и инженерам создавать уникальные детали для удовлетворения очень сложных или необычных потребностей приложений. И есть некоторые улучшения и доступные методы, такие как множество вариантов смолы и отделки, для производителей, которые хотят создавать еще более специализированные детали.
Хотя изначально изготовление самих форм может быть дорогостоящим, после их изготовления производственные затраты становятся довольно низкими. Фактически, литье под давлением лучше всего подходит для создания очень больших объемов точных деталей; после начала производства стоимость детали значительно снижается, что делает процесс очень экономичным при больших объемах производства.
Литье пластмасс под давлением — это высоконадежное решение для производства большого количества точных и стабильных компонентов. Он также более эффективен и экономичен, чем другие стили формования, так как производит гораздо меньше отходов.В результате литье под давлением чаще всего используется для изготовления высококачественных деталей в больших объемах.
Ротационное формование
Ротационное формование, также известное как ротационное формование, использует высокие температуры и вращательное движение для покрытия внутренней части формы для придания детали желаемой формы. Сначала форма заполняется полимерным порошком. Затем нагретая форма вращается по двум перпендикулярным осям, так что порошок прилипает ко всей внутренней части формы. По мере того как она продолжает вращаться, форма в конечном итоге охлаждается и удаляется, образуя в конечном итоге компонент с ровными стенками.
Ротационное формование лучше всего подходит для создания больших, полых, неразъемных контейнеров, таких как резервуары. Несмотря на то, что это рентабельный, это не быстрый процесс. Однако при центробежном формовании расходуется мало материала, а избыток материала часто можно использовать повторно, что делает его экономичным и экологически безопасным производственным процессом.
Другие ключевые преимущества включают возможность производства деталей с постоянной толщиной стенок, повышенную гибкость конструкции и большую прочность.
Введение в литье пластмасс под давлением электронная книга
Откройте для себя мир литья пластмасс под давлением с уверенностью
Загрузите нашу электронную книгу «Введение в литье пластмасс под давлением». Внутри мы покрываем:
- Виды литья пластмасс, их преимущества и применение
- Типы прессов, их возможности и преимущества
- Как определить стоимость литья пластмасс под давлением
- Распространенные ошибки, которых следует избегать
Узнать больше
Каждый из этих процессов формования пластмасс обладает уникальными характеристиками и преимуществами, благодаря чему каждый стиль хорошо подходит для различных типов применений.На
В Rodon Group наши дизайнеры и инженеры хорошо разбираются в технологиях литья пластмасс под давлением в больших объемах и работают в тесном сотрудничестве со всеми нашими клиентами, чтобы удовлетворить их уникальные потребности. В большинстве ситуаций есть несколько способов решения производственных задач, и мы можем предоставить экспертную информацию о различных методах и материалах, наиболее подходящих для конкретного проекта.
Чтобы узнать больше о литье пластмасс под давлением и о том, как это может помочь в вашем следующем проекте, загрузите нашу бесплатную электронную книгу «Литье пластмасс под давлением 101.”
3. Производство: материалы и обработка | Наука и инженерия полимеров: новые горизонты исследований
реакций конденсации были использованы для создания гибридных гелей, которые не усаживаются при сушке.
Выделение молекул органических красителей, жидких кристаллов или биологически активных частиц в неорганических или гибридных матрицах привело к появлению огромного множества композитных оптических материалов, которые в настоящее время разрабатываются в качестве лазеров, датчиков, дисплеев, фотохромных переключателей и нелинейно-оптических устройств.Эти материалы превосходят композиты с органической матрицей, потому что неорганическая матрица (обычно кремнезем) имеет больший коэффициент пропускания и менее подвержена фотодеградации. Органические молекулы, встроенные в неорганические матрицы, также могут служить шаблонами для создания пористости. Удаление шаблонов термолизом, фотолизом или гидролизом создает поры четко определенных размеров и форм. Неорганические материалы с заданной пористостью в настоящее время представляют интерес для мембран, сенсоров, катализаторов и хроматографии.
Неорганические, металлоорганические и гибридные полимеры и сетки представляют собой потенциально огромный класс материалов с практически неограниченными проблемами синтеза и обработки. Предполагается, что будущие исследования продолжат изучение периодической таблицы в поисках новых комбинаций материалов, новых молекулярных структур и улучшенных свойств. Гибридные системы особенно удобны для исследований в области многофункциональных материалов, то есть интеллектуальных материалов, которые одновременно выполняют несколько оптических, химических, электронных или физических функций.Также ожидается разработка гибридных материалов, которые демонстрируют исключительную прочность и вязкость разрушения природных материалов, таких как скорлупа и кость. Замечательная универсальность полифосфазенов и полисилоксанов будет по-прежнему использоваться для биомедицинских приложений, таких как доставка лекарств и замена органов и мягких тканей, а также усовершенствованные эластомеры, покрытия и мембраны.
Будущее прекерамических полимеров и золь-гель-систем кажется светлым. Основной задачей является разработка способов получения чистой стехиометрической неоксидной керамики, особенно SiC, которая демонстрирует прядильность и высокий выход керамики.Новые пути синтеза, такие как подходы к созданию «молекулярных строительных блоков» для многокомпонентной керамики, будут изучены для получения сверхпроводниковых, сегнетоэлектрических, нелинейно-оптических и ионно-проводящих фаз, в основном в форме тонких пленок. Использование золь-гель обработки для получения «индивидуальных» фаз. Пористые материалы для применения в сенсорах, мембранах, катализаторах, адсорбентах и хроматографии являются особенно привлекательной областью исследований и разработок.
ОБРАБОТКА ПОЛИМЕРАРост объемов полимеров и их использования, как описано выше, отчасти связан с простотой их обработки.Вопреки распространенному мнению, пластмассы часто дороже стали, то есть в расчете на фунт, но они также намного легче стали, стекла или алюминия. Огромное преимущество полимеров заключается в том, что их можно обрабатывать многими способами за
ед.Методы изготовления и методы изготовления пластмассы
Изготовление пластмассы — это проектирование, производство или сборка пластмассовых изделий одним из нескольких способов. Некоторые производители предпочитают изготовление из пластмассы работе с другими материалами (например, металлом или стеклом) из-за преимуществ этого процесса в определенных областях применения.
Пластиковые бутылки: изделия из пластмассыКредит изображения: Tezzstock / Shutterstock
Методы изготовления пластмасс
Податливость и экономичностьPlastic делают его универсальным и прочным материалом для целого ряда различных продуктов.
Сварка пластмасс
Подобно сварке металлов, сварка пластмасс предполагает использование тепла для плавления двух или более деталей вместе. Этот процесс эффективен при работе с термопластами, непригодными для клеевого связывания.Отдельные детали часто сплавлены с помощью наполнителя между ними, особенно если пластмассы имеют резко различающиеся точки плавления. Сварку можно выполнять несколькими различными методами, включая выброс горячего газа, высокочастотную вибрацию, вращение или контактную сварку. Оборудование, используемое для сварки пластмасс, зависит от выбранного процесса и типа используемого пластика.
Компаундирование (или смешение) методов изготовления пластмасс
Компаундирование — это тип изготовления, при котором два или более пластика объединяются в амальгаму перед формированием из них одной детали.Он включает в себя смешивание расплавленных пластмасс в соответствии с точными спецификациями с последующим их формованием с помощью пресс-формы, штампа или другого формовочного инструмента.
Компаундирование часто используется для облегчения обработки данного материала или для улучшения характеристик продукта. Комбинируя преимущества и недостатки нескольких типов пластика, процесс может привести к получению уникального материала, подходящего для конкретного применения. Некоторые распространенные типы пластиковых компаундов включают:
- Полимерные наполнители
- Базовые смолы
- Суперконцентраты пигментов
- Пенообразователи
- Огнезащитные составы
- Соединения для продувки
Ламинирование пластика
Пластиковая ламинация создает барьер на поверхности другого материала.Этот процесс чаще всего используется для улучшения долговечности, улучшения стиля или эстетического качества продукта. Это также может быть рентабельной мерой за счет защиты чувствительного или подверженного износу материала и уменьшения его потенциальной потребности в обслуживании.
Пленка и смола — два наиболее распространенных типа ламинирования. В обоих процессах к изготовленной пленке прикладываются тепло и давление, чтобы обеспечить ее адгезию к движущейся подложке. Пленочное ламинирование более эффективно для образования пластикового барьера на внешней стороне продукта, в то время как ламинирование смолой чаще используется для создания адгезионного слоя между двумя подложками.Бумага, ткань, металлическая пленка и гибкий пенопласт — обычные материалы для ламинирования.
Процессы формования
При формовании пластика пластику придают заданную форму, позволяя нагретой гибкой заготовке остыть и затвердеть вокруг или внутри формы. Существует множество методов формования пластмасс, включая литье под давлением, выдувное формование и ротационное формование. Выдувное формование часто используется для создания контейнеров, таких как бутылки или топливные баки, в то время как литье под давлением полезно в приложениях, требующих более высокого индекса расплава, таких как производство посуды.В результате ротационного формования получаются полые пластмассовые изделия, такие как каноэ, игрушки, буи и автомобильные детали.
Экструзия пластика
Экструзия пластика может использоваться для создания труб, трубопроводов или листовых компонентов. Он также применяется для повышения эффективности последующих стадий формования или обработки. Например, экструзия пластика часто предшествует процедурам адгезии или ламинирования.
Экструзия профиля и экструзия листа являются наиболее распространенными формами этого процесса.Чтобы кратко описать процесс экструзии пластика: экструзия профиля использует одношнековый экструдер для плавления пластиковых гранул, перемещения расплавленного пластика через винтовой механизм под давлением и нагнетания его в кольцевую головку. Затем пластик затвердевает вокруг калибровочной гильзы, образуя трубу или трубчатый компонент определенного диаметра. Неудивительно, что экструзия листов использует аналогичную технику для создания тонких пластиковых листов.
Вспенивание пластика
Пенопласту можно придавать самые разные формы.Общие конфигурации вспенивания включают круглые, листовые, пленочные, сплошные доски, стержни и булочки. Для достижения желаемых характеристик полимерные композиты обычно формуют с помощью процесса физического или химического выдувания. Как и при смешивании, в основной материал могут быть включены такие добавки, как пигменты, антиоксиданты и антипирены, чтобы оптимизировать характеристики продукта для пользователя.
Выбор процесса изготовления пластмассы
Функциональность продукта и простота изготовления — важные факторы, которые следует учитывать при выборе процесса изготовления пластмассы.Некоторые методы неэффективны для изготовления определенных типов пластика и поэтому могут оказаться бесполезными для вашего конкретного проекта. Некоторые другие проблемы, о которых следует помнить, включают:
- Потребность в отдельных пластмассах по сравнению с пластиковыми компаундами
- Предполагаемое соотношение пластика и непластика в продукте
- Роль пластика в вашем производственном процессе (как склеивание, ламинирование или основной продукт)
- Размеры и использование конечного продукта.
Ресурсы
- Определения пластмасс
- Виды пластмасс
- Изготовление пластмасс для наук о жизни
Прочие изделия из пластмассы
Больше от Plastics & Rubber
компаний по производству пластмасс | Услуги по изготовлению пластмасс
Список компаний по изготовлению пластмасс
Грубо говоря, пластик может относиться к любому синтетическому полимеру, который напоминает природные смолы. (Полимер — это чрезвычайно длинная молекулярная цепь; смолы — это уникальные вязкие органические соединения, нерастворимые в воде и способные превращаться в твердые вещества.) Производство пластмасс, в частности, относится к любому промышленному процессу, который вносит вклад в общий процесс преобразования пластиковой смолы в практичные потребительские товары. Производство пластмасс можно разделить на подкатегории: проектирование, производство и сборка.
ИсторияИстория пластмасс может сбивать с толку из-за гибкости определения «пластик». Природные вещества, напоминающие пластик, такие как рог и резина, использовались цивилизацией на протяжении тысячелетий.Однако подлинное появление современного пластика невозможно проследить раньше, чем промышленная революция и середина 19 века. Британскому изобретателю Александру Парксу часто приписывают самое раннее изобретение «пластика» через изобретение «Паркезина», материала на основе целлюлозы, который был представлен на Большой выставке в Лондоне (1862 г.). «Паркезин» был получен путем растворения нитрата целлюлозы в растворителе и последующего помещения его на нагревающуюся вальцовочную машину. Вскоре после этого два американских брата (Хиатты) добавили в эту смесь камфору, создав целлулоид (ок.1870 г.). Однако полностью синтетический пластик появится только в 20 веке. С 1907 по 1909 год бельгийско-американский доктор Лео Бэкеланд создал Бэкелит, пластик на основе ископаемого топлива, который в конечном итоге применялся для изготовления корпусов радио- и телефонных аппаратов, электрических изоляторов, кухонной посуды, ювелирных изделий и т. Д. Основным ингредиентом Бэкеланда был фенол, каменноугольная смола кислота. В последующие десятилетия были разработаны другие формы синтетического пластика (например, полистирола, полиэстера). По иронии судьбы, травмы двух мировых войн помогли закрепить важность пластика для военных применений — и, кстати, для потребительских приложений (поскольку возникший избыток пластика потребовался перепрофилировать после 1945 года).Появление Tupperware в 1948 году ознаменовало собой одно из первых широко распространенных применений коммерческого пластика. (Для получения дополнительной информации об истории пластика см. Пластиковые материалы и пластиковые контейнеры.)
Производство пластмасс — Park Plastic Products Преимущества
Пластик стал чрезвычайно популярной альтернативой другим материалам, таким как стекло, металлы и дерево. по целому ряду причин. Во-первых, пластик невероятно универсален. Ему можно придать практически любую геометрию или любую вообразимую форму.Пластик более удобен в использовании, чем другие материалы. Многие потребители предпочитают использовать пластик, а не металл, поскольку он легче и безопаснее, хотя во многих аспектах столь же эффективен. Кроме того, это недорогое решение, позволяющее производителям работать с меньшими затратами при меньших затратах. Одно из самых ценных свойств пластика — его долговечность. Пластик устойчив к нескольким веществам и условиям, таким как абразивные химические вещества, высокие удары, экстремальные температуры, вибрация, влага и давление.Кроме того, в отличие от многих металлов, пластик не окисляется под воздействием воды, поэтому его лучше использовать на открытом воздухе.
Основными недостатками производства и использования пластмасс являются экологические. Некоторые методы производства пластика имеют негативные последствия для окружающей среды и здоровья. Например, процесс «распыления» при производстве пластика приводит к попаданию в атмосферу летучих органических соединений (ЛОС), таких как стирол.
Этапы производства пластмассЧтобы удовлетворить разнообразные потребности широкого спектра отраслей, производители пластмасс полагаются на широкий спектр производственных процессов с использованием широкого спектра производственного оборудования.Некоторые из наиболее известных производственных процессов включают экструзию, литье под давлением, сварку, механическую обработку, штамповку и механическую обработку. Классификация промышленных процессов производства пластмасс зависит от множества факторов, включая характер конкретных конечных продуктов и характер самого процесса. Для практических целей различные производственные процессы будут сгруппированы по двум из трех основных этапов изготовления пластмассы: изготовление и сборка.
Производство
На начальных этапах производства пластмасс подавляющее большинство пластмасс доставляется производителю в виде необработанной смолы (в виде хлопьев, порошка или небольших гранул).Это сырье может быть производным органическим материалом, который в конечном итоге будет преобразован (например, целлюлоза из древесины), или из соединений ископаемого топлива (нефть, природный газ, уголь и т. Д.). Вообще говоря, в основе пластиков лежит углерод. (Основное исключение составляют силиконы на основе кремния.) Кроме того, пластмассы делятся на две широкие категории: термопласты (которые можно плавить и повторно формовать после производства) и термореактивные пластмассы (которые нельзя плавить и повторно формовать после производства).Сырье очищается, а затем реорганизуется (посредством реакций присоединения или конденсации) в полимеры, которые будут подвергаться фактическому процессу образования. Часто пластмассовые смолы комбинируют друг с другом в различных процессах смешивания или улучшают за счет введения добавок (подробнее будет обсуждаться ниже).
Чтобы превратить пластмассовую смолу в пригодные для использования детали или изделия, производители пластмассы могут выбирать из множества методов изготовления. Формование — это, безусловно, самая распространенная форма изготовления пластмассовых изделий.Как следует из названия, это семейство связанных процессов вращается вокруг использования формы для удержания и охлаждения нагретой пластмассовой смолы. Гранулы пластикового сырья (как смолы, так и добавки) расплавляют и смешивают с жидкостью соответствующего типа перед тем, как поместить в форму при повышенных температурах и / или давлении. Некоторые из наиболее актуальных типов литья включают:
Литье под давлением — самая распространенная форма изготовления пластмасс. В этом методе пластиковый материал с силой сжимается или впрыскивается в закрытую форму и ему дают остыть.Эпоксидная смола, полиэфир и полиуретан — это некоторые из пластмассовых смол, которые обычно производятся этим методом. Этот метод особенно полезен для продуктов, требующих высокой температуры плавления (например, посуды). Некоторые варианты литья под давлением включают реакционное литье под давлением (используемое для термореактивных материалов), усиленное реакционное литье под давлением и структурное реакционное литье под давлением (оба из которых усиливают полимеры рубленым стеклом / волокном или матовым волокном).
Ротационное формование или центробежное литье инжектирует пластиковую смолу в прядильную форму, выложенную ткаными матами.Центробежное движение формы заставляет смолу пропитать маты в процессе отверждения. Изделия ротационного формования обычно представляют собой полые объекты, такие как трубы, резервуары, различные автомобильные детали, каноэ и т. Д.
Выдувное формование получил свое название от использования сжатого воздуха для надувания предварительно сформированной термопластической трубки, чтобы она приняла форму. пресс-формы. Дополнительными подкатегориями выдувного формования являются экструзионно-раздувное формование и литье под давлением с раздувом. Эти подкатегории разграничены методом формирования предварительно сформированного термопластичного компонента (известного как заготовка).Контейнеры, такие как бутылки или резервуары, являются одними из наиболее распространенных продуктов выдувного формования.
Компрессионное формование — это более традиционная форма изготовления пластмасс, в которой используется листовой формовочный состав (SMC) или ванна из пластмассы, содержащей встроенные стекловолокна. Гидравлический пресс используется для отверждения этого материала под воздействием высоких температур и давления. Хотя этот метод не так распространен, как другие методы формования из-за высокой стоимости, он все еще используется в больших объемах производства для производства таких предметов, как автомобильные крылья и застежки для одежды.
Экструзия — еще одно семейство производственных процессов. Вместо того, чтобы просто выдавливать пластиковую смолу в форму, экструзия проталкивает смолу через нагретый цилиндр под давлением в матрицу для изготовления основных форм, таких как пластиковые листы и трубы. Экструзия может использоваться для создания форм, которые затем будут отформованы, или ее можно использовать для создания «отдельных» объектов. Пултрузия считается противоположностью экструзии, поскольку для достижения аналогичных целей она основывается на вытягивании, а не на толкающих силах.Как и литье под давлением, экструзия представляет собой процесс термоформования, что означает, что он включает плавление смолы, чтобы протолкнуть ее через пресс-форму или полость пресс-формы и принять форму пресс-формы или пресс-формы по мере ее охлаждения и затвердевания.
Многослойные методы производства пластмассы включают укладку сухих листов (известных как слои) в открытые формы и покрытие их пластмассовой смолой для отверждения под давлением. Давление часто прикладывается (вручную) с помощью инструментов, известных как ручные ролики. Сухие слои пропитывают слои в конце процесса укладки, в то время как влажные слои пропитывают слои один за другим по мере их укладки (для более равномерного распределения смолы).Метод напыления (упомянутый ранее) представляет собой «автоматическую» версию ручных методов укладки с использованием пневматического пистолета. Нередко при производстве пластмасс одновременно используются как ручной, так и автоматический методы «укладки» для повышения прочности готового продукта.
Трансферное формование смолой похоже на методы «укладки», так как оно также формирует пластик путем пропитывания сеток армированной волокном смолой. Основное различие между двумя категориями изготовления пластмасс заключается в том, что трансферное формование полагается на закрытые формы, а не на открытые.Стандартные методы впрыска часто используются для впрыска смолы в закрытую форму. Смолу можно впрыскивать с помощью вакуума в варианте, известном как литье с переносом смолы с помощью вакуума или просто вакуумное формование.
Сборка
Любая операция по изготовлению пластика, которая происходит после того, как основной пластик уже сформирован, может быть объединена в категорию постобработки. Механические процессы, такие как сборка пластика, гибка, резка, сверление, гравировка, травление, штамповка, штамповка и нарезание резьбы, — все это процессы изготовления после формования.Хотя они требуются только для определенных областей применения пластмасс, подобные процессы не редкость и позволяют производителям пластмасс вносить любые необходимые изменения. Такие операции, как сварка, резка и склейка, можно отнести к категории сборочных операций, которые, в частности, помогают формировать готовые изделия за счет соединения различных пластиковых деталей.
Резка позволяет дополнительно придавать форму пластику для конкретных применений после того, как он был сформирован и отформован. Почти всегда изготовление пластмассы поддерживается автоматизированным компьютерным программным обеспечением, которое называется программным обеспечением с числовым программным управлением (ЧПУ).Это особенно актуально на этапах резки пластмассовых изделий. Станки с ЧПУ ускоряют и оптимизируют операции намного больше, чем обычные технические специалисты, и делают человеческий фактор практически неважным, помогая производить большие объемы идентичных, очень сложных деталей и продуктов. Маршруты с ЧПУ, фрезерные станки с ЧПУ и токарные станки с ЧПУ — это лишь некоторые примеры сложного оборудования, используемого для резки, в то время как ружейное сверление и бесцентровое шлифование представляют собой специализированные процессы резки, позволяющие получать особые формы.Более традиционная механическая высечка все еще используется производителями пластмасс наряду с более продвинутыми формами ЧПУ и / или лазерной резки.
Строго говоря, сборочные операции относятся к любому процессу, который объединяет различные пластмассовые детали для создания пластмассового изделия или части пластмассового изделия. Склеивание и соединение (механическим креплением) — два распространенных метода сборки. Другой процесс изготовления, сварка пластика, включает нагрев двух кусков термопласта до тех пор, пока они не станут вязкими, а затем их сжимание, позволяя их молекулам смешаться в одну деталь.Сварка особенно полезна для пластика, который плохо реагирует на адгезию. Некоторые подкатегории включают выбросы горячего газа, высокочастотную вибрацию и контактную сварку.
Когда пластик ламинируется, он используется для создания поверхностного барьера для другого типа материала. Обычно он используется для увеличения прочности другого материала или категории химической стойкости (например, электрической, химической и т. Д.). При ламинировании пленкой пластик помещается на внешнюю поверхность продукта, а при ламинировании смолой ламинат помещается между парой подложек.
Пластмасса также может подвергаться различным процессам окончательной отделки в эстетических или других целях. Полировка, полировка, порошковое покрытие, шелкография и т. Д. Являются примерами различных конечных процессов, которые могут применяться к пластмассовым изделиям.
Даже краткий обзор методов изготовления пластмассы подчеркивает отсутствие строгой хронологии, которая характеризует весь процесс изготовления пластмассы. Например, хотя экструзия часто происходит относительно рано в процессе изготовления, она также может происходить непосредственно перед более поздними процедурами, такими как склеивание или ламинирование.Точно так же процессы термоформования могут быть строго ограничены методами формования, или они могут происходить в большей или меньшей степени в сочетании с более поздними методами постобработки (такими как сгибание пластикового листа на ленточном нагревателе). Использование добавок в производстве пластмасс наглядно демонстрирует гибкость порядка в производстве пластмасс. При изготовлении пластмасс используются многие типы химических добавок, таких как пластификаторы (для повышения гибкости), модификаторы удара (для увеличения поглощения ударов), внешние смазки (для уменьшения трения), наполнители / наполнители (для увеличения объема пластика), антипирены. (для уменьшения воспламеняемости), загустители (для увеличения вязкости) и т. д.Хотя многие добавки включаются в маточные партии пигментов / смол на ранних стадиях смешивания и подготовки сырья, они также могут быть добавлены в пластмассовые изделия во время сборки и других стадий «постобработки».
ПриложенияКаждая современная промышленность в значительной степени полагается на пластик. Конкретные примеры таких отраслей включают сельское хозяйство, архитектуру, автомобилестроение, химическую обработку, косметику, строительство, электронику, машиностроение, производство продуктов питания и напитков, гостиничный бизнес, медицину, освещение, упаковку и отгрузку, фармацевтику, ресторан, изготовление вывесок и производство игрушек. .(В некоторых областях используются специализированные производственные процессы. Примером может служить важность инфузии полимерной пленки для аэрокосмической промышленности.) Производители пластмасс поддерживают функционирование современного мира, бесшумно обеспечивая выполнение повседневных операций, от складирования остатков пищи в пластиковые контейнеры для хранения до включения насоса система. Для этого производители пластмасс производят ряд различных пластмасс, таких как акрил, нейлон, полиэтилен, полиэстер, полистирол, поливинилхлорид и полипропилен. (Для получения дополнительной информации о различных типах пластика см. Пластиковые материалы.)
Примеры пластиковых изделий, готовых к производству и сборке, включают тележки, стеллажи для выставки товаров, корпуса, пластиковые резервуары, вывески, ламинированные электрические изоляторы, крыши / панели грузовиков, дверцы доступа, панели управления и игрушки. Пластиковые резервуары, в частности, являются хорошим примером того, как природа конечного продукта определяет важность и характер изготовления пластмассы. Пластиковые резервуары — популярный пластиковый продукт, поскольку они в значительной степени зависят от химической коррозионной стойкости. Кроме того, цилиндрическая природа резервуаров требует очень специфических процессов изготовления, таких как вышеупомянутое ротационное формование или намотка нити (высокоавтоматизированный процесс, при котором волокна протягиваются через ванну со смолой и вокруг вращающейся оправки.) Процессы производства пластмасс создают не только независимые продукты, но и детали, которые служат важными компонентами других продуктов и систем. К таким пластмассовым деталям относятся болты, гайки, винты, направляющие кольца, уплотнительные кольца, компенсационные кольца, изоляторы, переходники, подшипники, втулки, распорки и прокладки.
СоображенияПоскольку производители пластмассовых изделий являются источником всех пластмассовых изделий, каждый потребитель пластмассовых компонентов полагается на них при создании необходимых им изделий.Все, от стандартных продуктов, таких как пластиковые шайбы, до нестандартных продуктов для специализированной электроники, должно создаваться производителем. Для производителей пластика, очевидно, важен выбор правильного процесса изготовления пластика. В целом, характер конечного продукта и гибкость процесса изготовления должны быть определяющими факторами при выборе процесса. Характер конечного продукта — включая его размеры, идеальный химический состав (например, одинарный / составной пластиковый состав, пластик / непластиковый состав) и практическое применение — определяет весь процесс производства от начала до конца.Материалы подбираются для продуктов в зависимости от того, как свойства материала будут поддерживать или улучшать требования к применению продукта. Например, пластмассовые изделия, предназначенные для использования в пищевой и медицинской промышленности, должны быть нетоксичными и устойчивыми к загрязнениям. Во избежание повреждения, загрязнения или разложения от воздействия таких веществ, как жиры, масла и биологические жидкости, они также должны быть водонепроницаемыми. Кроме того, пластмассовые материалы, из которых изготовлено оборудование и детали машин, должны обладать высокой прочностью на разрыв и способностью противостоять истиранию, воздействию влаги и масел, а также противостоять химическим веществам.Точно так же пластиковые детали, используемые в автомобильной промышленности, должны быть устойчивыми к вибрации и ударам. Гибкость определенного продукта — и, в более широком смысле, гибкость соответствующих производственных процессов — очень важна, поскольку она связана с финансовыми последствиями. Инструменты для определенных аспектов производства (например, литье под давлением) могут быть чрезвычайно дорогими. Таким образом, важно свести к минимуму изменения в конструкции продукта и применении.
Выбор поставщика пластмассовых изделий
Поиск качественного изготовителя пластмассы важен, поскольку изготовитель будет выполнять не только этапы производства и сборки для создания продукта, но часто также и начальный этап проектирования.Как показал даже краткий обзор производства пластмасс, создание пластмасс — это обманчиво сложный процесс. При участии в процессе проектирования производитель пластика должен учитывать множество факторов, таких как диапазоны рабочих температур, параметры размера, характер (твердость или мягкость), цвет и требования к пределу прочности. Как правило, производители пластмасс предлагают изделия предварительно разработанных конструкций и стандартных размеров, предоставляя клиентам примеры и размеры, из которых они могут выбирать.Тем не менее, любой достойный производитель пластмасс также охотно разработает специализированные и изготовленные на заказ детали для тех, кто их запрашивает, полагаясь на такие средства, как CAD и виртуальное 3D-прототипирование.
Производство пластмасс настолько сложно, что независимые производители обычно сосредотачиваются только на одном аспекте процесса (например, экструзии и литье под давлением). Это часто может работать на пользу заказчику, поскольку такое внимание часто соответствует глубине знаний и возможностей. Одна из областей, в которую следует обратить внимание при поиске производителя пластика, — это область контроля качества.Такие средства обеспечения качества, как строгое штрих-кодирование или система Канбан, являются долгожданными признаками добросовестности и компетентности изготовителя. Что касается работы с поставщиками пластика ближе к потребителю в цепочке поставок, важно работать с поставщиками, которые имеют тесные отношения с компаниями по производству пластика, чтобы расширить возможности изготовления на заказ. Многие стандарты, регулирующие пластмассовую промышленность, взяты из ISO. Например, стандарты, регулирующие термопласты, прилагаются к стандарту ISO 306.ISO 9001: 2008 — это более общий стандарт, ориентированный на качество обслуживания клиентов. Всегда следите за тем, чтобы производитель пластика, с которым вы работаете, имеет высокий уровень аккредитации и соблюдает отраслевые стандарты.
Производство пластмасс Информационное видео
Производство пластиковых деталей на заказ: как это делается
Пластмассы, также называемые полимерами, очень разнообразны. Они состоят из разных элементов, таких как водород, хлор, кислород и азот. У них также высокая молекулярная масса.
Промышленные пластмассы обычно предназначены для имитации компонентов натуральных материалов, таких как дерево.
Они сделаны путем переработки натуральных продуктов. Иногда они производятся путем объединения основных химических веществ из природного газа, нефти или угля.
Производство пластиковых деталей на заказ
Производство пластиковых деталей на заказ часто следует общей последовательности событий. Единственное отличие — это первичный этап изготовления, основанный на геометрии пластиковых деталей.
Учитываются и их практические требования.
Очень важно иметь представление о том, как изготавливать пластмассовые детали посредством литья пластмасс под давлением.
Шаги станут относительно простыми, если вы изучите основы производства.
Вот общее представление о том, как изготавливать пластиковые детали по индивидуальному заказу.
Предложить дизайн
Важно, чтобы вы придумали дизайн пластиковых деталей, которые вы хотите создать.
Начните с наброска дизайна на листе бумаги.
В конечном итоге ваш эскиз должен иметь достаточно деталей, чтобы вы могли нарисовать его 3D-модель.
Если у вас нет навыков, обратитесь за помощью к профессионалу.
Это также этап, на котором происходят серьезные изменения, чтобы сделать продукт доступным.
Предложение проекта группе экспертов чрезвычайно поможет вам в достижении вашей цели. Если возможно, обратитесь за помощью к экспертам по технологиям производства, чтобы доработать дизайн.
Определите, какой процесс формования пластика лучше всего подходит для данной конструкции
При производстве пластмасс используются различные методы формования.Литье под давлением по индивидуальному заказу, пожалуй, самая популярная техника.
Литье пластмасс под давлением используется для производства пластиковых деталей с использованием простой функции открывания и закрывания формы.
Выбранный вами процесс будет зависеть от разных переменных. К ним относятся ваш первоначальный дизайн, количество необходимых деталей и общее использование продуктов.
Построить прототип
Это увеличит ваши общие расходы, но разработка прототипа, напоминающего конечный продукт, будет огромным подспорьем.
Прототип также может сэкономить вам время и ресурсы в долгосрочной перспективе.
Существует множество прототипов инструментов для изготовления нестандартных пластиковых деталей, таких как прототип машины из полимера.
Построение прототипа позволит вам исправить проблемы, которые могут не проявляться на 3D-модели вашего дизайна.
Он также может определять эффективность и функциональность конечного продукта.
Сделайте дизайн
Если у вас есть средства и инструменты для изготовления пластиковых деталей по индивидуальному заказу, то делайте это тем способом, который вы выбрали.
В противном случае поищите компанию по производству пластика, которая поможет вам завершить вашу работу.
Некоторые компании производят исключительно пластиковые детали на заказ. Другие берут на себя весь процесс упаковки и отгрузки.
В конечном итоге выберите компанию, которая лучше всего соответствует вашим потребностям.
Услуги литья пластмасс под давлением (онлайн-предложения)
Формы с множеством полостей (семейные формы)Семейство фасонных деталей
В дополнение к одной пластиковой детали, производимой в цикле формования, пресс-форма также может быть спроектирована для производства нескольких количеств одной и той же детали за один цикл.Инструмент с одним слепком часто называется формой для одного слепка (полости), тогда как специальная форма для литья под давлением с двумя или более полостями одной и той же детали называется формой для нескольких слепков (полостей). Количество оттисков в форме часто ошибочно называют кавитацией. Некоторые пресс-формы очень большого объема, например, для крышек бутылок, могут иметь более 128 полостей.
Форма для множественных слепков (полостей) может также называться «семейной» формой. Тем не менее, семейная пресс-форма более точно определяется как пресс-форма, которая может производить несколько деталей одинакового размера в одинаковом количестве, цвете и материале.Формованные детали семейства часто являются частью сборки, например, сопрягаемой верхней и нижней половинами.
Формование поверхOvermolding — это процесс литья пластмасс под давлением, который очень полезен для производства деталей из нескольких материалов с некоторыми уникальными свойствами. Например, этот процесс можно использовать для добавления второй части из другого материала для ручки или рукоятки. Представьте себе электроинструмент с рукояткой из более мягкого материала, чем корпус инструмента. Точно так же игровой контроллер может быть изготовлен с различной текстурой пластика на его корпусе.
В основном, ранее отформованная под давлением деталь из одного материала (подложка) повторно вставляется в машину для литья под давлением, а другой материал (верхнее формование) впрыскивается для образования нового слоя поверх первой части.
Некоторые специализированные термопластавтоматы имеют два или более узла впрыска, которые могут «формоваться поверх» за один цикл формования. Например, пресс-формы для литья под давлением «с двумя или несколькими выстрелами» сначала формуют основную форму из пластика основного цвета, затем второй материал другого цвета вводится в оставшиеся открытые пространства для получения цельная, разноцветная пластиковая деталь.
Формование поверх друг друга не так просто, как литье под давлением детали из единого материала, и оно имеет свои ограничения. Одно из соображений заключается в том, что два материала должны быть совместимы, химически и термически. Поскольку пластмассовые материалы имеют разные температуры плавления, материал основы должен иметь более высокую температуру плавления, чем материал для формования, иначе исходная деталь расплавится и деформируется при впрыскивании материала для формования.
Формовочная пластинаМеталлические, керамические или пластмассовые детали могут быть вставлены в расплавленный термопласт, чтобы образовать многоматериальные, прочные детали с дополнительной функциональностью.Например, металлические вставки с резьбой могут быть отформованы в детали, чтобы их можно было прикрепить к другим деталям.
Литье со вставкой может снизить стоимость за счет встраивания второстепенных деталей в процесс литья пластмасс под давлением, в отличие от установки деталей после формования. За счет интеграции вставок во время формования детали становятся более прочными по сравнению с размещением деталей при постформовании. Конечно, вставки должны выдерживать высокую температуру и давление процесса литья под давлением.
Литье под пластиной, естественно, является более сложным процессом, чем стандартное литье под давлением, поэтому некоторые компании, занимающиеся литьем под давлением, имеют больший опыт в этом процессе, чем другие. Для небольших производственных циклов оператор станка может вручную загрузить вставки в пресс-форму перед циклом впрыска пластика. Однако для крупносерийного производства обычно используют автоматизированное оборудование для помещения вставок в пресс-форму.
Время цикла формованияПоследовательность событий во время производства называется циклом.Он начинается, когда форма закрывается, и полимер вводится в полость формы. Когда полость заполняется, форма поддерживает удерживающее давление, чтобы учесть усадку материала.
Затем винт поворачивается, и следующий выстрел перемещается в переднюю часть винта. Это заставляет винт реагировать, и после охлаждения форма открывается и пластиковая деталь удаляется.
Формулу можно использовать для определения времени цикла литья под давлением. Время, необходимое для изготовления детали методом литья под давлением, рассчитывается как:
Общее время = 2M + T + C + E
Где:
(2M) = Двойное время открытия / закрытия формы
(T) = Время впрыска (S / F)
(C) = Время охлаждения
(E) = Время выталкивания (E)
(S) = Форма Размер (дюйм3)
(F) = расход (дюйм3 / мин)
Время закрытия формы и выталкивания деталей, полученных литьем под давлением, может составлять от менее секунды до нескольких минут, в зависимости от размера формы и машины.Время охлаждения, которое доминирует в процессе, зависит от максимальной толщины детали.
Эффективность процессаОптимизация процесса литья под давлением очень важна, поскольку она влияет на стоимость, качество и производительность. Некоторые из различных проверок оптимизации включают:
• Оптимизация времени выдержки путем проведения исследований уплотнения затвора или замерзания затвора
• Проведение исследования времени охлаждения для оптимизации времени охлаждения литой детали
• Исследования перепада давления определяют, достаточно ли давления в машине для перемещения винта в наборе скорость
• Построение кривых вязкости для определения скорости впрыска
• Изменяйте температуру расплава и давление выдержки для оптимизации рабочего окна
Когда задание по литью под давлением настраивается впервые и размер порции для этой формы неизвестен, будет проведено испытание литья, чтобы все было «налажено».«Специалист по формам обычно начинает с небольшой порции груза и постепенно заполняет форму, пока она не будет заполнена на 95–99%. Затем прикладывается небольшое удерживающее давление, и время выдержки увеличивается до тех пор, пока не произойдет замерзание затвора (время затвердевания) на отлитой под давлением детали. Затвердевание затвора важно, потому что оно определяет время цикла, а время цикла является решающим фактором эффективности и, следовательно, экономики производственного процесса. Если детали имеют углубления, удерживающее давление будет увеличиваться до тех пор, пока они не будут сведены к минимуму и вес детали не будет достигнут.После того, как настройки установлены и термопластавтомат изготавливал хорошие детали, составляется установочный лист для стандартизации процесса для будущих производственных циклов.
.