Из чего делают автомобильную резину
Условия суровой конкуренции заставляют многих производителей автомобильных покрышек утаивать состав резиновой смеси, используемый для производства автошин. Этапы технологического процесса держатся в строгой секретности. При этом основные составляющие, из которых изготавливается авторезина, известны. Без них невозможно создание покрышек. Давайте разберемся, из чего делают резину.
Натуральные и синтетические составляющие
Как добывается натуральный каучукРезину для автомобилей делают из каучука, который может быть природного либо синтетического происхождения. Натуральный каучук добывают из каучуковых деревьев. Дословно название «каучук» переводится как плачущее дерево. Сок указанного дерева имеет очень большую ценность, из него производится авторезина. Синтетический каучук имеет меньшую себестоимость, его чаще применяют для производства.
Примерно 30% от общего состава резины составляет технический углерод (сажа). Он выступает скрепляющим компонентом, действующим на молекулярном уровне. Сажа увеличивает такие характеристики резины:
- эксплуатационный период;
- прочность изделия;
- износостойкость.
Иногда технический углерод заменяется кремниевой кислотой. Этот компонент используют с целью уменьшения себестоимости продукции. Указанная кислота дешевле сажи. При ее использовании увеличивается сцепление колес с мокрым дорожным покрытием, при этом уменьшается стойкость шин к износу.
При производстве резины, для обеспечения ей определенных свойств домешивают разнообразные масла и смолы. Они уменьшают жесткость покрышек, предназначенных для зимы.
Каждый производитель покрышек применяет особый состав авторезины, делает упор на определенные характеристики покрышек:
- сцепление с дорожной поверхностью;
- устойчивость к абразивным частицам дороги;
- улучшение скоростных характеристик и так далее.
Рекомендуем посмотреть видео о том, из чего делают резину:
youtube.com/embed/arF5fc14hpM?feature=oembed» frameborder=»0″ allowfullscreen=»»/>
Технология производства авторезины
Производство автопокрышекЛетняя резина отличается от зимней авторезины количеством и качеством, входящего в ее состав каучука. Чтоб сделать летние автошины, необходим каучук ненатурального происхождения. Он обеспечивает жесткость автопокрышкам. Натуральное сырье наоборот смягчает резину, поэтому его используют в зимних шинах. Присутствие натурального каучука позволяет зимним покрышкам не «дубеть» при очень низких температурах.
Сок каучуковых деревьев собирают, затем помещают его в большие чаны, наполненные кислотой на 10 и более часов. Такая технология позволяет сырью затвердеть и в результате получается латекс. Из полученного латекса убирают излишнюю влагу и пропускают его через специальные валы, для образования широкой ленты. Указанная лента с помощью специальных ножей измельчается, в итоге получается легкая воздушная масса, которую с помощью обжига в специальных печах преобразуют в эластичные блоки.
Указанные блоки помещают в специальный котел, в который производителем добавляются дополнительные элементы с учетом четких пропорций для придания резине определенных качественных характеристик. Этот «коктейль», состоящий из каучука и химических элементов нагревается и превращается в резину. Разогретую смесь раскатывают специальными валами в полосы определенной толщины, затем охлаждают.
Процесс изготовления автопокрышек
Из чего делаются покрышки? Готовые автопокрышки состоят не только из резины. Каркас автопокрышек изготавливают из специальных нитей. Они могут быть:
- текстильными;
- металлическими;
- полимерными.
Технология производства корда напоминает работу ткацкого станка. Образованный корд помещается в экструдер, в котором осуществляется его обрезинивание. Готовый каркас раскатывается на полосы, имеющие различную ширину для изготовления покрышек разной размерности.
Для создания протекторного слоя обрезиненный корд помещается на специальный станок, превращающий методом экструзии заготовку в протектор.
Борт авторезины изготавливается следующим образом:
- Металлическая проволока обрезинивается.
- Производится нарезка обрезиненной проволоки кругами (с учетом радиуса будущей покрышки).
- На специальном станке проводится сборка боковин.
Для сбора составляющих элементов шин в единую конструкцию применяют специальный станок. На него устанавливают бортовые кольца и катушки с компонентами. Станок автоматически соединяет все части автопокрышки, затем наполняет заготовку воздухом под протектор с брекетом.
Завершающим этапом создания шин есть вулканизация. После обработки покрышки горячим паром под давлением, каучук с всевозможными присадками спекается. Затем с применением специальных форм для пресса наносится протекторный рисунок с разнообразными надписями. Готовая продукция проверяется на соответствие всем необходимым характеристикам.
Заключение
Автомобильная резина состоит, в большинстве случаев, из таких компонентов:
- каучук;
- смолы;
- кремниевая кислота;
- сажа;
- секретные химические элементы, добавляемые в резину для придания ей определенных качеств (мел, глицерин, ацетилированный ланолин и так далее).
От качественных и количественных характеристик указанных компонентов зависит качество готовой продукции. Не стоит поддаваться рекламному воздействию и отдавать предпочтение автошинам, изготовленным с применением новых химических компонентов. Перед покупкой таких покрышек, стоит поинтересоваться, насколько заявленные производителем авторезины параметры соответствуют реальности.
Из чего делают шины?
Любой шинный продукт имеет те или иные свойства в первую очередь благодаря своему составу. Шинный коктейль, пожалуй, самый значительный фактор влияющий на технические характеристики той или иной модели. Изготовители автошин обычно держат в строжайшем секрете состав резиновой смеси своих изделий, это является коммерческой тайной любой компании. Но так или иначе, основные компоненты резины известны всем, как и известно об их химических свойствах, которые отражаются на качестве передвижения.
Главные составляющие материалы, используемые при производстве, влияющие на технические показатели автошины:
- Натуральный каучук.
Компонент добываемый из сока бразильской гевеи. На данный момент используется чаще всего в резиновом составе боковин моделей, гарантирую эластичность и упругость. Таким образом существенно улучшается маневренность. Натуральный каучук обладает белым молочным цветом, поэтому до того как стали использовать синтетический каучук шины обладали белым цветом.
- Искусственный каучук. Главный элемент в шинном коктейле, занимает большую долю резинового состава и непосредственно влияет на ходовые показатели. Натуральный каучук использовался на протяжении львиной часть 20 века, до тех пор пока не был синтезирован искусственный каучук (Бутадиен-стирольный, изопреновый, бутилкаучук и т.д.). От твердости каучуковой смеси зависит показатели износа, сцепления и торможения. То есть основные технические свойства. В зависимости от предназначения резины производители обозначают необходимую жесткость. Например, для высокоскоростных моделей состав используется более жесткий каучук, а для классических дождевых — более мягкий (так как такая резина хорошо сцепляется с мокрой дорогой).
- Технический углерод (ТУ) или сажа. Представленный материал занимает 1/3 состава и, как правило, обозначает для изделия такие характеристики как износоустойчивость и прочность. Также дает изделию характерную цветовую гамму. Технический углерод синтезируют путём деструкции природного газа, то есть, по сути, данный материал является отходом при добыче природного газа. Шины произведенные в СССР включали в себя большую долю сажи, по причине легкодоступности материала. К сожалению данный материал экологически вредный, поэтому с каждым годом производители стараются сократить его долю в своих изделиях.
- Диоксид кремния или силика. Заменой технического углерода являются специфические кремниевые кислоты в различных вариациях. Силика используется, прежде всего, в производстве зимней автошины. Она лучше чем ТУ внедряется в соединения каучука и не вытесняется из смеси подобно саже (черные следы идущие от шины ничто иное как вытесненный из состава технический углерод).
Диоксид кремния обеспечивает резину эластичностью, мягкостью, комфортностью и великолепным сцеплением с мокрой дорогой. Но главным преимуществом кремниевой кислоты является стойкость к низким температурам. Шины с большим содержанием силики обычно характеризуются как экологически чистые.
- Сера. Сера используется как вспомогательный элемент для связи молекул вышеописанных полимеров. Это отражается на целостности, прочности и эластичности шины.
- Натуральные масла или смолы. Смягчающие элементы природного происхождения (например рапсовое масло или канола). Обычно используются в зимних моделях.
- Помимо прочего используется большое количество уникальных натуральных элементов для предоставления тех или иных свойств. Например крахмал кукурузы снижает сопротивление качению, а молотая скорлупа грецкого ореха увеличивает сцепление на заледенелой поверхности.
Резиновая смесь того или иного изделия — залог безопасного передвижения того или иного автотранспорта.
Из чего делают автомобильные шины
11.12.2017, Просмотров: 1208
О производстве автомобильных шин ходит множество легенд и споров. Некоторые думают, что основа для шины составляет нефть, но на сегодня это не так. Первые автомобильные шины были исполнены из 100% природного материала.
Каучук
Каучук является основным компонентом для производства шины. Данный материал добывается при помощи каучукового дерева. Такие деревья растут на просторах Южной Африки, и только в 16 веке в Европе узнали о многовековом существовании дерева.
«Кастилья и Гевея» это основные источники каучука. Когда ломались ветки этих деревьев, то пролитый сок взаимодействовал с воздухом, и получалось тягучее вещество, очень схожее с резиной.
Особенности конструкции
Современная покрышка состоит из природного синтетического каучука и корда. Сам корд может состоять из металлических, текстильных и полимерных нитей. Состав шины:
- каркас;
- множество слоев брекера;
- протектор;
- борт с боковой частью.
Существует два типа шины по ориентации нитей:
- радиальная;
- диагональная.
Радиальная
Радиальный тип покрышки шины имеет нити, которые располагаются вдоль профиля покрышки от борта до борта. Такая конструкция позволяет не растягиваться резине поперек, а брекер, размещенный диагонально, предотвращает продольное перемещение нитей. В данной конструкции напряжение на нити меньше вдвое, чем в диагональной резине. Так же это позволяет наносить меньше слоев корда, что существенно понижает себестоимость шины. Низкая толщина каркаса, из-за меньшей силы трения, позволяет выделять маленькое количество тепло, что благоприятно сказывается на долговечности протектора.
Одним из достоинств радиальной шины является хорошее сцепление с дорогой, предотвращающее качение. Это преимущество значительно сказывается на расходе топлива.
К недостаткам можно отнести жесткое качение, появляющееся на неровной дороге, такое явление присуще низкопрофильной резине. Так же шина уязвима к ударам, порезам и проколам.
Диагональная покрышка
В такой шине каркас корда располагается диагонально под углом 53°. Такая внутренняя конструкция позволяет шине растягиваться вдоль и поперек, это делает шину эластичной. Боковина шины толстая, что позволяет держать низкое давление в покрышке. Диагональные шины крайне редко применяются в современном автомобилестроении, поэтому используются только в старых отечественных грузовых автомобилях, а так же на новой спецтехнике.
Из чего состоит каркас шины
Брекер. Этот элемент располагается между протектором и каркасом. Он служит для того, что бы защитить шину от ударов и придает жесткость на поверхности, контактирующей с дорогой.
Протектор. Он служит для регулировки правильного коэффициента контакта между дорогой и шиной. Протектор имеет разного рода рисунок. Для грунтовых дорог, шоссейных, городских, снежных разный рисунок. Основной задачей протектора обеспечение надежное сцепление с дорогой. К примеру: при дождевой погоде, во избежание эффекта «аквапланирование» протектор должен быстро отводить воду от колеса, благодаря чему шина плотно контактирует с поверхностью дороги, а не воды.
Борт. Благодаря борту обеспечивается надежная посадка шины в колесе.
Производство шины
Над тем, какая будет резина на выходе из производства, решает состав инженеров, который тщательно прорабатывают каждый рисунок на протекторе, отвечающий за свою роль. После того, как шина была смоделирована, наступает этап производства.
Рождается будущая шина в цеху резиносмешения. Здесь готовиться резиновая смесь, из которой сделана покрышка. В основе смеси пласты резины и технический углерод (сажа, смолы и 20 нужных компонентов, которые не рассекречиваются). Ингредиенты будущей шины отправляются в смеситель. Данный процесс напоминает замес теста: битум, каучук, канифоль и сера смешиваются, но рецептура может меняться в зависимости от типа резины по покрытию дороги и времени года.
После смешения пласты резины попадают в сборочный цех, где в первую очередь производят бортовое кольцо, которое придает жесткость и герметичность будущей шине. Бортовое кольцо состоит из проволоки, материалом для этого служит латунь. С большой катушки нити разматываются, протягиваются и собираются в одну стальную ленту. Что бы склеить нити, они проходят через экструдер, где плавится резина и обволакивает проволоку. Затем из ленты, при помощи робота, формируется кольцо.
Следующий слой – брекер. Для укрепления конструкции применяют нейлоновый бандаж. Параллельно изготавливается протектор – слой резины с разноцветными полосами. При помощи нитей разного цвета маркируется модель покрышки. Соседний аппарат готовит не менее важную деталь покрышки – гермослой. Он придает герметичность шине, и служит заменой камере. Поверх слоя наносится текстильный каркас и присоединяется бортовое кольцо, и сверху покрышка.
Вся конструкция под большим давлением сжимается, после чего необходимо загнуть края и придать конструкции форму. Что бы придать конструкции окончательный вид, ее перемещают в большой вулканизатор. Колесо размещается в раскаленную форму, где под температурой 200 градусов и высоким давлением покрышка приобретает конечную форму и рисунок протектора. Во время вулканизации каучук взаимодействует с серой и превращается в готовую резину.
После приготовления шины, вся партия проходит проверку на специальном станке, где проверяется наличие или отсутствие деформации и степень герметичности. Часть шин отправляются на динамические и стендовые испытания в лабораторию. Там резина проходит тесты в экстремальных условиях, где проверятся прочность резины на предмет наезда на острый предмет, прочность бортовых колец, максимальную скорость шины в жестких условиях эксплуатации.
После всех проверок, при условии, что покрышка соответствует всем нормам и мировых стандартам, она отправляется в магазины, после чего служит на дороге.
Как делают шины
Автор admin На чтение 4 мин. Просмотров 120
Многие автовладельцы имеют общее представление о строении автомобильных шин, но о том, как делают шины, мало кто сможет рассказать. Наиболее распространено представление, что резина заливается в некую форму, из которой затем выпрессовывается готовое изделие.
На самом деле это не так, а изготовление автомобильных шин – это сложный высокотехнологичный процесс, для которого необходимо наличие сложного специализированного оборудования, тщательного автоматизированного контроля и участие специалистов высокой квалификации.
Немного истории
Первая резиновая шина была создана в далеком 1846 году Робертом Вильямом Томсоном. На тот момент его изобретением никто не заинтересовался, и повторно к идее пневматической шины вернулись лишь через 40 лет, когда в 1887 году шотландец Джон Данлоп придумал сделать из поливального шланга обручи, надеть их на колеса велосипеда своего сына и накачать их воздухом.
Спустя три года Чарльз Кингстон Уэлтч предложил разделить камеру и покрышку, вставить в края покрышки кольца из проволоки и посадить их на обод, который затем получил углубление к центру. В то же время были предложены рациональные способы монтажа и демонтажа шин, что позволило применять резиновые покрышки на автомобилях.
Процесс производства шин
Из чего делают
Основной материал, который применяется при производстве шин, резина, изготовленная на основе натурального или искусственного каучука. В зависимости от того, в каких пропорциях и какой каучук добавляется, в конечном итоге получаются летние или зимние автомобильные покрышки.
Так, в резиновую смесь для летних шин добавляется преимущественно искусственный каучук, поэтому резина получается более жесткой, устойчивой к износу, она не «плывет» при высокой температуре и обеспечивает надежное сцепление с дорожным полотном. Чтобы изготовить зимние покрышки, добавляют натуральный каучук, который делает резину более мягкой и эластичной. Благодаря этому зимние шины не «дубеют» даже при очень сильных морозах.
- Помимо каучука в резиновую смесь добавляют множество других компонентов, таких как пластификаторы, наполнители, сажа, вулканизирующие добавки.
- Шина состоит из нескольких элементов, объединенных в одно целое: каркаса или корда, слоев брекера, протектора, борта и боковой части.
Как делают каркас
Корд будущей покрышки делают из металлических, текстильных или полимерных нитей на специальном станке – «шпулярнике». От множества катушек проволока нити сходятся в одном месте. В общих чертах конструкция напоминает ткацкий станок. Далее сплетенный корд попадает в экструдер, где происходит его обрезинивание.
Готовый каркас впоследствии раскраивается на полосы разной ширины, для производства шин разной размерности. И сматывается в катушки для хранения и транспортировки. Поскольку невулканизированная резина очень липкая, во избежание порчи каркаса между слоями вставляются прокладки.
Как делают протектор
Следующий этап производства – создание протектора. Лента обрезиненного корда заправляется в станок, который методом экструзии превращает ее в протектор. Чтобы работники могли визуально быстро определить размерность будущей покрышки, на протектор краской делают цветные линии.Боковая часть
Борт покрышки состоит из бортового кольца и слоя вязкой воздухонепроницаемой резины. Производство бортов шин начинается с того, что металлическая проволока обрезинивается, после чего закручивается под требуемый радиус колесного диска и нарезается кругами. После этого на станке осуществляется сборка. Подробнее этот процесс можно посмотреть на видео.
Сборка
Предпоследний этап – сборка готовой покрышки. Осуществляется она на станке, на который поступают все готовые элементы. Обслуживают станок два работника: сборщик и перезарядчик.
Первый навешивает бортовые кольца, а второй вставляет катушки с компонентами. После этого станок все делает автоматически: соединяет части воедино и раздувает заготовку воздухом под протектор с брекером. Почти готовую шину взвешивают и осматривают на предмет наличия дефектов. Этот процесс также можно посмотреть на видео.
Вулканизация
Последний этап производства – вулканизация. Шина обрабатывается горячим паром под давлением 15 бар и при температуре порядка 200 градусов по Цельсию. В результате каучук, сажа и всевозможные присадки спекаются, а на поверхности покрышки при помощи пресс-форм наносится рисунок протектора и надписи. Готовые шины проверяются на соответствие всем требуемым характеристикам.
Что еще стоит почитать
С чего начинается шина | Журнал Популярная Механика
Они должны плакать. Плакать белыми тягучими слезами, раз в пять дней. Иначе мы не сможем ездить.
Круглый предмет падает на землю и магическим образом отскакивает от нее прямо в руки индейцу: команда Колумба зачарована увиденным. Разбитый подагрой американец гладит латекс утюгом, варит, жарит и запекает его на кухне. Его голодная семья с ужасом наблюдает за опытами: ах, если б только латекс был съедобным! Чарльз Гудьир наконец изобретает технологию превращения латекса в более прочный и стабильный материал под названием резина, но счастья ему она не приносит. Он умирает больным, нищим и безвестным. Англичанин Генри Уикхэм тайком вывозит тысячи семян гевеи из Бразилии. Гевею высаживают в британских колониях на Малайском полуострове, и через какое-то время крупнейшая южноамериканская страна превращается из монополиста латекса в его импортера! Это лишь несколько эпизодов из жизни латекса, материала с невероятно захватывающей историей…
Микроциклус, злой и ужасный
Несколько месяцев назад «Популярная механика» решила выяснить, из чего делают автомобильные шины, и так увлеклась расследованием, что несколько дней провела в бразильском штате Байя, на каучуковых плантациях.
Направлявшиеся на Токийский автосалон автомобильные журналисты, с которыми мы встретились в аэропорту «Шереметьево-2», могли бы удивиться, что мы с ними летим в разные концы света. Ведь сегодня практически 95% натуральной резины производится в Юго-Восточной Азии, главным образом в Индонезии, Таиланде и Малайзии. Туда обычно и отправляются все желающие узнать, как «выращивают шины». На родине же этого материала, в Бразилии, сегодня производится менее 1% латекса в мире! И все же в штат Байя мы отправлялись не случайно: только здесь и еще в Париже находится лаборатория по изучению гриба Microcyclus ulei. По вине этого паразита мир в скором будущем может остаться без натуральной резины!
Если бы не микроциклус, Бразилии сегодня не приходилось бы закупать за рубежом более 100 000 т латекса. Нынешние объемы производства этого материала в стране покрывают лишь 40% национального спроса. Проблема в том, что местный микроскопический грибок с остервенением набрасывается на листья гевеи, поражает их, а деревья, тратя все свои силы на восстановление листьев, больше не способны производить латекс. Настоящим провалом обернулся проект Fordlandia, инициированный в 1920-х годах Генри Фордом. Чтобы не закупать латекс у англичан, изобретатель конвейера открыл огромную каучуковую плантацию недалеко от Амазонки в Бразилии, но из-за поражения растений грибком и ряда организационных просчетов американская компания понесла огромные убытки и в конце концов решила избавиться от плантации. Беда не обошла стороной и одну из самых крупных шинных компаний в мире — Michelin. Плантация, на которой мы находимся, была куплена французской компанией в 1984 году у терпевшей огромные убытки американской фирмы Fire-stone (ныне подразделение Bridge-stone). Сделка оказалась крайне неудачной для французов. Выяснилось, что многие деревья на плантации поражены микроциклусом. Химические способы борьбы дороги и малоэффективны: над плантацией должны были постоянно кружить самолеты с химикатами, и все равно таким образом грибок не уничтожить. К тому же цены на натуральную резину на международном рынке резко упали.
На бразильских плантациях
От индейской игры пок-та-пок до гигантской шинной индустрии современности, резина вот уже три тысячелетия присутствует в жизни человечества.
1600 лет до нашей эры. Обитатели Мезоамерики, историко-культурного региона, простирающегося от центра Мексики до Никарагуа, начинают играть в пок-та-пок. Мяч для этой древнейшей командной игры, похожей на баскетбол с элементами волейбола, делали из белого сока растения Castilla elastica. Чтобы латекс затвердел и стал прыгучим, индейцы смешивали его с соком лозы Ipomoea alba. В течение 10 минут полученный раствор затвердевал и приобретал свойства, присущие резине. Это был древней аналог вулканизации, придуманной три тысячелетия спустя Чарльзом Гудьиром. Индейцы также использовали латекс для изготовления непромокаемых тканей, обуви и емкостей для хранения воды и продуктов.
1452 год. Колумб открывает Америку и знакомится с прыгающими мячиками из латекса. О них Колумб упоминает как о забавной диковинке, не придавая ей какого-то значения. В результате последующие три столетия европейцы даже не задумываются о том, что резина — стоящий материал.
1731 год. Французский географ Шарль Кондамин во время путешествия в Южную Америку открывает для себя латекс и, впечатленный свойствами этого материала, привозит его в Европу. Латексом наконец-то заинтересовываются ученые и коммерсанты. В 1770 году англичанин Джозеф Пристли представляет миру каучуковый ластик, затем латексом начинают пропитывать ткань. Первым крупным производителем непромокаемых плащей становится английский химик Чарльз Макинтош — вскоре его фамилия становится нарицательной.
1839 год. Люди в галошах и макинтошах больше не боятся дождливой погоды, но теперь их страшат перепады температуры. В холодные дни их одежда становится ломкой, а в жару размягчается, превращаясь в липкую массу. Кроме того, от нее исходит неприятный запах. Химики проводят бесчисленные эксперименты, пытаясь сделать латекс более стабильным. В результате процесс вулканизации каучука совершенно случайно открыл Чарльз Гудьир. Выяснилось, что при нагревании с серой латекс теряет липкость и ломкость.
1876 год. Англичанин Генри Уикхэм тайком вывозит из Бразилии, поставлявшей каучук всей Европе, партию семян гевеи. Растения высаживают в британских колониях на Малайском полуострове. Дерево отлично прижилось и спустя годы именно эти места стали основным местом добычи каучука, тогда как природные запасы каучука в Бразилии постепенно истощились.
1901 год. Русский ученый Кондаков синтезирует каучук из бутадиена. В России эта технология применения не нашла, но на основе ее немцы разработали свою технологию производства шин для армейских машин.
Конец 1920-х годов. В России и Германии разрабатывают метод создания недорогой и неплохой резины. Спустя 15 лет в США синтезируют неопрен, который по ряду качеств превосходит натуральную резину.
Конец XX века. За счет применения в составе шин кремнезема удалось снизить коэффициент сопротивления качения на 30%, уменьшив расход топлива автомобиля примерно на 6−9%.
Война объявлена
Руководству Michelin надо было незамедлительно принимать решение. Можно было, например, наладить на плантации производство других культур, но шинная компания не видела смысла заниматься новым для себя бизнесом. Другой альтернативой была продажа земли, но тогда бы пришлось уволить всех работников плантации. Движимые идеями социальной ответственности топ-менеджеры Michelin решили сохранить рабочие места. Компания пошла на беспрецедентный ход: была объявлена полномасштабная война с микроциклусом. Совместно с французским научным центром CIRAD компания занялась длительными исследованиями, чтобы найти эффективные методы борьбы с грибком.
Чего боятся в Азии
Первоначально ученые хотели вывести растения, полностью невосприимчивые к заболеванию, но выяснилось, что грибок легко мутирует, а значит, через некоторое время появятся новые виды паразита, которые будут уничтожать и «защищенные» сорта гевеи. Выходом из ситуации стало выведение сортов, которые страдают от грибка, но в минимальной мере: заболевание практически не сказывается на урожае. После двух десятилетий научной работы было выведено 14 сортов высокопроизводительной гевеи, устойчивой к грибу-паразиту. Впервые в истории человек нашел эффективный способ борьбы с паразитом каучукового дерева!
Поскольку микроциклус поражает только листья гевеи и водится только в Южной Америке, где латекса производится сравнительно немного, победа ученых может показаться незначительной. Однако специалисты утверждают, что появление микроциклуса в Азии — всего лишь вопрос времени. Если это случится, то всей авиации азиатских стран не хватит для борьбы с ним химическими средствами, и миру придется на некоторое время остаться без натуральной резины. Десять миллионов человек, работающих в отрасли, рискуют потерять работу. И только высадкой устойчивых к грибку растений можно спасти ситуацию.
Любопытно, что слово «каучук», которое в России часто используют для обозначения натуральной резины или застывшего сока гевеи, в других языках относится только к дереву. Вас поймут, если вы скажете по‑английски или по‑португальски «каучуковое дерево» или «каучуковая плантация», но не поймут, что вы имеете в виду, если скажете просто «каучук». Правильней всего называть застывший сок растения гевеи латексом. С помощью вулканизации, технологии, изобретенной Чарльзом Гудьиром, латекс превращают в натуральную резину — более прочный и устойчивый к воздействиям температуры материал.
Фабрика слез
Перед нами высокие деревья, рассаженные в определенном порядке. Раз в пять дней специально обученный человек надрезает дерево на уровне груди, и с него, как молоко, стекает сок растения в подвешенный ниже горшочек. Когда с дерева стекал сок, индейцам казалось, что оно плачет. Поэтому они стали называть это растение «плачущим деревом» — от индейских слов кау («дерево») и учу («плакать»).
Ни в коем случае не стоит поддаваться искушению попробовать сок гевеи на вкус. Дело в том, что при взаимодействии с кислородом воздуха сок превращается в эластичную твердую массу. Так что выпить сока просто не удастся: получится лишь покушать резину.
Сколько «шин» вырастает на одной гевее? Ответ зависит от того, какие колеса мы имеем в виду. Если легковые, то ежегодного урожая одной гевеи (а это около 5 кг латекса) может хватить на несколько десятков шин. Если же брать грузовые, то для производства одного колеса может потребоваться несколько деревьев. И дело тут вовсе не в том, что шины для коммерческого транспорта больше и тяжелее. Достоинство натурального материала, в отличие от синтетики, — его высокая ходимость и способность выдерживать серьезные вертикальные нагрузки. Это как раз то, что нужно грузовикам! Поэтому некоторые шины грузовиков и автобусов могут состоять на 85% из натурального каучука, хотя обычно в них содержится 30−40% этого материала. В шинах легковых автомобилей натуральной резины всего 15−20%: ресурс шин для обычных машин не самая важная характеристика.
В авиационных шинах низкая истираемость и способность выдерживать высокие нагрузки — самые главные характеристики. Поэтому их делают исключительно из натуральной резины. В случае с шинами для «Формулы-1» срок службы мало кого волнует, куда важнее коэффициент сцепления колеса с дорожным полотном, поэтому эти колеса состоят только из синтетической резины. По крайней мере так предполагает директор нашей плантации Жерар Бокё, давний сотрудник компании Michelin. Информация о составе «формульных» шин, разумеется, держится в секрете, но до недавнего времени болиды «Формулы-1» ездили как на покрышках Bridgestone (нынешний монополист), так и Michelin. Так что можно полагать, что наш хозяин владеет «инсайдерской» информацией.
Жерар Бокё — интересный собеседник. Выращиванием латекса он занимается около 30 лет и не понаслышке знает, что происходит в этой области. Оказывается, за последние десятилетия благодаря научным исследованиям производительность некоторых плантаций возросла примерно втрое!
Но все равно эти успехи не останавливают роста суммарной площади каучуковых плантаций в мире. С каждым годом мировая потребность в резине увеличивается примерно на 3%. Примерно 40% всей производимой резины — натуральная, так что каучуковых деревьев в мире становится все больше. Параллельно строятся новые заводы по производству искусственной резины. «Кстати, вы знаете, что СССР была первой в мире страной, начавшей крупномасштабное производство искусственной резины?» — интересуется у русской группы Жерар. Конечно! Правда, стоит признать, что первыми искусственную резину открыли все-таки немцы. Им пришлось это сделать.
Лист гевеи, пораженный микроциклусом.
Как прожить без гевеи?
Если бы ночью во время Первой мировой в лагерь австро-немецких войск проник лазутчик, то его внимание несомненно привлекли бы армейские грузовики противника. Точнее, способ их стоянки. Практически все они были поддомкрачены и «спали» с вывешенными колесами. Необычное зрелище объяснялось просто: впервые в истории в массовом порядке немецкие военные «обули» свои машины в шины из синтетического каучука.
Когда началась Первая мировая, Великобритания устроила каучуковую блокаду Германии, так что немецким военным ничего не оставалось, как ездить на истершихся покрышках. Разумеется, это сильно нервировало немецкое командование, поэтому генералы вскоре вспомнили, что всего за несколько лет до войны кайзеру Вильгельму II был
Как производят шины для машины
Фотоэкскурсия по знаменитому Ярославскому шинному заводу, одному из крупнейших шинных заводов центрального региона России. Репортаж из цехов, где производят и тестируют шины марки «Cordiant» для легковых автомобилей.
Я и до этого знал, что шина — предмет не простой. Оказалось, что производство еще сложнее, чем я представлял. И самое главное, я узнал секрет, откуда берутся усики на новой резине и зачем они нужны!
1. Немного истории:
Не многие знают, что давным давно шины были деревянными или металлическими (так мне рассказывали в институте). Первая в мире резиновая шина была сделана Робертом Уильямом Томсоном в 1846 году, однако автором пневматической шины считают шотландца Джона Данлопа, который в 1887 году придумал надеть на колесо трехколесного велосипеда своего 10-летнего сына широкие обручи, сделанные из шланга для поливки сада, и надуть их воздухом. Именно с велосипедов и началась эра пневматических шин.
2. Основными материалами для производства шин являются резина, которая изготавливается из натуральных и синтетических каучуков и корд.
Производство шины начинается с приготовления резиновых смесей, которые могут включать в себя до 10 химикатов, начиная от серы и углерода и заканчивая каучуком. Из смесей на специальных станках методом экструзии делают различные заготовки для будущей шины.
3. Так, например, выглядит будущий корд на конвейере.
4. На отбракованном участке заготовки можно увидеть «скелет шины» — каркас, который изготавливается из высокопрочного металлокорда. Многие недалекие автовладельцы считают, что шину пора выкидывать только тогда, когда она стирается до корда.
5. На станках изготавливаются компоненты для сборки. Процесс экструзии для большинства изделий схож, и компоненты выглядят примерно одинаково — на выходе из станка получается длинная резиновая лента.
6. Резина до вулканизации очень липкая, поэтому материал наматывают в бобины прокладывая каждый виток защитным слоем.
7. Все компоненты сортируют по типоразмеру шины, на каждую бобину приклеивают штрих-код, чтобы можно было в любой момент понять для какого типа шин изготовлен материал.
8. Станки с гигантскими катушками изготавливают бортовые кольца. Бортовое кольцо — важный элемент шины, который изготавливается из множества витков обрезиненной бортовой проволоки. Это нерастяжимая, жесткая часть шины, с помощью которой происходит фиксация на ободе диска.
9. Много-много нитей сплетаются в ряды, которые далее обрезиниваются.
10. Этот станок закругляет обрезиненную проволоку в кольцо под необходимый посадочный размер диска. Слева в кадре — ленты проволоки, справа — готовые кольца.
11. Готовые бортовые кольца.
12. На сборочных станках все детали шины соединяются в единое целое. Необходимые компоненты с бобин загружаются на ленты конвейера.
13. Так выглядит протекторная заготовка. До вулканизации это просто толстая полоса резины без рисунка протектора. Цветные линии — специальная кодировка, чтобы можно было быстро и четко понять, какой у шины радиус, ширина и высота профиля и т.д. (своеобразный штрих-код шины).
14. Бабина с заготовкой раскручивается, компонент уходит на конвейер, а защитный слой, (коричневая лента, чтобы материал не слипался) наматывается на другую катушку.
15. Дальше начинается этап «Слава роботам!». Все происходит очень быстро и далеко не сразу можно разобраться, что к чему. На сборочный барабан последовательно накладываются слои с разных лент конвейера.
Увеличить изображение
16. Потом приезжает большой робот и ловко раздувает заготовку воздухом, что-то сминает, сжимает и заворачивает и получается полуфабрикат шины.
Увеличить изображение
17. По конвейерным линиям заготовки отправляются в цех вулканизации.
18.
19. Здесь шина подвергается термовоздействию горячим паром под высоким давлением. Каучук, техуглерод и присадки «спекаются» в единое целое, а на внешние и внутренние поверхности шины с помощью пресс-форм наносятся рисунок протектора, надписи и другие технические профили.
20. В цеху целые ряды установок вулканизации с прессформами для различных типов шин.
21. Слева идет процесс вулканизации, а справа пустая камера с диафрагмой, которая раздувает шину под высоким давлением.
22. Заготовка в камере, сверху видны прессформы. Под давлением по боковинам и протектору прорисовывается рельефный рисунок. Происходит химическая реакция (вулканизация), которая придает резине эластичность и прочность.
23. Так выглядит разобранная прессформа. Со временем от высокой температуры и давления прессформа загрязняется и ее следует очищать.
24. Прежде всего забиваются каналы для отвода воздуха при вулканизации. Именно из-за этих каналов и образуются те загадочные «усики» на новых шинах.
25. Прессформы для боковин.
26. Цех, где очищают загрязнившиеся прессформы.
27. Историческая справка:
В июне 1943 г. в результате налета немецкой авиации, завод был полностью разрушен. Но уже в конце сентября последствия бомбардировки были ликвидированы, завод восстановлен.
1950-е гг. Впервые в СССР завод начал выпускать бескамерные шины: для легковых автомобилей «Победа», «Волга», «ЗИМ».
Конец 50-х. Страна переживала «шинный кризис», увеличивался простой автотранспорта из-за дефицита шин.
1966 г. Выпущена 100-миллионная шина.
1969 г. ЯШЗ первому из отечественных заводов было дано право выпускать шины для нового легкового автомобиля «Жигули».
28. Внутри установок по вулканизации безумно красиво!
29. Вот где нужно было снимать Терминатора.
30.
31.
32. Готовые шины поступают на общий конвейер и отправляются на окончательный контроль качества шин перед отправкой потребителям.
33.
34. На контроле производится визуальный осмотр шин.
35. Дальше в работу снова включается робот, который проверят динамические характеристики каждой шины.
36. Все новые модели обязательно проходят стендовые и лабораторно-дорожные испытания в заводском опытно-испытательном центре, которые ведутся на специальных станках, где моделируются условия эксплуатации, в несколько раз превышающие по воздействию дорожные.
37. Диски под все типы шин.
38. А так выглядит стенд для испытания сразу шести шин одновременно.
39. А это — авиационные шины. Как их производят — большой секрет! На предприятиях компании «СИБУР – Русские шины», выпускающих шины марки Cordiant производится не только продукция для широкого круга потребителей, но и специальные изделия, например шины для истребителя 5-го поколения, известного как Т-50, или ПАК-ФА.
40. Чтобы посмотреть на производство авиационных шин нужно получать разрешение в ФСБ.
41. В этом цехе установлены стенды, где имитируют скорости и нагрузки на колесо при взлете и посадке самолета.
42.
43. Вот так производятся шины Cordiant.
«Современное сборочное оборудование — это полностью автоматизированное производство, в рамках которого человеку отводится лишь минимальная роль. Автоматизация производства уменьшает влияние человеческого фактора на качество шин, что приводит к значительному улучшению эксплуатационных характеристик конечного продукта. »
Большое спасибо Павлу Кукушкину, Кремневу Юрию и Герастовскому Александру за организацию съемки!
Взят в Как производят шины для машины.
Как работают шины | HowStuffWorks
Вы, возможно, задавались вопросом, как автомобильная шина с давлением в 30 фунтов на квадратный дюйм (psi) может выдержать автомобиль. Это интересный вопрос, и он связан с несколькими другими проблемами, например, с какой силой нужно толкать шину по дороге и почему шины нагреваются во время движения (и как это может привести к проблемам).
В следующий раз, когда вы сядете в машину, внимательно посмотрите на шины. Вы заметите, что они не совсем круглые.На дне есть ровное место, где шина встречается с дорогой. Это плоское пятно называется пятно контакта , как показано здесь.
Если вы смотрите на машину через стеклянную дорогу, вы можете измерить размер пятна контакта. Вы также можете довольно точно оценить вес вашего автомобиля, если вы измерили площадь пятен контакта каждой шины, сложили их вместе, а затем умножили полученную сумму на давление в шинах.
Так как в шине существует определенное давление на квадратный дюйм, скажем, 30 фунтов на квадратный дюйм, вам понадобится довольно много квадратных дюймов пятна контакта, чтобы выдержать вес автомобиля.Если вы добавите больше веса или уменьшите давление, вам понадобится еще больше квадратных дюймов пятна контакта, чтобы плоское пятно стало больше.
Правильно накачанная шина и недостаточно накачанная или перегруженная шина
Вы можете видеть, что недостаточно накачанная / перегруженная шина меньше круглой, чем правильно накачанная, правильно нагруженная шина. Когда шина вращается, пятно контакта должно перемещаться вокруг шины, чтобы оставаться в контакте с дорогой. В том месте, где шина встречается с дорогой, резина выгнута.Чтобы согнуть эту шину, требуется сила, и чем больше она должна гнуться, тем больше усилий требуется. Шина не является идеально эластичной, поэтому, когда она возвращается к своей исходной форме, она не возвращает всю силу, необходимую для ее изгиба. Часть этой силы преобразуется в тепло в шине за счет трения и работы по изгибу всей резины и стали в шине. Поскольку недостаточно накачанная или перегруженная шина должна больше гнуться, требуется больше усилий, чтобы толкать ее по дороге, поэтому она выделяет больше тепла.
Производители шин иногда публикуют коэффициент трения качения (CRF) для своих шин.Вы можете использовать это число, чтобы вычислить, сколько силы требуется, чтобы толкнуть шину по дороге. CRF не имеет ничего общего с тяговым усилием шины; он используется для расчета величины лобового сопротивления или сопротивления качению, вызываемого шинами. CRF такой же, как и любой другой коэффициент трения: сила, необходимая для преодоления трения, равна CRF, умноженному на вес шины. В этой таблице перечислены типичные CRF для нескольких различных типов колес.
Тип шины | Коэффициент трения качения |
Легковая шина с низким сопротивлением качению | 0.![]() |
Обычная автомобильная шина | 0,015 |
Грузовая шина | 0,006 — 0,01 |
Колесо поезда | 0,001 |
Давайте выясним, с какой силой типичный автомобиль может толкать шины по дороге. Допустим, наша машина весит 4 000 фунтов (1814,369 кг), а коэффициент CRF шин равен 0.015. Сила равна 4000 x 0,015, что составляет 60 фунтов (27,215 кг). А теперь давайте разберемся, сколько это мощности. Если вы читали статью HowStuffWorks Как работают сила, крутящий момент, мощность и энергия, вы знаете, что мощность равна силе, умноженной на скорость. Таким образом, количество мощности, используемой шинами, зависит от скорости движения автомобиля. На скорости 75 миль в час (120,7 км / ч) шины используют 12 лошадиных сил, а на скорости 55 миль в час (88,513 км / ч) они используют 8,8 лошадиных сил. Вся эта сила превращается в тепло. Большая его часть попадает в шины, но часть уходит на дорогу (фактически дорога немного изгибается, когда по ней проезжает машина).
Из этих расчетов вы можете видеть, что три фактора, которые влияют на то, сколько силы требуется, чтобы толкнуть шину по дороге (и, следовательно, сколько тепла накапливается в шинах), — это вес шин, скорость, которую вы едете, и CRF (которая увеличивается при понижении давления).
Если вы едете по более мягким поверхностям, например по песку, больше тепла уходит в землю, а меньше — в шины, но CRF возрастает.
Объявление
To The Point — диски и шины UST
Выпущенный Mavic, Michelin и Hutchinson в 1999 году, бескамерный обод и система шин UST уже много лет используются гонщиками Кубка мира и гонщиками выходного дня, но эта тема все еще остается одной может вызвать головокружение даже у самых технически подкованных байкеров.Это усугубляется большим количеством «совместимых с бескамерными» покрышками и ободами, которые, хотя и не имеют сертификата UST, также могут работать достаточно хорошо.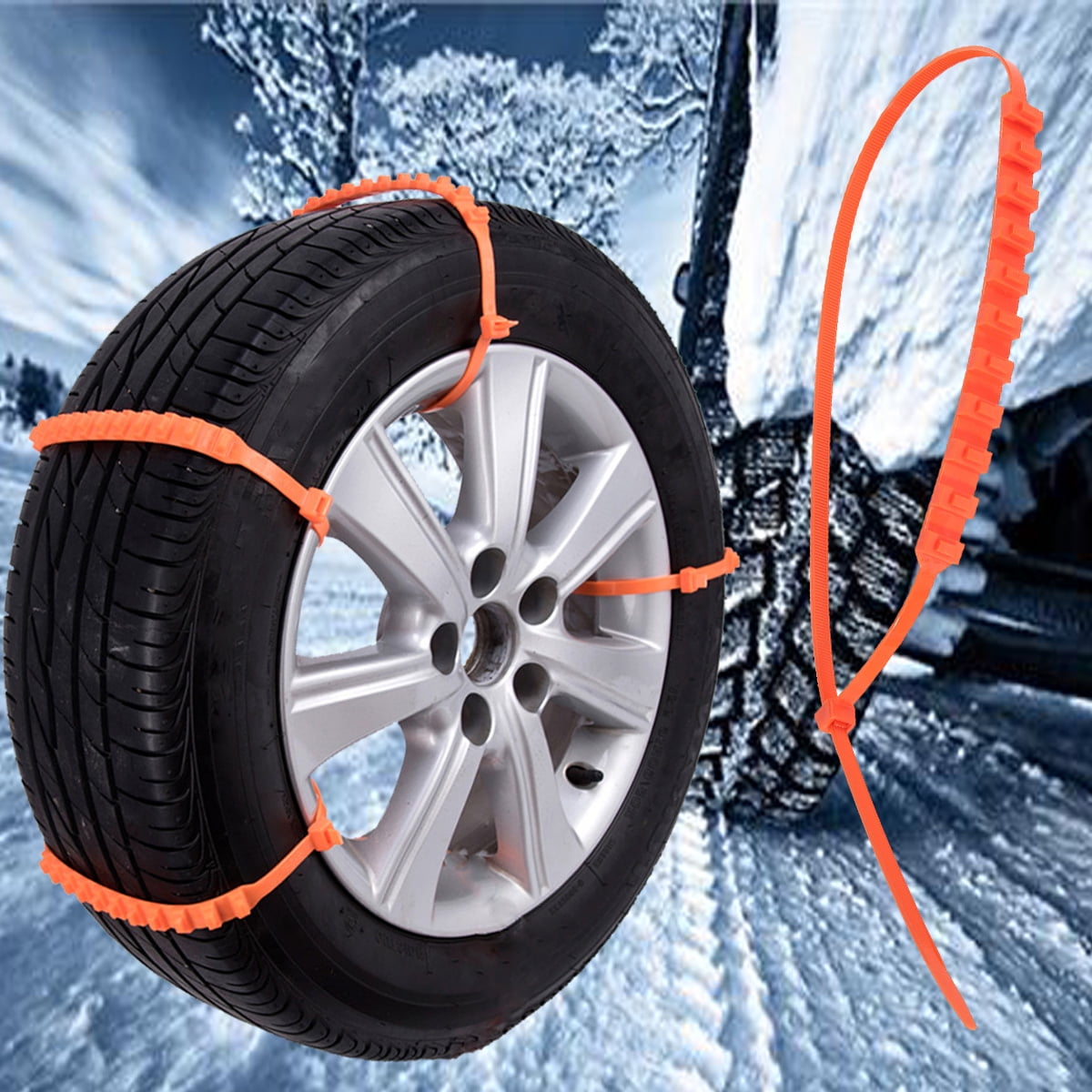
Что означает UST и что это такое?
UST расшифровывается как Universal Standard Tubeless и относится к очень специфической системе, состоящей из двух частей, состоящей из обода и шины.Система UST была разработана и внедрена
в 1999 году в рамках партнерства между Mavic, Michelin и Hutchinson. Что касается обода,
Mavic внесла свой вклад в технические разработки в отношении формы обода и обеспечения герметичности станины шины
. Что касается шин, Мишлен и Хатчинсон разработали шины с воздухонепроницаемым каркасом
и бортом, который фиксировался бы на ободе, подобно бескамерной автомобильной или мотоциклетной шине.
Существует очень специфическая форма и размер крюка для борта обода UST ( — внутренний край
с выступом или крюк боковой стенки обода, который фиксируется бортом шины ), при этом
имеет квадратную форму, а не закругленный профиль стандартный обод. Кроме того, на краю обода
имеется «горб», который помогает зафиксировать борт шины на месте. Размеры крючка для бус
, включая его высоту, диаметр, а также ширину и форму «горба», контролируются
очень тщательно. Последним признаком обода UST является то, что он должен быть воздухонепроницаемым, что означает
, что любые отверстия для спиц должны быть полностью заклеены лентой или пластиком, или основание обода
должно быть неповрежденным и не просверлено вообще. Форма обода UST (, в частности, форма крючка для борта
и выступ ) запатентована Mavic, и Mavic за определенную плату предоставляет эту форму другим компаниям
.Независимая лаборатория дает техническое разрешение на использование любых продуктов
других компаний с логотипом UST.
А что отличает шину UST?
Со стороны шины шина UST должна иметь бортик, имеющий форму, соответствующую форме крюка бортаUST — он больше квадратный, чем круглый, и у него есть небольшой клапан на внутреннем крае
, чтобы помочь создать герметичное уплотнение.

обода, когда она впервые накачивается. Размер и механические характеристики надлежащего борта шины UST
имеют решающее значение.Любое отклонение диаметра или профиля, или растяжение борта
под давлением накачивания может привести к неправильной установке шины и, следовательно, к нарушению герметичности
. Наконец, надлежащий каркас шины UST герметичен и удерживает воздух с течением времени. Опять же, независимая лаборатория
удостоверяет правильные размеры борта, допустимое растяжение борта, герметизирующую способность
, безопасность замка борта даже при спускании воздуха и способность удерживать воздух в течение
раз. Однако компании, которая хочет производить шины UST, не нужно платить лицензионный сбор
.Ему просто нужно сделать шину такой, чтобы она прошла сертификационные испытания.
Обратите внимание, что на стороне шин системы «UST-ready» встречаются повсеместно. Шина, подготовленная к UST, имеет надлежащий борт, сертифицированный по стандарту
UST, но для герметичности каркаса требуется герметик. Несколько марок шин
прошли сертификацию UST с использованием герметика. Конечно, в эту категорию попадают новые шины
Mavic Charge, Roam и Roam XL, как и шины TCS от WTB.
Особенностью номер один в системе UST является интерфейс с крючком.Точный допуск между ободом и бортом шины, а также особая квадратная форма помогают борту шины надежно фиксироваться на ободе. Кроме того, борт шины контролируется на предмет того, насколько он может растянуться при накачивании, что очень мало или совсем нет. Эти характеристики создают очень безопасный и надежный замок для борта. Шина имеет тенденцию оставаться на месте даже в спущенном состоянии. Кроме того, шина может работать при разном давлении, не опасаясь того, что шина взорвется или скатится с обода. Конечно, клапан также является важным компонентом системы — он должен быть правильно установлен на ободе для обеспечения герметичного уплотнения.
Работают ли шины без UST на ободах UST и наоборот? Шины
Non-UST будут работать с ободами UST, но у них нет защиты борта, надежно фиксирующейся в канале обода ( крючки для борта, ).

формы борта вызовет проблемы с удержанием воздуха. Борт шины не очень хорошо прилегает к ободу
. Наконец, шины без UST не так строго контролируются в отношении диаметра и растяжения борта шины
, а это означает, что шина с неплотным креплением может быть более склонна к скатыванию
с обода или разрыву с него под высоким внутренним давлением.
Человек имел бы больший успех, установив шину UST на обод без UST, но опять же, отсутствие точности
между бортом шины и крюком борта обода может вызвать проблемы с уплотнением.
И обод без UST не имеет герметичного станины шины. Кроме того, вам нужно будет найти способ закрыть
отверстия для спиц на станине обода, прежде чем вы сможете установить его бескамерным.
Системы от Stans и другие бескамерные переделки действительно работают, поскольку они позволяют
создать в основном герметичное соединение шины и обода.Но в этих системах нет такого надежного бортового замка (
) между шиной и ободом. Это может привести к непостоянной или, в худшем случае, небезопасной защите обода шины
. Конечно, все это выглядит как продвижение запатентованной системы Mavic, но
другие производители ободов и шин четко протестировали и увидели преимущества надлежащей сертификации
UST. Я разговаривал с менеджером по продукции шин в WTB, который очень откровенно рассказал
о небезопасных условиях, которые они обнаружили в некоторых «бескамерных» системах, и поэтому они создали свои диски и шины
с надлежащей сертификацией UST.То же самое и с другими брендами, такими как Easton
и ENVE.
Каковы преимущества использования установки UST по сравнению с переоборудованием с использованием герметика и ободной ленты, особенно с учетом того, что переоборудованные устройства часто весят меньше?
У правильного СТЮ есть несколько преимуществ. Во-первых, безопасность
при правильно подобранной шине и ободе непревзойденна. Блокирующий борт шины и крюк
борта обода имеют большое значение. Герметичные диски UST не имеют потери веса по сравнению с ободами без UST.Со стороны шины
шины UST-ready имеют такой же вес, как и другие шины, но у них есть бортик, который надежно фиксирует
в крюке борта обода. Что касается надувания, надувать правильно подобранную систему
должно быть так же легко, как надуть систему преобразования. Правда, иногда системы преобразования
увеличивают внешний диаметр станины обода и плотнее прижимают борт шины к ободу
для облегчения накачивания, но такое же состояние может быть создано с шиной UST и ободом, используя рычаг шины
для вытягивания. борт шины частично на «бугорке» в станине обода СТЮ.Это мгновенно создает уплотнение
и облегчает накачивание шины UST с помощью обычного ручного насоса.
www.mavic.com
Почему автомобили так важны и почему вы должны инвестировать в них
В этом быстро меняющемся мире управление личной и профессиональной жизнью может быть действительно беспокойным. Если у вас нет личного транспорта, жизнь может стать еще более беспокойной. Чтобы облегчить себе жизнь, вы всегда должны найти более простой и надежный способ передвижения.Продолжайте читать, чтобы узнать, почему автомобили важны и почему вы должны инвестировать в них с умом.
Дорожное движение
Одна из основных причин, по которой автомобили стали более распространенными и важными, заключается в том, что это легкий вид транспорта. Добраться из точки А в точку Б еще никогда не было удобнее и проще. Вам больше не нужно полагаться на общественный транспорт для ежедневных поездок на работу, и вы можете наслаждаться свободой и независимостью, которые дает автомобиль.
В этом сообщении в блоге вы узнаете больше о важности автомобилей, их преимуществах и нескольких веских причинах, почему вам также стоит инвестировать в них.
Важность транспортных средств
Это как свойство
Покупка автомобиля, пожалуй, одна из самых больших инвестиций, которые вы когда-либо сделаете, после покупки дома. Следовательно, ваш автомобиль — это не просто средство передвижения, это как собственность. В случае необходимости вы можете продать его за более дешевую модель и потратить деньги на что-нибудь полезное. В случае успеха вы можете обменять его на что-то с еще лучшими функциями, преимуществами и внешним видом.
Люди проводят большую часть времени в автомобилях
Даже после покупки автомобиля люди проводят много времени в машине во время поездок на работу.Поэтому, если у вас нет машины, как вы сможете убить время? По крайней мере, когда у вас есть автомобиль, вы можете слушать музыку или разговаривать с другом. Если у вас есть дети, они будут вам благодарны за развлечения, предлагаемые вашей машиной.
На общественный транспорт нельзя положиться
Сесть на автобус утром только для того, чтобы узнать, что он уже заполнен или уехал, может быть очень неприятным занятием. Кроме того, если автобус опаздывает и вам нужно куда-то быстро добраться, даже несколько секунд могут показаться дольше обычного.
Следовательно, вы не можете просто полагаться на общественный транспорт для ежедневных поездок. Вот почему очень важно иметь собственный личный автомобиль; он помогает добраться до места назначения, не полагаясь на других людей.
Это не просто способ добраться из точки A в точку B
В то время как многие люди относятся к своим машинам как к чему-то полезному, на самом деле это не так. Вождение по открытым дорогам может быть очень интересным. Не говоря уже о том, что, путешествуя по некоторым маршрутам, вы можете наслаждаться красотой матери-природы, такой как леса, океан, реки, озера, пустыни, леса, горы и холмы.Проще говоря, ваша машина может отправиться в приключение, которое иногда невозможно при ходьбе. Таким образом, автомобили — это выгодное вложение — больше, чем просто доставка из пункта А в пункт Б.
причин инвестировать в автомобиль
Удобство и независимость
Для молодых людей, закончивших колледж и университет, жизнь без личного транспорта может быть неприятной. Это одна из основных причин, по которой вы должны инвестировать в автомобиль. Это обеспечивает максимальное удобство и может помочь вам сделать первый шаг к независимости.
Вам не придется зависеть от членов вашей семьи или общественного транспорта, вы сможете без проблем добраться до колледжа.
Экономьте время — Спасайте разум
Поездка детей в школу на общественном транспорте может быть очень стрессовой и отнимать много времени. Вы должны постоянно помнить время, чтобы не пропустить автобус. Кроме того, даже если вы все-таки сядете на автобус, остановки, сделанные по дороге, гарантируют, что вам предстоит долгое путешествие. Однако, если у вас есть машина, вы можете облегчить бремя и стресс, бросив ее самостоятельно.
Удобные покупки и транспортировка тяжелых предметов
Это начало нового месяца, и вам снова нужно отправиться за ежемесячными продуктами. Но единственное, что расстраивает, — это таскать эти тяжелые сумки пешком или в автобусе. Вам не придется испытывать эти хлопоты, если вы приобретете автомобиль. В автомобилях есть багажник, в котором достаточно места для перевозки большого количества покупок и тяжелых материалов.
Подходит для ежедневных поездок и коротких поручений
Если в вашем доме живет пожилой человек, неразумно пользоваться общественным транспортом для коротких поручений.Вместо этого вы можете просто завести машину и отправиться в ближайший магазин независимо от того, сколько раз вы хотите, не беспокоясь о вызове такси или сборе на автобус.
Таким образом, автомобиль, как правило, является лучшим выбором для ежедневных поездок на работу, позволяя выполнять больше поручений по сравнению с общественным транспортом с меньшими усилиями и за меньшее время.
позволяет путешествовать с большой группой друзей
В больших транспортных средствах, таких как минивэны или внедорожники, достаточно места для размещения примерно 6 или 8 пассажиров.Таким образом, путешествие с большой группой друзей или большой семьей больше не будет проблемой. Кроме того, это может даже снизить ваши транспортные расходы при аренде автомобилей или использовании общественного транспорта.
Топливная эффективность означает снижение транспортных расходов
Автомобили доступны во многих типах, конфигурациях и комплектациях. Автомобили среднего размера, купе, седаны, субкомпактные и компактные автомобили обладают высокой топливной экономичностью и имеют более низкий уровень выбросов CO 2 . Многие легко предлагают пробег до 30 миль на галлон или более в городе.Следовательно, это может привести к значительной экономии расходов на общественный транспорт.
Безопасный вид транспорта
По сравнению с общественным транспортом автомобили намного безопаснее. Они оснащены многочисленными функциями безопасности, включая подушки безопасности, адаптивный круиз-контроль, обнаружение столкновений, предупреждения о выезде с полосы движения, давление в шинах, ремни безопасности и мониторинг слепых зон, а также систему помощи при торможении.
Все эти функции делают вождение более безопасным. Дополнительно автомобили проходят испытания на безопасность при авариях.Поэтому, если вы покупатель, заботящийся о безопасности, вы всегда можете взглянуть на рейтинги безопасности IIHS и NHTSA по результатам краш-тестов, чтобы узнать больше о безопасности приобретенного вами автомобиля.
Надеюсь, вы знаете, почему автомобили так важны в современном быстро меняющемся мире, и, разумно инвестируя в них, вы сможете воспользоваться преимуществами удобства, безопасности и экономичности путешествий. Если вы хотите приобрести новый автомобиль в 2015 году, загляните сюда, чтобы увидеть список 10 ведущих автомобильных брендов 2014 года, чтобы понять, какой автопроизводитель вам следует учитывать при поиске автомобиля.
ответов для автомобиля
Автомобиль
А
В настоящее время в мире насчитывается более 700 миллионов автотранспортных средств, и их число ежегодно увеличивается более чем на 40 миллионов. Среднее расстояние, которое проезжают автомобилисты, также растет — с 8 км в день на человека в Западной Европе в 1965 году до 25 км в день в 1995 году. Эта зависимость от автомобилей привела к серьезным проблемам, включая загрязнение окружающей среды, истощение запасов нефти. ресурсы, пробки и безопасность.
Б
Хотя выбросы от новых автомобилей намного менее вредны, чем раньше, городские улицы и автомагистрали становятся более переполненными, чем когда-либо, часто старыми грузовиками, автобусами и такси, которые выделяют чрезмерное количество дыма и дыма. Из-за такой концентрации транспортных средств качество воздуха в городских районах становится неприятным, а иногда и опасным для дыхания. Даже Москва вошла в список столиц, страдающих от пробок и автомобильного дыма. В Мехико автомобильное загрязнение представляет собой серьезную опасность для здоровья.
К
Еще сто лет назад большинство путешествий было на расстояние 20 км, расстояние, на которое легко добраться на лошади. Тяжелые грузы можно было перевозить только по воде или по железной дороге. Изобретение автомобиля принесло личную мобильность в массы и сделало возможной быструю доставку грузов на гораздо более обширную территорию. Сегодня около 90% внутренних грузовых перевозок в Соединенном Королевстве осуществляется автомобильным транспортом. Ясно, что мир не может вернуться к конной повозке. Сможет ли он избежать попадания в перегруженные и загрязняющие окружающую среду пути перевозки людей и товаров?
Д
В Европе большинство городов по-прежнему рассчитаны на использование старых видов транспорта.Адаптация к автомобилю включала добавление кольцевых дорог, систем с односторонним движением и парковок. В Соединенных Штатах больше земли отводится под автомобили, чем под жилье. Разрастание городов означает, что жизнь без машины практически невозможна. Массовое использование автомобилей также привело к гибели или ранениям миллионов людей. Автомобиль приписывают и другим социальным эффектам, таким как отчуждение и агрессивное поведение человека.
E
Исследование, проведенное Европейской федерацией транспорта и окружающей среды в 1993 году, показало, что автомобильный транспорт в семь раз дороже, чем железнодорожный, с точки зрения внешних социальных издержек, которые он влечет, таких как заторы, аварии, загрязнение, потеря пахотных земель и естественной среды обитания, истощение нефтяные ресурсы и так далее.Тем не менее, автомобили легко превосходят поезда или автобусы как гибкий и удобный вид личного транспорта. Нереально ожидать, что люди откажутся от личных автомобилей в пользу общественного транспорта.
Факс
Технические решения могут уменьшить проблему загрязнения и повысить топливную экономичность двигателей. Но расход топлива и выбросы выхлопных газов зависят от того, какие автомобили предпочитают клиенты и как они управляются. Многие люди покупают машины большего размера, чем они нужны для повседневных нужд, или тратят топливо, агрессивно управляя автомобилем.Кроме того, использование автомобилей во всем мире растет более быстрыми темпами, чем улучшение выбросов и топливной экономичности, которое теперь стало возможным благодаря технологиям.
г
Одним из предложенных решений является долгосрочное решение по проектированию городов и кварталов таким образом, чтобы в поездках на автомобиле не было необходимости — все основные службы располагались в пределах пешей досягаемости или легко доступны на общественном транспорте. Это не только сэкономит энергию и сократит выбросы углекислого газа, но и повысит качество жизни общества, с упором на людей, а не на автомобили.Хорошие местные органы власти уже кое-где это делают. Но немногие демократические сообщества наделены видением — и капиталом — для столь глубоких изменений в современном образе жизни.
H
Более вероятным сценарием представляется комбинация систем общественного транспорта для проезда в города и вокруг них с небольшими автомобилями с низким уровнем выбросов для городского использования и более крупными гибридными автомобилями или автомобилями с обедненным газом для использования в других местах.