Антикоррозионные материалы (двухкомпонентные)
Антикоррозионные материалы SHEG (двухкомпонентные)
Любые конструкции из металла, которые применяются при строительных работах, необходимо качественно защищать от воздействия внешней среды, точнее, от развития коррозии. Под воздействием окружающей среды в результате коррозийных процессов металл теряет свои свойства.
Присутствие коррозии приводит к уменьшению срока службы любого оборудования на производстве, конструкций из металла, это ухудшает качество продукции, которая производится данным оборудованием. Антикоррозийные покрытия от компании «SHEG — Полимер» позволяют значительно уменьшить потери при производстве.
Чтобы решить проблемы с увеличением срока эксплуатации и обеспечением химической защиты металлу, из которого сделано оборудование, конструкции и сооружения, в компании «SHEG — Полимер»

Бетон является основным строительным материалом, который тоже необходимо хорошо защищать. Этот строительный материал имеет пористость, что делает его высокопроницаемым и снижает его прочность.
Для предотвращения разрушений появляется необходимость ограничить поступление воды и других агрессивных веществ к бетонному основанию. Компания «SHEG – Полимер» разработала и ввела в эксплуатацию высококачественные покрытия для защиты конструкций и сооружений из бетона и железобетона.
Покрытие обладает влагостойкостью и малой чувствительностью к химическому воздействию, что уменьшает вероятность попадания воды в защищаемую поверхность и предупреждает дальнейшее разрушение материала.
Области применения:
— машиностроение и металлообработка;
— промышленность по переработке нефти;
— энергетическая и химическая промышленность;
— строительство;
— судостроение;
— торговые и складские помещения.
ГРУНТ:
Грунт SHEG-560EP (жидкий, красно-коричневый) — двухкомпонентный состав на основе эпоксидной смолы, аналог ЭП-0010. Материал предназначен для грунтования любых поверхностей на различных объектах промышленной зоны. Покрытие устойчиво к действию растворов щелочей, солей и кислот, нефтепродуктов, морской и пресной воды.
Грунт SHEG-561EP (жидкий) — двухкомпонентный грунт на основе эпоксидной смолы. Используется при грунтовании металлических поверхностей перед нанесением защитного химстойкого покрытия на различных промышленных объектах.
Грунт SHEG-562EP (жидкий) — двухкомпонентный грунт на основе эпоксидной смолы. Используется в судостроении, судоремонте и в химической промышленности. Его наносят, чтобы обеспечить защиту металлическим поверхностям оборудования, конструкций и гидросооружений, подводной и надводной частей судов.
Грунт SHEG-760PU (жидкий) — двухкомпонентный полиуретановый грунт. Применяется для грунтования поверхностей из металла перед нанесением защитного атмосферостойкого покрытия на различных промышленных объектах. Преимущество грунта в том, что он не мелуется, что обеспечивает сохранение межслойной адгезии.
Пропитка SHEG-510EP (жидкая) — пропитка укрепляющая поверхность для бетонных, железобетонных и каменных конструкций, цементосодержащих оснований для площадок под наливные полы (в т.ч. для предприятий пищевой промышленности), защитные покрытия, подвергающиеся высоким химическим нагрузкам (резервуары, водосборники, очистные сооружения, другие конструкции) в цехах, гаражах, на АЗС и т. п. Повышает прочность и защищает основание от проникновения химикатов, жиров, масел, растворителей. Применяется для пропитки, грунтовки, шпатлевки поверхностей, а также в качестве выравнивающего слоя и/или заполнения деформационных швов и трещин.
ЭМАЛЬ:
Эмаль SHEG-570EP — двухкомпонентная эмаль, основой которой служит эпоксидная смола. Аналог ЭП-140. Используется при окраске заранее загрунтованных металлических и бетонных поверхностей в местах, не доступных попаданию прямых солнечных лучей и осадков.
Эмаль SHEG-571EP — двухкомпонентная эмаль на основе эпоксидной смолы. Аналог ЭП-1155. Используется для защиты конструкций из стали и бетона, мостовых ферм, которые эксплуатируются в атмосферных условиях и водной среде.
Эмаль SHEG-572EP — двухкомпонентная эмаль, основой которой является эпоксидная смола.
Эмаль SHEG-573EP — двухкомпонентная эмаль на основе эпоксидной смолы. Аналог ЭП-574. Используется для антикоррозионной защиты металлических, бетонных, железобетонных и цементосодержащих поверхностей.
Эмаль SHEG-770PU — двухкомпонентная эмаль на основе полиуретана. Применяется как защитное покрытие для загрунтованных поверхностей из металла и бетона, которые подвергаются атмосферному воздействию в различных зонах промышленных предприятий.
Эмаль SHEG-771PU
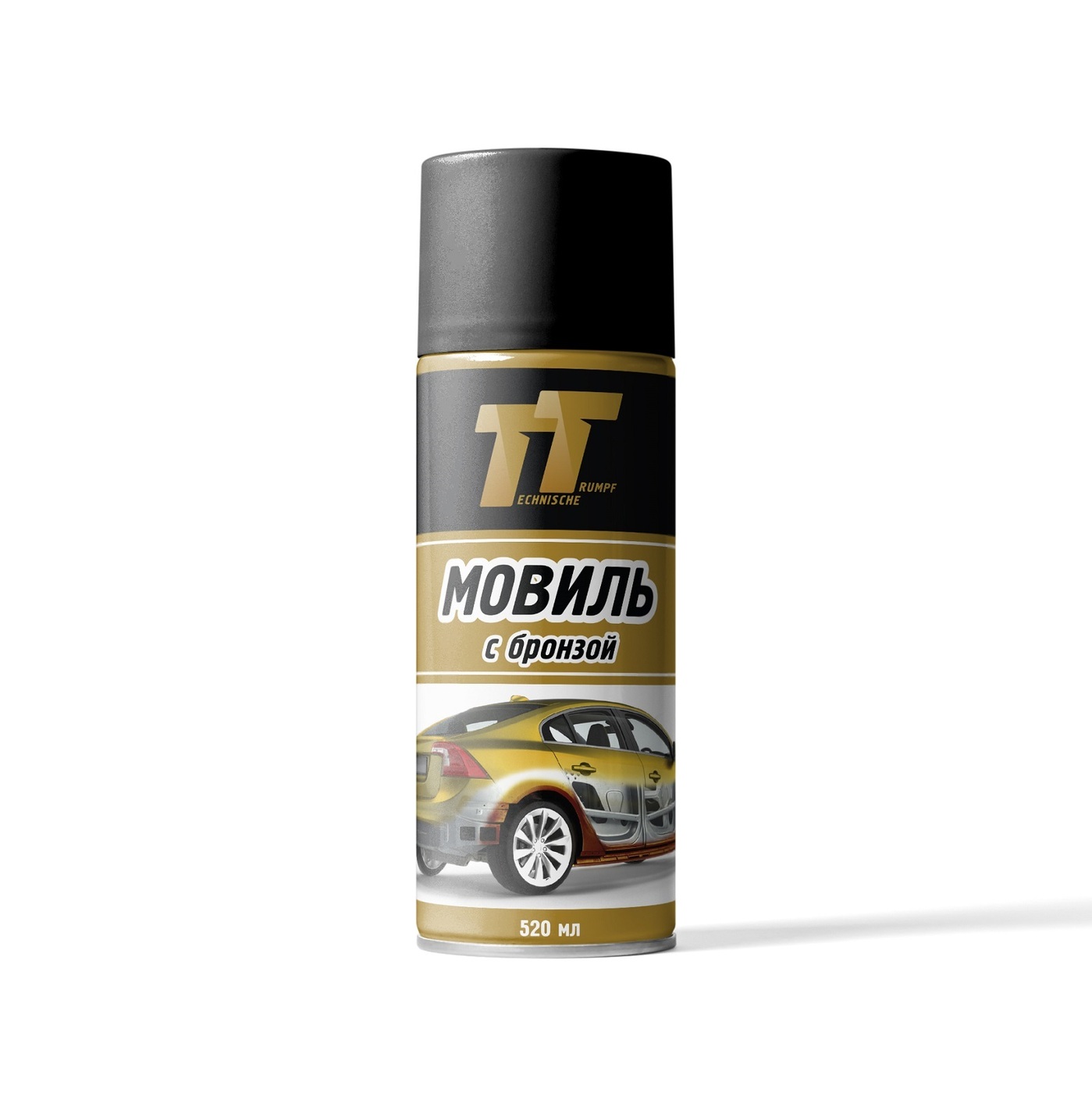
Эмаль SHEG-772PU — двухкомпонентная эмаль на основе полиуретана. Используется в судостроении и судоремонте для окрашивания подводной части и пояса переменной ватерлинии судов. Применяется для защиты стальных и бетонных конструкций и гидросооружений, эксплуатация которых проходит в морской, пресной и технической воде.
Эмаль SHEG-773PU — двухкомпонентная эмаль на основе полиуретана. Используется в судостроении и судоремонте для окрашивания палубных конструкций судов. Ее также используют для защиты металлических и бетонных поверхностей от воздействия промышленных газов.
Эмаль SHEG-774PU — двухкомпонентная эмаль на основе полиуретана. Используется в судостроении и судоремонте при окрашивании палуб и палуб активной эксплуатации. Также применение эмали в промышленности необходимо для защиты стальных и бетонных конструкций и гидросооружений, эксплуатация которых проходит в морской, пресной и технической воде.
Эмаль SHEG-775PU — двухкомпонентная эмаль на основе полиуретана. Используется в судостроении и судоремонте. Ею окрашивают надводный борт и надстройки судов. В промышленности используется для защиты сооружений и конструкций, находящихся в эксплуатации в непосредственном контакте с технической, пресной и морской водой.
Фасовка: 20 кг.
РАЗБАВИТЕЛИ:
SHEG — 000PU – для эмали на основе полиуретана.
SHEG – 000ЕР — для эмали на основе эпоксидной смолы.
Тара: 1л, 5л, 10л, 20л, 200л.
ОЧИСТИТЕЛЬ-ОБЕЗЖИРИВАТЕЛЬ:
SHEG – 0161 — состав для очистки и обезжиривания поверхности металла и бетона.
Тара: 1л, 5л, 10л.
ЗАЩИТНОЕ ПОКРЫТИЕ:
SHEG-574EP – двухкомпонентный состав на основе эпоксидной смолы. Его используют в качестве защитного покрытия для ранее загрунтованных поверхностей из металла и бетона, а также возможно применение для устройства декоративного и промышленного напольного покрытия – полов, путем создания тонкого слоя защитного покрытия или окраски.
Лак SHEG-557EP (жидкий) — химически стойкий лак для защиты от воздействия химикатов, кислот и щелочей, стойкость к высоким температурам.
ШПАТЛЁВКА:
SHEG-521EP — двухкомпонентная шпатлевка на основе эпоксидной смолы. Используется при выравнивании язв, выбоин и некоторых дефектов в судостроении и судоремонте, а также и в химической промышленности. Обеспечивает защиту от коррозии металлических и бетонных конструкций, гидросооружений, градирен, надводных и подводных частей судов.
Фасовка: 20 кг.
Антикоррозионные материалы покрытия — Справочник химика 21
Армированные покрытия на основе синтетических смол — новый изоляционный антикоррозионный материал. В этих покрытиях применяются эпоксидные и полиэфирные смолы. [c.181]Полиизобутилен марки П-200 используется для получения антикоррозионных покрытий внутренней поверхности емкостей, резервуаров для хранения кислот, щелочей и других агрессивных сред. Для этой цели наибольший интерес представляют смеси на основе полиизобутилена, графита, сажи, талька и асбеста. Так, антикоррозионный материал марки ПСГ получается смешением [c.339]
Окрашенное техническое средство сдают в эксплуатацию после его выдержки при 18—23 С в течение 10— 12 сут.

Наличие в составе грунтовки и эмали меламиноформальдегидной смолы значительно повышает водостойкость готового покрытия. Эмаль и грунтовку доводят до рабочей вязкости разбавителем РКБ-1 (ТУ 6010-1326— 72) или смесью бутилового спирта и ксилола (или сольвента), взятых в соотношении 1 1. Материал покрытия наносят на новерхность пневматическим распылением или обливом. Грунтовку и эмаль сушат при 120 °С в течение 1 ч. Для обеспечения необходимых сплошности и антикоррозионных свойств толщина покрытия должна составлять 40—55 мкм. [c.73]
Надежность и долговечность антикоррозионного лакокрасочного покрытия определяются способностью материала, из которого оно изготовлено, длительно сохранять свои свойства в условиях эксплуатации защищаемого сооружения, правильным выбором системы покрытия и точным соблюдением технологии его нанесения. Покрытие должно выполняться из водоустойчивого материала, обладающего высокими адгезионными и диэлектрическими свойствами, эластичностью, устойчивостью к истиранию и динамическим воздействиям, коррозионной стойкостью, химической инертностью по отношению к металлу трубы и биостойкостью [16—18]. [c.21]
Битумные материалы хорошо совмещаются с синтетическими смолами. Так, например, если в каменноугольную смолу добавить эпоксидную смолу получается ценный антикоррозионный материал ЭКС-1, обладающий свойствами составных компонентов. Этот материал наносят в виде мастики он затвердевает без нагревания в слое любой толщины. Покрытия из ЭКС-1 стойки в серной, соляной и 5%-ной азотной кислотах, а также в [c.204]
Верхнее покрытие пола может быть монолитным и бесшовным (кислотоупорный цемент, асфальт и др.) или может быть выполнено из штучных элементов (метлахская или диабазовая плитка, кислотоупорный кирпич и др.), уложенных по кислотостойкой замазке. Выбор зависит от характера агрессивных сред и механических воздействий. Все цементы и замазки на силикатной основе в той или иной мере проницаемы, поэтому под верхнее покрытие пола обязательно нужно укладывать непроницаемый гидроизоляционный и антикоррозионный материал. Особенно рекомендуется для этой цели листовой полиизобутилен ПСГ, который в стыках можно не только склеивать, но для большей надежности и сваривать горячим воздухом [12]. Однако полиизобутилен ПСГ совершенно неустойчив в органических растворителях и минеральных маслах.
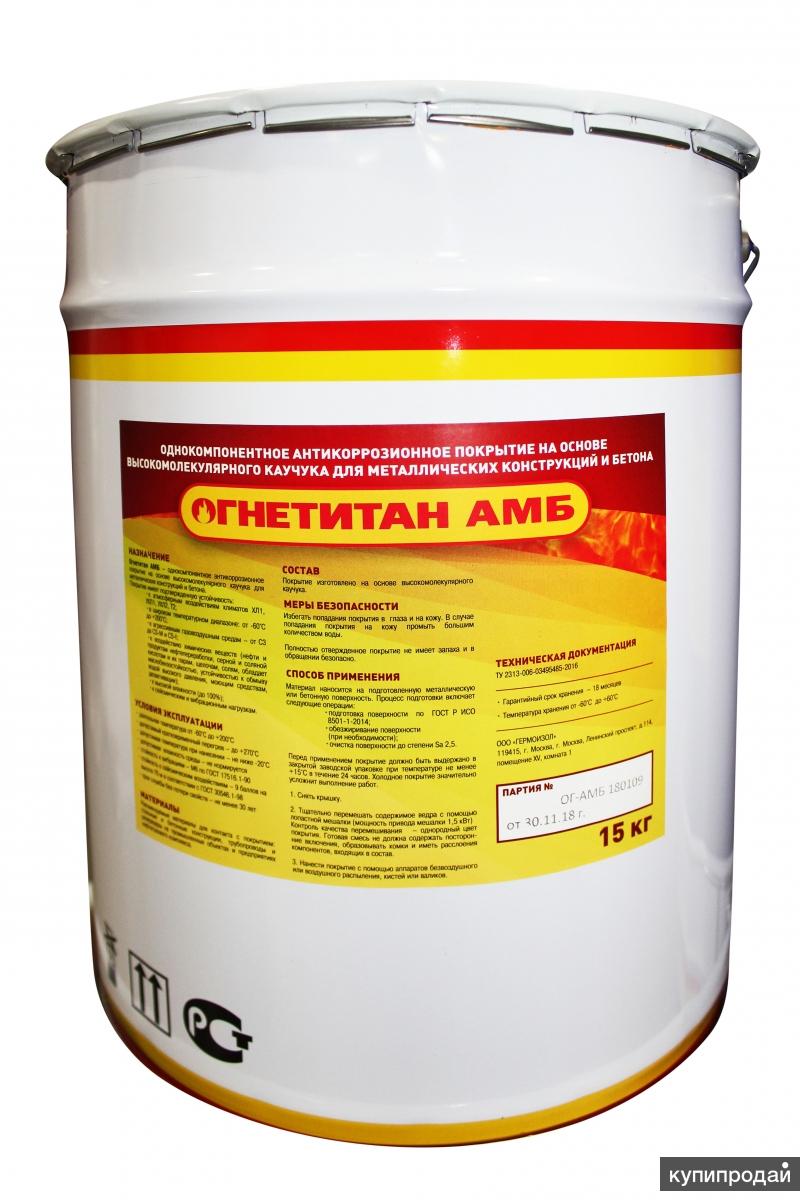
Очень важным преимуществом пластических масс по сравнению, например, с металлами является высокая стойкость к действию воды и многих химических реагентов (растворов солей, кислот и щелочей). Поэтому некоторые пластмассы широко применяются в химическом машиностроении в качестве антикоррозионного материала, не требующего специальных защитных покрытий. Наибольшей химической стойкостью обладают политетрафторэтилен, полиэтилен, полиизобутилен, полистирол и полихлорвинил. На политетрафторэтилен не действует даже царская водка. [c.121]
Л. Оуэн наносил антикоррозионные никелевые покрытия в результате разложения N1(00)4 на сталь, медь, бронзу и другие металлы [369]. В этом случае реактор представляет собой стеклянный колпак высотой 300 или 400 мм и диаметром 64 или 178 мм в зависимости от габаритов изделий. Процесс никелирования проводится при температуре подложки 200°С, давлении 1—2 мм рт.ст. и скорости подачи N1(00)4 1—1,5 г/ч (по никелю). Как показывают испытания, при толщине слоя 12,7 мкм поры в никелевом покрытии отсутствуют и оно обеспечивает полную защиту материала от агрессивной среды. [c.216]
Все возрастающее распространение получают также и поли-изобутилены. Обладая высокой химической стойкостью, они применяются в качестве антикоррозионного материала взамен свинцовых покрытий. [c.11]
Частые трещины на покрытии в виде мелкой сетки вызываются нанесением покрытия при резкой разнице температур поверхности бетона и рабочего состава антикоррозионного материала. Указанный признак свидетельствует также о неравномерной толщине слоя и нанесении покрытия на непросохший предшествующий слой. [c.101]
В современной технике часто требуется герметизировать отдельные сложные детали и профилированные изделия эластичными каучуковыми уплотнителями, наносимыми в жидком состоянии или в виде паст. В качестве примера можно привести вакуум-конденсаторы на современных теплоэлектроцентралях, где установлены турбины, работающие на паре, характеризующемся сверхвысокими параметрами. При герметизации промышленного конденсатора на Московской TЭЦ I2, насчитывающего около 6 тыс. трубок, хорошие результаты показал жидкий наирит, который в данном случае используется как герметизирующий и как антикоррозионный материал (рис. 23). Наиритовое покрытие успешно эксплуатируется уже [c.110]
Аппараты и установки химических производств, как известно, подвержены коррозии. По экономическим и техническим соображениям применение легированных металлов в качестве коррозионностойких материалов не всегда оправданно. Часто для этой цели подходит менее дорогостоящая ферритная сталь с долговечным и стойким к Коррозии покрытием поверхности [41]. При температурах до 140 °С в качестве антикоррозионного материала может применяться композиция на основе фенольной смолы и кислотостойких наполнителей . Отвержденная композиция по стойкости к кислотам и растворителям превосходит некоторые другие защитные материалы. Она обладает стойкостью к действию минеральных и органических кислот (за исключением НСООН), спиртов, углеводородов и их хлорпроизводных, сложных эфиров, не стойка к галогенам, щелочам, окислителям. [c.268]
Химически стойкие асфальты применяют в качестве антикоррозионного материала для верхнего покрытия полов для защитных прослоек стяжек в кровельных и междуэтажных перекрытиях от- [c.85]
Диффузионная проницаемость для агрессивных веществ — одна из важнейших характеристик антикоррозионного материала защитных покрытий и футеровок. [c.57]
При проектировании машин для производства химических волокон, работающих во влажных и агрессивных средах, особое внимание следует уделять защите деталей от коррозии выбирать антикоррозионный материал как для изготовления самих деталей, так и для защитного покрытия (свинец, коррозионностойкие стали, бакелит, карболит, винипласт, фаолит, полиэтилен, полипропилен, фторопласт, резина и т. д.). [c.11]
Пленки, трубы, облицовочный материал, оболочки кабелей, шланги, емкости для агрессивных жидкостей, предметы ширпотреба Упаковочные пленки, посуда, электроизоляционные покрытия, трубы, большие емкости, детали для холодильников и радиоприемников. Синтетические волокна Электроизоляционные покрытия. Антикоррозионный материал [c.98]
Разрушение материала антикоррозионного покрытия цистерн под действием динамических и вибрационных нагрузок, а также в результате специфических условий эксплуатации судна (качка, колебания температур и др.). Материал покрытия мигрирует в воду в виде высокодисперсных твердых частиц и в ионной форме. [c.75]
Перхлорвиниловые покрытия могут найти применение для защиты холодной аппаратуры и оборудования нефтеперерабатывающих заводов. Перхлорвиниловый лак представляет собой прекрасный антикоррозионный материал при защите коммуникаций и аппаратуры от атмосферной коррозии в цехах, где применяются жидкости, имеющие кислый характер. [c.106]
Окраска электроосаждением широко используется в современном массовом производстве. При ее применении возможна полная автоматизация окрасочных работ, значительно меньше загрязняется атмосфера, экономится дефицитный лакокрасочный материал, повышаются антикоррозионные свойства покрытий. [c.169]
Фторопласт-3 расходуете на уплотнительные детали, работающие при высоких давлениях прокладки, работающие в агрессивных средах при давлении до 3,2 МПа и рабочей температуре от —70 до +50 °С, на детали для клапанов кислородных приборов, работающих при давлении до 15—20 МПа, мембраны используется в качестве диэлектрика для особо ответственных деталей и как антикоррозионный материал в виде покрытий. Из фторопласта-3, наполненного фарфоровой или кварцевой мукой, изготавливают сложные (фасонные) детали различного назначения. [c.32]
Действительно, многолетней практикой установлено, что правильный выбор грунтовочного материала существенно влияет на антикоррозионные свойства покрытия. [c.27]
Чтобы предотвратить разрушение канализационных сетей, колодцев, камер и других сооружений, необходимо их выполнять из материалов, стойких к коррозионному воздействию агрессивных компонентов сточных вод. Выбор того или иного материала определяется характером агрессивной среды, ее концентрацией, температурой, давлением и т. д. Для транспортировки агрессивных сточных вод можно применять трубы из нержавеющих сталей, стальные гуммированные трубы, фаолитовые, текстолитовые, стеклянные, полиэтиленовые, стальные, футерованные химически стойкими пластмассами, эмалированные и другие трубы. Оборудование для обработки и перекачивания стоков (насосы, теплообменники, разделители, сборники и др.) можно изготавливать пз легированных сталей или из углеродистых сталей с соответствующими антикоррозионными покрытиями (футеровка кислотоупорным кирпичом или плиткой, покрытия из винипласта, свинца, полиэтилена и т. д., лакокрасочные покрытия, гуммирование и др.). [c.256]
Схематически структура защитных покрытий представлена на рис. 50 Защшпые противокоррозионные покрытия формируются обычно послойно из различных материалов и могут иметь разную толщину. Количество слоев и материал слое определяется назначением защищаемой конструкции и условиями ее эксплуатации. Структура некоторых видов антикоррозионных неметаллических покрытий приведена в табл. 4. [c.88]
Основное функциональное назначение любого антикоррозионно, го покрытия — обеспечение защиты материала конструкции от непосредственного контакта с агрессивной средой, от кавитационных, эрозионных и абразивных воздействпй. Защитное покрытие может выполнять также и антиадгезионную роль, препятствуя налипанию или отложению компонентов среды на стенках аппаратов и трубопроводов. Химическое оборудование с полимерным покрытием выполняет различные функции, которые так или иначе влияют на выбор критерия отказа. Так, например, предельное состояние емкостной, колонной и реакционной аппаратуры с покрытием должно отличаться от предельного состояния насосов, вакуум-фильтров, центрифуг и т. д. Во многих случаях необходимо устанавливать предельные состояния для отдельных элементов и узлов аппаратов и машин форсунок, оросителей, мешалок, колес центробежных насосов п т. д. Такой подход позволяет более рационально выбирать тип и конструкцию полимерного покрытия. [c. 44]
При выборе материалов покрытий основных узлов вентиляторов (рабочее колесо, корпус) должны учитываться также коррозионные свойства транспортируемой среды материал покрытий должен исключать искрообразование при соударении деталей и обладать необходимыми антикоррозионными свойствами. Этим не только продляется срок службы вентиляторов, но и повышается их взрывобезопасность. Следует указать, что безопасность при работе вентиляторов, являющихся одним из элементов транспортных систем, обеспечивается соблюдением необходимых требований при проектировании, монтаже и эксплуатации специальных систем вентиляции. Проектом векткляцноппой системы должны предусматриваться технические решения, исключающие попадание посторонних предметов в вентиляторы (например, заградительные сетки, предохранительные клапаны и т. д.) и контроль параметров перемещаемой среды (температуры, состава, влажности и т. д.). [c.376]
Широко применяется поливинилхлорид в химической и других отраслях промышленности в качестве антикоррозионного материала [764—770]. Устойчивые к агрессивным средам покрытия из поливинилхлорида [771, 774] применяются для окраски корабельных корпусов [772, 773, 775], для защиты от действия влаги и коррозии трубопроводов [776—778], металлических изделий [779, 780], различных емкостей и оборудования [781 — 783], фасадов зданий [784] и т. д. В работе Стильберта и Каммингса описываются огнезащитные покрытия из поливинилхлорида [785], которые при действии высоких температур вспениваются и изолируют изделие от огня. [c.295]
Жидкий наирит промышленной марки НТ — это антикоррозионный материал типа резины, используемый в качестве защитных покрытий. Покрытия эти бензомаслозодостойкие и обладают хорошим сопротивлепием абразивному износу. Вулканизуют их открытым способом на воздухе без давления простыл прогревом при температуре 100 °С и ниже. [c.216]
В цикле исследований, направленных на получение низкомолекулярных хлоропреновых каучуков, пригодных для изготовления жидких гуммировочных антикоррозионных составов [132—134], были разработаны эмульсионные полихлоропрены, названные масляным и дисперсным жидкими наиритами. Отработаны оптимальные условия механохимической деструкции указанных наиритов, а также уже освоенного промышленностью наирита НТ (низкотемпературного). Последний несколько труднее деструктируется, но как антикоррозионный материал обладает рядом эксплуатационных достоинств. Из них важнейшими являются 1) способность, вследствие кристаллизации, отверждаться без термической обработки и давать не только вулканизованные, но и невулканизованные покрытия с хорошими защитными свойствами 2) способность образовывать после вулканизации при 100°С эластичные покрытия с лучшими физикомеханическими показателями, а также с более высокой химической и износостойкостью. Для промышленного производства был принят жидкий гуммировочный состав на основе наирита НТ [135], получение и применение которого подробно описано ниже. [c.104]
По окончании работ на каждой захватке распылитель, красконагнетательный бак и щланги, по которым подают антикоррозионный материал, промывают растворителем, на котором был приготовлен рабочий состав покрытия. Для промывки огнеопасными растЕорктелями аппаратуру опускают вниз, где для этой цели по согласованию с пожарной охраной отводится специальное место. [c.98]
Толь — картон, пропитанный каменноугольным дегтем и посыпанный с обеих сторон речным песком. По прочности толь З тупает другим рулонным материалам и применяется в качестве кровельного материала в покрытиях временного типа как антикоррозионный материал толь менее надежен, чем другие рулонные материалы. [c.63]
Обусловленные парафиновым характером полиизобутилена иротивостарительная и химическая стабильность, а также его полнейшая невосприимчивость к воде вызвали широкое применение полиизобутилена в качестве антикоррозионного материала в химическом машиностроении и строительном деле [1], [2], [186]. Фирма И. Г. Фарбениндустри применяла полиизобутилен в форме полос, листов и покрытий в качестве изолирующего промежуточного слоя на бетоне, кирпиче или подобном футеровочном материале для емкостей с кислотами и растворителям, а также в качестве защитного слоя для стен, перекрытий, полов, стенок сосудов и т. д. из металла, бетона и кирпича, причем связующим агентом служил битум или асфальт с добавкой полиизобутилепа [310], [311]. [c.297]
Необходимо отметить, что рекомендации в отношении пригодности материалов к использованию в различных условиях носят скорее качественный характер, что затрудняет выбор антикоррозионного материала. Чтобы можно было хотя бы приблизительно сравнивать и обобщать однородные показатели, применяют систему числовых оценок. Важность различных свойств материалов оценивают по десятибалльной числовой шкале (1 — высший балл). Таким образом, представляется возможность располоншть конкурирующие материалы в один ряд и сравнить их достоинства по оценочным баллам [45]. Пример такой оценки для антикоррозионных покрытий па основе модифицированной и немодифицирован-ной фенольных смол приведен ниже [c.271]
Для его нанесения применяли две конструкции машин. На одной из них покрываемые изоляцией трубы оставались неподвижными, а головка вращалась со скоростью 110 об/мин и продвигалась внутри трубы. Сжатый воздух использовался как для извлечения из трубы оставшейся окалины, так и для распыливания антикоррозионного материала. У другой машины головка п труба вращаются со скоростью 110 обКмин в противоположные стороны. Для удаления оставшейся окалины применялся вакуум. Покрытие наносилось через форсунки иод давлением. Стальные щетки вращались со скоростью 1200 об/мин. [c.219]
Прозрачные поливинилфторидные покрытия можно наносить непосредственно на различные металлические субстраты, например на хромированные поверхности, на медь, латунь, сталь, алюминий и др. [52-61]. Они обеспечивают превосходную защиту от коррозий и не изменяют декоративный вид материала [351 Это позволяет применять поливинилфторид в качестве антикоррозионного материала для использования в автомобилестроении. Кроме того, этот полимер можно. применять для изготовления светоотражательных дорожных знаков [Зб]. [c.215]
Много винилхлорида потребляется в производстве пер-хлорвипиловой смолы — ценного пленкообразующего вещества. Перхлорвияиловая смола служит исходным продуктом для получения синтетического волокна хлорин. Из этого волокна изготовляют фильтровальные ткани и антикоррозионные защитные покрытия для аппаратуры ткань из волокна хлорин идет на пошив защитой одежды для персонала, работающего с вредными веществами, и используется в качестве электроизоляционного материала. [c.9]
Б р а ц ы X и н Е. А., Пластические массы в качестве антикоррозионного материала, Материалы I Ленинградской конференции по неметаллическим защитным покрытиям, литографир. изд., Л. 1937. [c.563]
Прибавка на коррозию равна скорости коррозии v (мм/год), умноженной на срок службы т аппарата (обычно 10—12 лет) с = = ит. Скорость коррозии определяют по справочникам или По лабораторным испытаниями. Прибавку на коррозию обычно принимают I—2 мм, что соответствует скорости 0,1—0,2 мм/год. При более интенсивной коррозии стенки аппарата необходимо защищать антикоррозионными покрытиями или заменять конструкционный материал другим, более коррозионно-стойким. Для неответственных частей аппаратов скорость коррозии может быть принята и большей. Если стенка подвергается коррозии с двух сторон, то необходимо ввести две прибавки на коррозию. Для чугунных отливок прибавку на коррозию и возмолшую разностенность отливок принимают равной 5—9 мм. Для аппаратов из двухслойной стали в расчет принимается только слой основного металла, а плакирующий слой может быть учтен только в качестве прибавки на коррозию. Прибавки С2 и Сз учитывают только тогда, когда сумма их превышает 5% от расчетной толщины листа. [c.39]
Антикоррозийные материалы — Строительная химия
Антикоррозийные материалы необходимы на любой из стадий производства и строительства, так как возникновение коррозионного процесса не только приведет к безвозвратным потерям, но и зачастую становится причиной выхода из строя необходимых дорогостоящих сооружений и изделий. Антикоррозийное покрытие позволяет сократить потери, которые составляют приблизительно 12% от выплавки металла за год, а, учитывая увеличение использования конструкций из металла, потери возрастают постоянно. По этой причине эксперты рекомендуют тщательнее выбирать как антикоррозионные материалы так и методы защиты, при этом антикоррозийное покрытие, прежде всего, должно быть качественным и долговечным.
Именно такие антикоррозийные материалы, которые также выгодно отличаются оптимальным сочетанием стоимости и качества, предлагает наша компания для долговременной защиты ваших объектов из металла. Позвоните нашим менеджерам, и они подберут лучший вариант из предлагаемых материалов.
Сегодня рынок предлагает различные антикоррозионные материалы.
Почему именно производитель Ай-Си-Ти Кемикал?
Использование материалов Ай-Си-Техно Пенетрируующий праймер дает возможность снизить затраты на качественную очистку металлических поверхностей от предыдущих покрытий и коррозийных продуктов.
Антикоррозийные материалы Покрытие Пу, Праймер ПУ и Ай-Си-Топ Пенетрирующий праймер позволяет производить работу по обеспечению антикоррозийной защите даже при отрицательной температуре (от +50 до -5°С) и достаточно высокой влажности — 30–98%.
Благодаря трехслойной системе защиты от коррозии удается получить антикоррозийное покрытие с эксплуатационным сроком не менее 15 лет.
Каждый предлагаемый нами продукт сертифицирован.
Защита металлических изделий, без которых не обходится ни одно возведение объектов и при помощи которых решаются сложнейшие задачи, подразумевает, в первую очередь, создание для поверхности металла покрытия-барьера от агрессивного воздействия атмосферных явлений и, следовательно, коррозии.
Наиболее широко используемый антикоррозионный метод — нанесение полимерных пленок, что позволяет придать металлической поверхности практически любой цвет. При ремонтах он просто незаменим.
Мы производим высококачественное антикоррозийное покрытие из полимеров.
По сути, защитить металл возможно несколькими способами:
- не допустить контакта коррозионно-активных сред с металлической поверхностью;
- при нарушении покрытия контакт должен быть со специальным слоем, противостоящим коррозии (к примеру, грунтовки серии Ай-Си-Техно марки Праймер ПУ).
Важнейшее условие в проведении антикоррозийных работ — качественная предварительная подготовка металлической поверхности к окраске. Это — самое дорогостоящее и сложное мероприятие, особенно, если необходимо удалять большое количество слоев старого покрытия и/или металл сильно поражен коррозией.
Наши менеджеры подскажут наиболее подходящие антикоррозионные материалы для вашего объекта, помогут рассчитать стоимость, а также проконсультируют по многим вопросам.
Также рекомендуем обратить внимание и на одно- и двухкомпонентные полиуретановые клеи, компаунды, наливные полимерные полы и фасадные покрытия.
Номер занятия |
Наименование занятия |
Домашнее задание |
Лз 1 |
Вводное
занятие. Коррозия и защита металлов от коррозии |
1. Задачи № 1,33,47,60; с.85-89;96-104, 137. 2. МУ по теме лаб.занятия. 3. Конспект лекции. |
Лз 2 |
Определение скорости коррозии металла по объему выделившегося водорода |
1. Задачи № 43, 45, 65, 68; с.88-89;96-104. 2. МУ по теме лаб.занятия. 3. Конспект лекций. |
Лз 3 |
Влияние ингибиторов на скорость коррозии металла |
1. 2. МУ по теме лаб.занятия. 3. Конспект лекций. |
Лз 4 |
Скорость коррозии черных и цветных металлов в атмосферных условиях и в водных средах |
1. Задачи № 7, 10, 14,17, 23, 93; с.88-95. 2. МУ по темам лаб.занятий. 3. Конспект лекций. |
Лз 5 |
Гальванические покрытия |
1.
Задачи № 222, 223, 226; с. 2. МУ по теме лаб.занятия. 3. Конспект лекций. |
Лз 6 |
Технология нанесения лакокрасочных покрытий |
1. Задачи № 110, 115, 121, 124, 130,131; с.105-119. 2. МУ по теме лаб.занятия. 3. Конспект лекций. |
Лз 7 |
Изучение физико-механических и защитных свойств покрытий Коллоквиум (для студентов ДФО) по теме: «Коррозия металлов и защитные покрытия в автомобилестроении» |
1. 2. МУ по теме лаб.занятия. 3. Конспект лекций. 4. Вопросы к коллоквиуму. |
Лз 8 |
Полимеры. Резины, их состав, получение и физико-механические свойства. Клеи |
1. Задачи № 186,189,193,199,204, 210, 211; с.125-126. 2. МУ по теме лаб.занятия. 3. Конспект лекций. |
Лз9 |
Заключительное занятие по лабораторному практикуму |
1. 2. МУ по темам лаб.занятий. 3. Домашние задачи 4. Отчеты по лаб.работам. |
МОДУЛЬНЫЙ КОНТРОЛЬ |
||
М 1 |
Теоретические основы коррозии металлов в автомобилестроении |
Проводится на 7-ой неделе |
М 2 |
Антикоррозионные материалы и покрытия в автомобилестроении |
Проводится на 15-ой неделе |
Антикоррозионная защита металлоконструкций | Deltaplast
Различные металлоконструкции, эксплуатируемые под открытым небом или внутри промышленных помещений, подвержены сильному воздействию окружающей среды. Его результат, в большинстве своем, негативный и приводит к коррозии металла.
Ветры, осадки, температурные колебания и солнечная радиация снижают срок эксплуатации конструкций. Причем в городах и на прилегающих территориях металл корродирует гораздо быстрее: в атмосферной влаге (кроме собственно воды) содержится масса агрессивных примесей, выбрасываемых в атмосферу промышленностью и транспортом.
Коррозия приносит столько убытков, что над решением этой проблемы работают лучшие химики и инженеры. На сегодняшний день разработаны технологии, которые при грамотном использовании существенно замедляют процессы коррозии, продлевают жизнь металлоконструкциям, при этом просты в применении и демократичны по цене.
Особенности антикоррозионной защиты крупногабаритных конструкций и сооружений
Как показала практика, наиболее эффективной и экономически оправданной является антикоррозионная защита металлоконструкций при помощи специальных покрытий. Кроме разумной стоимости, их отличают:
- простота нанесения на поверхности любой конфигурации и площади;
- возможность обеспечить наряду с защитной и декоративную функцию.
Все это позволяет активно использовать антикоррозионные покрытия для защиты металлических конструкций больших размеров и сложной формы.
- Здания. Наибольшей коррозионной угрозе подвержены металлические элементы промышленных и складских зданий вследствие более высоких концентраций в воде и воздухе химических реагентов. Защитное покрытие в этом случае подбирается не только исходя из условий эксплуатации, но и с учетом декоративных свойств материала (в помещениях, где работают люди).
- Вышки ЛЭП.
Для их защиты используются специальные системы лакокрасочных материалов, которые отличаются высокой стойкостью в различных климатических условиях и хорошо себя показали при эксплуатации в интенсивных электромагнитных полях.
- Мосты. Жесткие условия эксплуатации таких сооружений предъявляют особые требования к антикоррозионной защите: такие материалы должны быстро наноситься, хорошо себя вести при вибрациях и механических нагрузках, не разрушаться в широком диапазоне температур.
- Резервуары. Стойкость этих конструкций во многом зависит от уровня антикоррозионной защиты, поскольку зачастую в них хранятся очень агрессивные по отношению к металлу вещества — продукты нефтехимии, кислые или щелочные растворы, вода. При этом внутренние и наружные поверхности одного и того же резервуара могут требовать совершенно разных покрытий для сохранения всех эксплуатационных качеств сооружения.
- Трубопроводы. Промышленные (внутри предприятий) и магистральные трубопроводы требуют разных подходов к антикоррозионной защите.
Но объединяет их одно: покрытие должно гарантировать постоянную и безаварийную работу системы на протяжении всего периода эксплуатации.
Типы антикоррозионных покрытий
Существует несколько классификаций антикоррозионных покрытий. Например, по способу нанесения они могут быть мембранными, лакокрасочными, напыляемыми. Есть также градация по степени защиты, которую обеспечивает материал. Но наиболее применимой и информативной принято считать классификацию по химическому составу.
- Полимерные покрытия. На сегодняшний день еще достаточно дороги, но имеют ряд неоспоримых преимуществ перед другими способами защиты. Они эластичны, стойки к большинству агрессивных факторов, по долговечности сравнимы со сроком эксплуатации металлоконструкций.
- Цинконаполненные покрытия. Основной компонент этих лакокрасочных материалов — высокодисперсный порошок цинка. Вследствие того, что содержание активного компонента высоко (более 86% по массе), такие антикоры защищают сталь, в том числе, и электрохимически, подобно горячему цинкованию.
Поэтому данная технология получила название технологии «холодного цинкования». Цинкнаполненные покрытия долго служат, могут применяться в различных условиях, в том числе, в высокоагрессивных, средах.
- Полиуретановые лакокрасочные материалы. Их отличительная черта — высокая эластичность в сочетании с предельной прочностью. Полиуретановые системы (как одноупаковочные так и двухупаковочные) удобны в работе, твердеют при взаимодействии с воздушной влагой, могут наноситься при отрицательных температурах. Химически стойкие, универсальные, имеют высокую адгезию и водостойкость.
- Винилово-эпоксидные материалы. Сочетают в себе твердость, отличное сцепление с основанием, износостойкость, устойчивость к неблагоприятным атмосферным воздействиям.
- Кремнийорганические покрытия. Отличаются, кроме атмосферостойкости и твердости, еще и термостойкостью. Могут применяться на любых нагреваемых поверхностях, как в условиях открытой местности, так и в горячих цехах.
Этапы выполнения работ
Для того чтобы антикоррозионное покрытие проявило все свои лучшие качества, работы по защите объекта проводятся в несколько этапов.
- Осмотр объекта и предварительная оценка объемов работ. На этом же этапе происходит подбор оптимальной технологии антикоррозионной защиты, производятся необходимые расчеты. Подбираются материалы и способы их нанесения.
- Общая подготовка к проведению работ. Готовится проектно-сметная документация, план-график проведения работ и другие документы. Необходимые материалы и оборудование завозятся на объект.
- Подготовка обрабатываемой поверхности. От правильного проведения этого этапа на 80% зависит долговечность антикоррозионного покрытия. С поверхности удаляются все загрязнения, она обезжиривается, на ней создается особый микрорельеф для повышения адгезии основания.
- Нанесение покрытия. Здесь очень важно соблюдать все нюансы технологии, выдерживать временной и температурный режимы.
- Контроль качества полученного покрытия.
Оптимальная методика подготовки основания под антикоррозионную защиту
Безусловно, большую роль играет правильный выбор покрытия для каждого конкретного случая — его делают, основываясь на исходном состоянии поверхности, ее размерах, особенностях эксплуатации, условиях внешней среды и других факторах. Но не меньшую роль играет качественная подготовка поверхности к нанесению покрытия.
Сэкономить деньги и время, при этом получив основание с нужными параметрами, позволяет пескоструйная обработка металлоконструкций. В этом случае за одну операцию удается:
- очистить поверхность металла от нагара, копоти, старого лакокрасочного слоя, свежих граффити, участков коррозии, атмосферных и промышленных загрязнений;
- обезжирить основание, что предотвращает пузырение и отслойку покрытия;
- нанести на поверхность микроборозды, благодаря которым сцепление антикоррозионного материала с поверхностью повышается в несколько раз.
Кроме того, пескоструйка проводится без присутствия воды, что особенно важно при работе с металлом.
Современное абразивоструйное оборудование позволяет в зависимости от условий и требуемого результата варьировать режимы обработки и состав абразивной смеси. При этом такие комплексы мобильны, что позволяет с легкостью перемещать их с объекта на объект. В результате заказчик получает быстро и качественно подготовленную к дальнейшему покрытию поверхность, которая соответствует стандартам и существенно повышает долговечность антикоррозионной защиты металлоконструкций.
Материал предоставлен ООО «Обработка и защита поверхности»
Компания специализируется на оказании услуг по пескоструйной очистке любых поверхностей от различных видов загрязнений (старых лакокрасочных покрытий, ржавчины, окалины, грязи, высолов и т.д.), и нанесению декоративных, защитных, антикоррозионных и гидрофобизирующих покрытий.
Официальный сайт: obrabotka.ru
Антикоррозионная защита.

Коррозия — это самопроизвольное разрушение металлов под воздействием химического или физико-химического влияния окружающей среды.
На сегодняшний день нет такой отрасли промышленности или объекта инфраструктуры в котором бы не применялись металлы. Экономический ущерб, нанесенного коррозионными разрушениями для предприятий нефтегазохимической промышленности, составляет около 50%. Это связано с влиянием на незащищенные поверхности металлоконструкций и оборудования, как агрессивных технологических сред, так и окружающей среды.
Но не только экономические потери влекут за собой коррозионные разрушения. Выход из строя оборудования в процессе его эксплуатации приводит к его разгерметизации и возгоранию, содержащихся в нем, технологических сред. Подобные возгорания в условиях современных производств, приводят к взрывам, уносящим за собой человеческие жизни. Последняя крупная авария на территории России, по причине коррозионного износа, произошла на Ачинском нефтеперерабатывающем заводе в 2014г, тогда погибло 8 человек.
Сегодня существует ряд методик и видов системной защиты металлов от столь нежелательного воздействия коррозии. Самым доступным и экономически оправданным способом защиты металла, является антикоррозионная защита на основе лакокрасочных покрытий.
В основе метода антикоррозонной защиты лежит принцип создании барьера между защищаемым металлом и агрессивной средой. Принимать во внимание следует не только агрессивные технологические среды, но и влияние окружающей среды (воздух и ультрафиолет).
Современные системы антикоррозионной защиты на основе лакокрасочных покрытий состоят из одного или двух видов лакокрасочных материалов, таких как: антикоррозионный грунт и антикоррозионная краска. Тип лакокрасочного материала и сочетание различных типов лакокрасочных покрытий определяются в соответствии с требованиями, предъявляемыми к системе антикоррозионной защиты.
К системе антикоррозионной защиты предъявляются следующие требования:
1. Предполагаемый срок службы;
2. Условия эксплуатации системы антикоррозионной защиты;
3. Условия нанесения;
4. Ремонтопригодность;
В соответствии с вышеперечисленными требованиями подбирается материалы антикоррозионных покрытий, способных защитить поверхность металлоконструкций и технических устройств на срок до 25 лет, при условии соблюдения технологии нанесения лакокрасочных покрытий и проведения своевременного контроля нанесенных лакокрасочных материалов в процессе эксплуатации.
Условия эксплуатации материалов антикоррозионной защиты на основе лакокрасочных покрытий является важнейшим факторов определяющих предполагаемый срок службы системы. Условия эксплуатации определяются количеством и видом агрессивных компонентов, входящих в состав:
1. Технологической среды, воздействующей на внутренние поверхности сосудов и резервуаров;
2. Окружающей среды, воздействующей на наружные поверхности технических устройств, металлоконструкций и конструкций из бетона.
Технологические среды.
Технологические среды бывают следующими:
— нефть и нефтепродукты,
— кислоты,
— вода и газы.
Параметры технологической среды, категории ее коррозийной активности, а также соответствие требованиям технической документации на конкретный лакокрасочный материал, определяются компоненты системы антикоррозионной защиты.
Окружающая среда.
Окружающая среда подразделяется в соответствии с требованиями ИСО 12944-5 на шесть категорий атмосферной коррозионной активности от С1 до С5-М и
на три категории для воды и почвы от Im 1 до Im 3. ИСО 12944-5 рекомендует методику определения системы антикоррозионной защиты. Так же при выборе
систем антикоррозионной защиты учитываются требования технической документации на лакокрасочный материал, выбранный в качестве компонента системы.
Наряду с условиями эксплуатации систем антикоррозионной защиты, важнейшую роль в предполагаемом сроке службы
лакокрасочных покрытий играет и соблюдение технологии их нанесения.
В процессе выполнения работ по антикоррозионной защите необходимо производить следующие виды контроля:
1. Условия окружающей среды;
2. Входной контроль лакокрасочных материалов и абразива;
3. Подготовка поверхности передназначиной для окрашивания;
4. Подготовка лакокрасочных материалов для нанесения на окрашиваемую поверхность;
5. Нанесение антикоррозионного материала и его отверждение;
6. Качество готового покрытия.
Этап подготовки металлической поверхности перед нанесением первого слоя системы антикоррозионной защиты самый ответственный. С целью удаления продуктов коррозии, окалины, загрязнений и т.п. поверхность металла следует очистить. Так же предварительная обработка поверхности металла необходима для её активации. Исключать подготовительные работы нельзя! Иначе образование адгезионных связей между металлической поверхностью и лакокрасочным покрытием, так необходимых для полноценной работы антикоррозийных систем, станет невозможным.
Для классификации степени подготовки поверхности руководствуются требованиями ИСО 8501. Необходимая степень очистки металла индивидуальна для каждого применяемого лакокрасочного материала, и в полном объеме указанна в технической документации. Но как показывает практика только лишь степень абразивоструйной очистки Sa 2,5 (очень тщательная очистка, любые загрязнения выглядят, как не значительное окрашивание в виде пятен или полос) способна создать необходимое количество адгезионных связей для создания системы антикоррозионной защиты с предполагаемым сроком службы до 25 лет.
Контроль, над всеми этапами работ, необходимо производить в соответствии с требованиями ИСО стандартов. Работы по нанесению антикоррозионных красок и антикоррозионных грунтовок в соответствии технической документацией на используемые антикоррозионные материалы. Для объективной оценки, контроль над проведением работ, должен осуществлять независимый, от производителя работ, инспектор. Для создания качественной антикоррозионной защиты и правильного применения всех антикоррозийных систем на объекте, где проводится защита резервуаров, трубопроводов и т.п. присутствие аттестованного и независимого инспектора не вызывает сомнения. Является неотъемлемой частью процесса, и положительно сказывается на сроке службы инфраструктурных объектов.
Правильно подобранные лакокрасочные покрытия и выполнение всех требований по технологии их нанесения необходимо для создания систем антикоррозионного покрытия. Но увеличить предполагаемый срок службы системы антикоррозионной защиты до 25 лет может гарантировать только целостность покрытия на протяжении всего процесса эксплуатации.
В процессе эксплуатации неизбежно появление механических повреждений лакокрасочного покрытия, контроль за выявлениями которых необходим повсеместно. Незначительные механические повреждения, под влиянием окружающей среды, способны перерасти в дефекты покрытия в виде растрескивания и отслоения. Площадь таких дефектов будет многократно превышать размер исходного повреждения. Из вышесказанного следует, что ежегодная инспекция с целью выявления дефектов антикоррозионной защиты с последующим их устранением, является неотъемлемой частью производственного процесса на всех предприятиях.
На основании изложенного мы готовы предложить Вам лучшие технологии и решения, исходя из мирового и Российского опыта по подготовке поверхности, окраске, выбору оптимальных схем антикоррозионной защиты, как для объектов капитального строительства, так и для проведения ремонтных работ, которые позволят получить не только качественное лакокрасочное защитное покрытие с длительным сроком эксплуатации, но и сэкономить бюджетные средства.
Выезд нашего инспектора, на объект на время проведения покрасочных работ, является обязательным условием! Это позволяет обеспечить соблюдение технического регламента и дисциплинированному исполнению пожеланий заказчика. Только специально обученный сотрудник компании Jotun может обеспечить подобающий контроль за проведением всего комплекса работ по созданию высококачественной антикоррозионной защиты.
Соблюдение техники безопасности при производстве работ, входной контроль материалов, подготовительные этапы, контроль по соблюдению технологического регламента, оформление документации, сдача объекта – все это далеко не полный перечень обязательств возложенных на наших специалистов. Все технические инспектора имеют сертификаты «FROSIO» и «Прометей».
Разработка руководящего документа по антикоррозионной защите как металлических так и железобетонных конструкций, определяющий требования к материалам, подготовке поверхности, нанесению покрытия, ремонту, проверке и испытанию покрытий также входит в перечень наших услуг.
Антикоррозионные покрытия ВМП — Продукция ВМП
АЛИСТЕРУС 3105
Защитная грунт-эмаль
ПодробнееАЛЮМОТЕРМ®
Термостойкая кремнийорганическая композиция с алюминиевой пудрой
ПодробнееАЛЮМОТАН®
Полиуретановая композиция с алюминиевой пудрой
ПодробнееАЛПОЛ®
Композиция на основе термопластичного полимера и алюминиевой пудры
ПодробнееВИНИКОР®-акрил-51
Грунт-эмаль на основе полиакриловых смол
ПодробнееВИНИКОР® грунт-эмаль
Грунт-эмаль винилово-эпоксидная
ПодробнееВИНИКОР®-061
Винилово-эпоксидная грунтовка
ПодробнееВИНИКОР®-62 марка А
Винилово-эпоксидная эмаль
ПодробнееВИНИКОР®-62 марка Б
Винилово-эпоксидная эмаль
ПодробнееВИНИКОР®-63
Виниловый лак
ПодробнееВИНИКОР®–марин грунт
Эпоксидная грунтовка
ПодробнееВИНИКОР®–марин эмаль
Эпоксидная эмаль
ПодробнееВИНИКОР®-норд
Винилово-полиэфирная грунт-эмаль
ПодробнееВИНИКОР®–экопрайм
Эпоксидная грунт-эмаль
ПодробнееВИНИКОР®–экопрайм-01
Эпоксидная грунтовка
ПодробнееВИНИКОР®–БЭП-5297
Эпоксидная эмаль
ПодробнееВИНИКОР®–ЭП-5285
Эпоксидная эмаль с отвердителем полиамидного типа
ПодробнееВИНИКОР® ЭП-1155 Д
Эпоксидная эмаль
ПодробнееИЗОЛЭП®-235
Эпоксидная грунт-эмаль
ПодробнееИЗОЛЭП®-mastic
Эпоксидная грунт-эмаль
ПодробнееИЗОЛЭП®-арктик
Эпоксидная грунт-эмаль
ПодробнееИЗОЛЭП®-гидро
Эпоксидная грунт-эмаль
ПодробнееИЗОЛЭП®-mio
Эпоксидная эмаль c «железной» слюдкой
ПодробнееИЗОЛЭП®-SP-03
Межоперационная эпоксидная грунтовка
ПодробнееИЗОЛЭП®-эполайн
Эпоксиуретановая композиция
ПодробнееИЗОЛЭП®-про
Эпоксидная пенетрирующая грунтовка
ПодробнееИЗОЛЭП®-eps
Межоперационная эпоксидная грунтовка
ПодробнееИЗОЛЭП®-primer
Эпоксидная грунтовка с фосфатом цинка и «железной» слюдкой
ПодробнееИЗОЛЭП®-oil
Толстослойная эпоксидная композиция
ПодробнееИЗОЛЭП®-oil 250
Эпоксидная композиция
ПодробнееИЗОЛЭП®-oil 350 AS
Эпоксидная композиция с антистатическими свойствами
ПодробнееНЕФТЬЭКОР® грунтовка
Эпоксидная грунтовка
ПодробнееНЕФТЬЭКОР® эмаль
Эпоксидная эмаль
ПодробнееПОЛИТОН®-ХВ
Эмаль
ПодробнееПОЛИТОН®-УР
Полиуретановая эмаль
ПодробнееПОЛИТОН®-УР (УФ)
Акрилуретановая эмаль
ПодробнееПОЛИТОН®-ZP
Грунт-эмаль
ПодробнееФЕРРОТАН®
Полиуретановая композиция с «железной» слюдкой
ПодробнееФЕРРОТАН®-про
Пенетрирующая полиуретановая грунтовка
ПодробнееЦИНЭП®
Цинкнаполненная эпоксидная грунтовка
ПодробнееЦИНОТЕРМ®
Термостойкая цинкнаполненная кремнийорганическая композиция
ПодробнееЦИНОТАН®
Цинкнаполненная полиуретановая композиция
ПодробнееЦИНОЛ®-СВ
Цинкнаполненная композиция на основе высокомолекулярного синтетического полимера
ПодробнееЦИНОЛ®
Цинкнаполненная композиция на основе высокомолекулярного синтетического полимера
ПодробнееЦВЭС®-МО
Цинкнаполненная этилсиликатная грунтовка для межоперационной защиты
ПодробнееЦВЭС®-А
Композиция защитно-фрикционная
ПодробнееЦВЭС®
Цинкнаполненная композиция на основе этилсиликатного связующего
ПодробнееЦВЭС®-SP
Межоперационная грунтовка (shop-primer)
ПодробнееТипы антикоррозионных покрытий и их применение
Введение В этой главе рассматриваются основные типы покрытий, которые в настоящее время доступны для использования, и содержится общая информация о составе покрытий. Он предназначен для предоставления основной информации о покрытиях и не является исчерпывающим руководством по выбору антикоррозионных покрытий. Если требуется информация о конкретном продукте или покрытиях, подходящих для определенных областей, следует проконсультироваться с производителем покрытия.
Покрытия часто делятся на две большие категории:
1) продукты для применения в новостройках и;
2) продукты, подходящие для технического обслуживания и ремонта, которые будут включать как капитальный ремонт, так и техническое обслуживание на борту (OBM).
Типы антикоррозионных покрытий, используемых для OBM, часто представляют собой однокомпонентные продукты, поскольку это позволяет избежать трудностей, связанных с измерением и смешиванием небольших количеств двухупаковочных продуктов, хотя небольшие количества двухупаковочных продуктов иногда доступны от производителей красок.Ремонт, проводимый экипажем находящихся в эксплуатации судов, редко бывает успешным в долгосрочной перспективе из-за трудностей с подготовкой поверхностей к достаточно высоким стандартам.
Как правило, краски предназначены либо для определенных участков резервуаров и для определенных функций для достижения наилучших характеристик, либо доступны универсальные покрытия для всех областей с компромиссными характеристиками. Во всех случаях необходимо соблюдать баланс между стоимостью, производительностью и сложностью обслуживания. Например, антикоррозионные покрытия, используемые на внешней стороне жилого помещения, имеют другие требования к характеристикам, чем антикоррозионные краски, используемые в балластных танках морской воды, поскольку коррозионное напряжение, оказываемое на последние, намного выше.Балластные цистерны также намного сложнее обслуживать из-за трудностей доступа, и поэтому использование высокоэффективного (и часто более дорогого) покрытия предпочтительнее для поддержания стали в хорошем состоянии.
Напротив, трюмы навалочных судов страдают от абразивного износа из-за удара груза и повреждения захвата, что часто приводит к коррозии. Грузовые трюмы, используемые в качестве балластных танков в тяжелую погоду, могут быть особенно восприимчивыми к коррозии в местах повреждения, и для этого грузового трюма иногда используется другое покрытие. Это также относится к грузовым танкам для нефтеналивных судов с обозначением класса «Чистые продукты», где любой грузовой танк может использоваться для тяжелого погодного балласта.
Состав краски
Краска может быть описана как жидкий материал, который можно наносить или растекать по твердой поверхности, на которой он впоследствии высыхает или затвердевает с образованием сплошной клейкой пленки. Краски в основном состоят из трех основных компонентов и множества добавок, которые включены в незначительных количествах. Основные компоненты:
• Связующее (также называемое наполнителем, средой, смолой, пленкой или полимером)
• Пигмент и наполнитель
• Растворитель
Из них , только первые два образуют окончательную сухую пленку краски. Растворитель необходим только для облегчения нанесения краски и начального образования пленки, но неизбежно, что на практике всегда остается некоторое количество растворителя в зависимости от уровня вентиляции.
Связующие — это пленкообразующие компоненты краски, которые определяют основные характеристики покрытия, как физические, так и химические. Краски обычно называются по их связующему компоненту (например, эпоксидные краски, краски на основе хлорированного каучука, алкидные краски и т. Д.). Связующее образует прочную непрерывную пленку, которая отвечает за адгезию к поверхности и способствует общей стойкости покрытия к окружающей среде.Связующие, используемые при производстве красок, делятся на два класса: термореактивные и термопластичные. После высыхания термореактивное покрытие будет отличаться по химическому составу от краски в банке. После отверждения на термоотверждающиеся покрытия не действуют растворители.
В случае термопластичного покрытия сухая пленка и влажная краска различаются только содержанием растворителя и химическим составом, они остаются практически одинаковыми. Если первоначально использованный растворитель наносится на термопластичное покрытие, оно размягчается и может быть повторно растворено в этом растворителе.
Эти покрытия обычно поставляются в двух отдельных упаковках, которые смешиваются вместе непосредственно перед нанесением. В жидких красках, где используется растворитель, сушка считается двухэтапным процессом. Обе стадии на самом деле происходят вместе, но с разной скоростью.
Этап первый: растворитель уходит из пленки при испарении, и пленка становится сухой на ощупь. Этап 2: Пленка постепенно становится более химически сложной с помощью одного из следующих четырех методов:1) Реакция с кислородом воздуха, известная как окисление.
2) Реакция с добавлением химического отвердителя.
3) Реакция с водой (влажность в атмосфере).
4) Искусственное отопление.
Это преобразование краски известно как высыхание или отверждение. Пленки, сформированные указанными выше способами, химически отличаются от исходных связующих и не будут повторно растворяться в исходном растворителе.
Эти смолы особенно важны, и их разработка для использования в качестве связующих была одним из наиболее значительных достижений в технологии антикоррозионных покрытий.Скорость сшивания или отверждения зависит от температуры. Ниже 5 ° C скорость отверждения стандартных эпоксидных смол значительно снижается, и для получения оптимальных свойств пленки необходимо полное отверждение. Эпоксидные смолы со специальными отвердителями затвердевают или застывают при температуре до –5 ° C. Важно строго соблюдать рекомендации производителя покрытия по температуре нанесения, чтобы покрытия были эффективными в эксплуатации.
Выбор отвердителя очень важен, так как в случае основы он определяет свойства пленки.Существует широкий выбор как смол, так и отвердителей, что позволяет создавать продукты, подходящие для большинства областей применения. Эпоксидные смолы используются как под водой, так и над водой и демонстрируют хорошую стойкость ко многим морским средам, включая катодную защиту с использованием цинка или других анодов, но они имеют тенденцию к мелу на солнечном свете. Этот процесс происходит, когда связующее разрушается ультрафиолетовым светом с образованием рыхлой и рыхлой поверхности, а частицы пигмента остаются на поверхности.
Это полимеры, образующиеся в результате реакции между гидроксильными соединениями и соединениями, содержащими изоцианаты. В двухкомпонентных системах специальная полиэфирная или полиэфирная смола со свободными гидроксильными группами реагирует с высокомолекулярным изоцианатным отвердителем. Возможная проблема с этими материалами заключается в их чувствительности к воде при хранении и применении. Транспортировка и хранение должны производиться в строгом соответствии с рекомендациями производителей.Из-за их плохих свойств отверждения при низких температурах при нанесении необходимо соблюдать рекомендации производителя.
Полиуретановые смолы обладают превосходной химической стойкостью и стойкостью к растворителям и превосходят стандартные эпоксидные смолы по кислотостойкости. Эпоксидные смолы более устойчивы к щелочам, чем полиуретаны. Полиуретановые финишные покрытия очень твердые и обладают очень хорошим блеском, сохранением блеска и могут не желтеть. Однако в некоторых случаях на них может быть трудно нанести следующий слой после старения, и для достижения оптимальной адгезии требуются очень чистые поверхности.Изоцианатный отвердитель также представляет потенциальную опасность для здоровья при распылении, которую можно преодолеть с помощью соответствующих средств защиты.
Алкидные смолы Алкидные смолы образуются в результате реакции между специальной органической кислотой (например, фталевой кислотой), специальным спиртом (например, глицерином или пентаэритритом) и растительным маслом или его жирными кислотами. Конечные свойства алкидных масел зависят от процентного содержания масла (называемого «маслянистость»), а также от используемых спирта и органической кислоты.
Эти типы включают силикаты, которые почти всегда используются в сочетании с цинковой пылью. Существуют неорганические силикаты на водной основе на основе силиката лития, калия или натрия и неорганические силикаты на основе растворителей, обычно основанные на этилсиликате.Покрытия на основе этих смол очень твердые, коррозионно-стойкие и термостойкие. Они требуют хорошей подготовки поверхности и часто ремонтируются с использованием органических покрытий. Цинк в неорганических смолах может растворяться в кислотных или щелочных условиях, но покрытия хорошо работают при нейтральном pH и часто используются в качестве покрытий для резервуаров.
Термопластические покрытия Эти типы связующих для красок представляют собой простые растворы различных смол или полимеров, растворенных в подходящих растворителях, и обычно поставляются в виде одной упаковки, что делает их особенно подходящими для работ по техническому обслуживанию. Сушка происходит просто за счет потери растворителя при испарении. Это называется физической сушкой, поскольку никаких химических изменений не происходит. Таким образом, полученная пленка всегда легко растворяется в исходном растворителе и также может размягчаться при нагревании. Поскольку эти покрытия по определению требуют наличия значительных количеств растворителя, они исчезают с рынков, где регулируется содержание летучих органических соединений, особенно в США и ЕС. Общие типы связующих в этой категории включают:
Хлорированные каучуковые смолы обладают хорошей кислотостойкостью и водостойкостью на хорошо подготовленных поверхностях.Их температурная чувствительность может привести к различным дефектам пленки при использовании в очень жарком климате. Кроме того, белые и бледные цвета имеют ярко выраженную тенденцию к желтизне при воздействии яркого солнечного света. Краски на основе хлорированного каучука высыхают при низких температурах и обеспечивают хорошую межслойную адгезию как в свеженанесенных, так и в старых системах, что делает их пригодными для технического обслуживания.
Виниловые смолы основаны на пленкообразующих полимерах, состоящих из поливинилхлорида, поливинилацетата и поливинилового спирта в различных соотношениях.Используемые типы пластификаторов — трикрезилфосфат или диоктилфталат. Твердые материалы большего объема могут быть получены путем смешивания виниловой смолы с другими материалами, такими как акриловые смолы. Обычно свойства пленки и погодоустойчивые характеристики также показывают хорошие характеристики сушки при низких температурах и межслойной адгезии. Каменноугольная смола может быть добавлена для повышения водостойкости.
Пигменты и наполнителиПигменты и наполнители используются в красках в виде тонких порошков.Они диспергированы в связующем до размеров частиц примерно 5-10 микрон для отделочных красок и примерно 50 микрон для грунтовок.
Антикоррозийные пигменты (1) Цинк Металлический цинк широко используется в грунтовках, придающих коррозионную стойкость стали. Первоначальная защита — гальваническое воздействие. Однако по мере того, как покрытие подвергается воздействию атмосферы, происходит постепенное накопление продуктов коррозии цинка, в результате чего образуется непроницаемый барьер с небольшой гальванической защитой или без нее.Чтобы обеспечить хорошую гальваническую и барьерную защиту, требуется высокий уровень цинка, около 85% цинка в сухой пленке по весу. В качестве смол можно рассматривать эпоксидные смолы и силикаты. Очевидно, что для правильного функционирования цинк должен находиться в тесном контакте со стальной подложкой, и поэтому важна хорошая чистота поверхности перед нанесением.
Металлические алюминиевые чешуйки обычно используются в качестве антикоррозионных пигментов и действуют как антикоррозионные средства, создавая обходной путь для воды и ионов вокруг пластинчатых чешуек, а также поглощая кислород для дают оксиды алюминия, которые блокируют поры в покрытии.Там, где алюминий находится в контакте со сталью, также будет действовать ограниченный механизм катодной защиты, хотя при использовании на танкерах и продуктовозах содержание алюминия в сухой пленке не должно превышать 10 процентов, чтобы избежать возможной опасности искры при скоплении горючих газов.
Это также широко используемый антикоррозийный пигмент, и считается, что при нормальных условиях воздействия защита обеспечивается барьерным эффектом, поскольку для обеспечения адекватной защиты от коррозии необходимы высокие уровни пигментации. охрана.Фосфат цинка может быть включен практически в любое связующее, и из-за его низкой непрозрачности или прозрачности можно производить краски любого цвета.
Барьерные пигменты Наиболее распространенными типами этих пигментов являются алюминий (листовой алюминий) и слюдяной оксид железа (MIO). Оба имеют форму частиц, которые называются пластинчатыми (пластинчатыми). Эти материалы можно использовать в сочетании, при этом алюминий осветляет почти черный оттенок MIO. Пигментированные пленки MIO обладают долговечностью, но для достижения этого необходимы высокие уровни MIO, порядка 80% от общего пигмента.Алюминий уже много лет используется в качестве основного пигмента в красках. Пластинчатая форма делает пленку более водонепроницаемой. Стеклянные хлопья также используются в качестве барьерного пигмента.
Как следует из названия, они в основном регулируют или «расширяют» пигментацию краски до тех пор, пока не будет достигнута требуемая объемная концентрация пигмента (PVC). Пигменты-наполнители представляют собой неорганические порошки с различными формами и размерами частиц. Хотя они вносят незначительный вклад в непрозрачность цвета краски или не вносят ее вообще, они могут иметь значительное влияние на физические свойства. К ним относятся текучесть, степень блеска, противоосадочные свойства, способность к распылению, водо- и химическая стойкость, механическая прочность, твердость и твердость (твердый объем, задерживающая тиксотропия). Смеси наполнителей часто используются для получения желаемых свойств. Они относительно недороги по сравнению со смолами, антикоррозийными пигментами и красящими пигментами.
Растворители используются в красках в основном для облегчения нанесения. Их функция заключается в растворении связующего и снижении вязкости краски до уровня, который подходит для различных методов нанесения, таких как кисть, валик, обычное распыление, безвоздушное распыление и т. Д. После нанесения растворитель испаряется и не играет никакой роли. дальнейшая часть в финальной лакокрасочной пленке. Жидкости, используемые в качестве растворителей в красках, можно описать одним из трех способов:
(1) Настоящие растворители — жидкость, которая растворяет связующее и полностью с ним совместима.
(2) Скрытый растворитель — жидкость, которая не является настоящим растворителем. Однако при смешивании с настоящим растворителем смесь обладает более сильными растворяющими свойствами, чем один настоящий растворитель.
(3) Растворитель-разбавитель — жидкость, которая не является настоящим растворителем. Обычно используется как смесь со смесями истинный растворитель / скрытый растворитель для снижения стоимости.
Связующие допускают только ограниченное количество разбавителя. В лакокрасочной промышленности используется множество растворителей, отчасти это связано с рядом различных свойств, которые необходимо учитывать при выборе растворителя или смеси растворителей.Помимо коммерческих факторов, таких как цена и доступность, свойства включают токсичность, летучесть, воспламеняемость, запах, совместимость и пригодность. В некоторых странах использование некоторых типов растворителей запрещено. Это особенно верно в США, где Закон о вредных веществах, загрязняющих воздух (HAPS) определяет сроки удаления многих растворителей и наполнителей с покрытий. При реализации этого закона, скорее всего, будут затронуты свойства нанесения, время высыхания и окна перекрытия.
За некоторыми исключениями (например, противообрастающие краски, косметические эффекты, антипирены и т. Д.), Большинство покрытий, наносимых на сосуд, используется для защиты от коррозии. Существует много типов антикоррозионных покрытий, но эпоксидные краски обычно покрывают наибольшую площадь на судне, особенно когда они используются в балластных танках морской воды. В последние годы ведутся споры о терминологии, используемой для эпоксидных покрытий, и обычно используются следующие термины:
(1) Чистая эпоксидная смола
Чистые эпоксидные покрытия обычно рассматриваются как краски, содержащие только эпоксидные полимеры, сшивающий агент, пигменты, наполнители и растворители. Покрытия содержат большое количество эпоксидного связующего, и поэтому ожидается, что они обеспечат максимально возможные характеристики покрытия с точки зрения защиты от коррозии, длительного срока службы и низких эксплуатационных расходов. Кроме того, некоторые продукты также заявляют о стойкости к истиранию. В чистые эпоксидные покрытия можно добавлять другие пигменты, такие как алюминий, для обеспечения дополнительных антикоррозионных свойств. Эпоксидно-фенольные покрытия могут использоваться в грузовых танках, где требуется высокий уровень дополнительной устойчивости груза, например, на нефтепродуктах и химовозах.Особая осторожность требует подготовки поверхности; может потребоваться отверждение покрытия путем нагревания резервуаров. Производители покрытий сообщат конкретные требования для каждого резервуара.
(2) Модифицированная эпоксидная смола
Эта группа, также известная как эпоксидная мастика, не содержащая смол эпоксидная смола и отбеленная эпоксидная смола, охватывает широкий спектр продуктов и обеспечивает антикоррозионные свойства. В эксплуатации могут быть эффективны модифицированные эпоксидные смолы. Однако, поскольку существует множество возможных модифицированных эпоксидных составов, невозможно сделать какие-либо обобщения об их антикоррозионных характеристиках.Модифицированные эпоксидные смолы могут содержать неэпоксидные материалы, которые способны образовывать поперечные связи в конечную пленку. Они также могут содержать инертные материалы, твердые или жидкие, которые не участвуют в образовании пленки, но остаются в конечном покрытии как пигменты или наполнители. Если эти материалы растворимы в воде (или в грузе), они могут вымываться в течение длительного периода времени, оставляя пористую или хрупкую пленку с пониженными антикоррозийными свойствами.
(3) Каменноугольная смола Эпоксидная
Каменноугольная смола является продуктом природного происхождения.Угольные гудроны доступны в широком диапазоне типов от жидких до твердых. Включение каменноугольных смол в покрытие приводит к очень темно-коричневому или черному цвету покрытия, который может быть слегка осветлен добавлением пигмента в виде чешуек алюминия для более светлых красок. Однако маловероятно, что эпоксидные смолы из каменноугольной смолы будут достаточно светлыми для использования в соответствии с требованиями IMO PSPC 4.4 Таблица 1, пункт 1.2 для окончательного покрытия. Светлый верхний слой из эпоксидной смолы без содержания смолы может быть использован поверх первого слоя на основе смолы.Однако «просачивание» смолы может изменить цвет верхнего покрытия. Некоторые компоненты покрытия могут вымываться в течение длительного времени, в результате чего покрытие становится более хрупким и менее защищенным. Эпоксидные смолы каменноугольной смолы имеют длительный опыт эксплуатации и в целом хорошо себя зарекомендовали. С 1990-х годов они были выведены из эксплуатации в балластных цистернах из-за проблем со здоровьем и безопасностью нанесения покрытий, а также из-за рекомендаций по нанесению светлых покрытий для облегчения инспекций балластных танков.
(4) Эпоксидная смола, не содержащая растворителей
Краски, не содержащие растворителей (иногда называемые твердыми веществами на 100%), как следует из названия, формулируются и наносятся без необходимости в дополнительных растворителях, что позволяет преодолеть остатки растворителей в покрытии. Вязкость, необходимая для распыления краски, получается путем выбора низкомолекулярного сырья или путем нагрева и использования многокомпонентных систем. Типичные области применения включают балластные и грузовые танки. Иногда они используются там, где удаление летучих органических компонентов (ЛОС) затруднено из-за плохой вентиляции, хотя следует отметить, что ЛОС для систем без растворителей не обязательно равен нулю. Типичные области применения покрытий, не содержащих растворителей, включают внутреннюю часть трубопроводов, некоторые резервуары и другие области, где не может быть обеспечена соответствующая вентиляция, или для областей, где действуют строгие меры контроля выбросов летучих органических соединений.

Cortec Антикоррозионные материалы | ТАРТ, s.r.o.
Наша компания является эксклюзивным центральноевропейским дилером Cortec Corporation USA — мирового лидера в области инновационных решений для защиты материалов от коррозии. Мы предлагаем комплексную систему защиты продукции от коррозии, которая включает: антикоррозионных упаковочных материалов, антикоррозионные консерванты, чистящие и обезжиривающие средства, средства для удаления ржавчины, антикоррозионные добавки, антикоррозионные покрытия и ингибиторы мигрирующей коррозии. .
Уникальные решения для всех видов защиты от коррозии
ТАРТ, s. r.o. выполнила строгие условия лицензирования и, таким образом, стала единственным производителем продуктов CORTEC VpCI ® в Чешской Республике. Благодаря этому на чешский рынок выводятся новейшие технологии ведущих мировых компаний в области защиты от коррозии.
Cortec обеспечивают краткосрочную, среднесрочную или долгосрочную защиту от коррозии.Компания Cortec разработала новое поколение летучих ингибиторов коррозии (VCI) под названием VpCI ® (ингибитор коррозии паров / летучих фаз). Эти ингибиторы коррозии образуют молекулярный слой на поверхности черных и цветных металлов и надежно защищают его от коррозионного воздействия влажности SO 2 и H 2 S. Уникальность системы Cortec заключается в повышенном уровне давление ингибиторов, вытесняющих молекулы воздуха и воды с поверхности упакованного продукта.
Преимущества продукции Cortec:- высокая эффективность — долговременная защита от коррозии даже в экстремальных условиях
- простое приложение — широкий ассортимент продукции для индивидуальных приложений.
Простая защита даже в труднодоступных местах
- экологически чистый и пригодный для вторичной переработки — сертифицирован в соответствии с экологическим стандартом ISO
- без риска для здоровья человека — нетоксичны, не содержат тяжелых металлов, нитридов, силиконов, фосфатов и хлорированных углеводородов
Отправьте запрос на Demand @ tart.cz
4 типа металла, устойчивого к коррозии или не ржавеющего
Мы обычно думаем о ржавчине как о оранжево-коричневых хлопьях, которые образуются на открытой стальной поверхности, когда молекулы железа в металле реагируют с кислородом в присутствии воды с образованием оксидов железа. Металлы также могут реагировать в присутствии кислот или агрессивных промышленных химикатов. Если ничто не останавливает коррозию, чешуйки ржавчины будут продолжать отламываться, подвергая металл дальнейшей коррозии, пока он не распадется.
Ознакомьтесь с нашим ассортиментом коррозионно-стойких металлов на IMS!
Не все металлы содержат железо, но они могут вызвать коррозию или потускнение в других окислительных реакциях. Чтобы предотвратить окисление и разрушение металлических изделий, таких как поручни, резервуары, приборы, кровля или сайдинг, вы можете выбирать металлы, которые являются «нержавеющими» или, точнее, «коррозионно-стойкими». В эту категорию попадают четыре основных типа металлов:
Нержавеющая сталь
Типы нержавеющей стали, такие как 304 или 316, представляют собой смесь элементов, и большинство из них содержат некоторое количество железа, которое легко окисляется с образованием ржавчины.Но многие сплавы нержавеющей стали также содержат высокий процент хрома — не менее 18 процентов — который даже более активен, чем железо. Хром быстро окисляется, образуя защитный слой оксида хрома на поверхности металла. Этот оксидный слой противостоит коррозии и в то же время предотвращает попадание кислорода в нижележащую сталь. Другие элементы сплава, такие как никель и молибден, повышают его устойчивость к ржавчине.
Алюминий металлический
Многие самолеты изготавливаются из алюминия, а также детали автомобилей и велосипедов.Это связано с его небольшим весом, а также с устойчивостью к коррозии. Алюминиевые сплавы почти не содержат железа, а без железа металл не может ржаветь, но окисляется. Когда сплав подвергается воздействию воды, на поверхности быстро образуется пленка оксида алюминия. Слой твердого оксида довольно устойчив к дальнейшей коррозии и защищает лежащий под ним металл.
Посмотреть изделия из металла на IMSМедь, бронза и латунь
Эти три металла содержат мало железа или совсем не содержат железа, поэтому не ржавеют, но могут вступать в реакцию с кислородом.Медь со временем окисляется, образуя зеленую патину, которая фактически защищает металл от дальнейшей коррозии. Бронза — это смесь меди и олова, а также небольшого количества других элементов, и, естественно, она гораздо более устойчива к коррозии, чем медь. Латунь — это сплав меди, цинка и других элементов, который также устойчив к коррозии.
Оцинкованная сталь
Оцинкованная сталь ржавеет долго, но со временем она ржавеет. Это углеродистая сталь, оцинкованная или покрытая тонким слоем цинка.Цинк действует как барьер, не позволяющий кислороду и воде достигать стали, поэтому она защищена от коррозии. Даже если цинковое покрытие поцарапано, оно продолжает защищать близлежащие участки лежащей под ним стали за счет катодной защиты, а также за счет образования защитного покрытия из оксида цинка. Как и алюминий, цинк обладает высокой реакционной способностью к кислороду в присутствии влаги, а покрытие предотвращает дальнейшее окисление железа в стали.
Industrial Metal Supply предлагает широкий ассортимент нержавеющих металлов для различных областей применения.
Ваш местный поставщик металла, обслуживающий Южную Калифорнию, Аризону и Северную Мексику
Industrial Metal Supply — крупнейший в Саутленде поставщик всех видов металла и аксессуаров для металлообработки, включая средства защиты от ржавчины.
Как правильно выбрать коррозионно-стойкий материал
Как правильно выбрать антикоррозийный материал
Выбор материала — важная часть любого производственного процесса.Выбор правильного материала очень важен, потому что этот материал определяет химические и механические свойства производимого компонента, может значительно повлиять на долговечность компонента и обеспечить его правильное функционирование. Коррозионно-стойкие материалы играют важную роль в производстве из-за их свойств материала и отсутствия реакционной способности к суровым условиям окружающей среды и химическим веществам.
Например, многие аэрокосмические компоненты производятся из титана, вольфрама и углеродного волокна, потому что эти материалы очень прочные, но легкие и гибкие.К сожалению, эти материалы могут вступать в реакцию друг с другом и со временем вызывать гальваническую коррозию, локализованную коррозию, при которой происходит обмен ионами между материалами. Здесь коррозионно-стойкие материалы сохраняют целостность деталей в одной из самых строго регулируемых отраслей в мире.
С экологической точки зрения экологически чистые источники солнечной и ветровой энергии уязвимы в суровых условиях, а коррозионно-стойкие материалы помогают защитить их критически важные компоненты от повреждений с течением времени.Это помогает производителям безопасно создавать компоненты для альтернативных источников энергии и вносить вклад в более устойчивую экономику. Для инженеров, которые хотят защитить свои детали от агрессивных сред, таких как кислоты и соли, или от ультрафиолетового излучения, вот лучшие коррозионно-стойкие материалы, которые следует рассмотреть.
Примеры коррозионностойких материалов
1. Нержавеющая сталь
Сплавы нержавеющей стали известны своей стойкостью к коррозии, пластичностью и высокой прочностью.Коррозионно-стойкие свойства нержавеющих сталей напрямую связаны с содержанием в них хрома и никеля — большее количество этих элементов коррелирует с повышенной стойкостью.
Большинство сплавов нержавеющей стали, представленных сегодня на рынке, содержат не менее 18% хрома. Когда хром окисляется, он образует защитный слой оксида хрома на поверхности металлической детали, который предотвращает коррозию и не позволяет кислороду достигать подлежащей стали.
Нержавеющая сталь находит широкое применение: от кухонных приборов, таких как кастрюли и сковороды, до автомобильных запчастей и хирургических имплантатов.Поскольку этот материал имеет высокую температуру плавления и может выдерживать и выдерживать высокое давление, он также хорошо подходит для строительства, машиностроения и изготовления контейнеров для хранения. Нержавеющая сталь 304, 430 и 316 является наиболее часто определяемой маркой нержавеющей стали, при этом марка 316 является предпочтительной для суровых морских условий.
Тем не менее, долговечность и высокая коррозионная стойкость нержавеющей стали достигаются за высокую цену, что делает их непомерно дорогими для некоторых производителей. Кроме того, со сплавами нержавеющей стали может быть трудно работать, особенно при сварке, из-за их высокой температуры плавления.
2. Алюминий
Алюминиевые сплавы нетоксичны, на 100% пригодны для вторичной переработки, имеют высокое отношение прочности к массе, обладают высокой теплопроводностью и электропроводностью и легко поддаются механической обработке. Кроме того, алюминий уникален, потому что это один из немногих материалов, обладающих естественной устойчивостью к коррозии.
Этот материал практически не содержит железа, поэтому не может ржаветь, но может окисляться.Когда алюминиевый сплав подвергается воздействию воды и окисляется, что называется самопассивацией, на поверхности детали образуется пленка оксида алюминия, которая защищает ее от коррозии. Алюминий 5052-h42 более устойчив к коррозии, чем другие разновидности алюминия, и имеет яркую гладкую поверхность.
Этот процесс окисления также можно тщательно контролировать с помощью процесса, называемого анодированием. Кроме того, алюминий уникален, потому что это один из немногих инновационных материалов для аддитивного производства, которые обладают естественной устойчивостью к коррозии.Анодирование — это недорогая контролируемая отделка, которая широко используется. Этот процесс также позволяет добавлять цвет к детали, что позволяет дополнительно настраивать ее для различных вариантов использования.
Алюминий часто используется в аэрокосмической промышленности, автомобильных панелях, чувствительных к соленой воде приложениях и других ситуациях, когда требуется высококачественный материал. Производители должны рассмотреть возможность использования алюминия, если им нужен доступный по цене устойчивый к коррозии материал, помня при этом, что производство алюминия может быть беспорядочным и хлопотным в работе.
3. Мягкие металлы
Мягкие металлы или красные металлы включают коррозионно-стойкие материалы, такие как медь и ее сплавы, латунь и бронза. Медь пластична, пластична и отлично проводит тепло и электричество. Эти металлы могут обеспечить коррозионную стойкость на протяжении всего жизненного цикла данного компонента. . Медь со временем не подвергается коррозии; при окислении образует зеленый внешний слой, называемый патиной, который защищает деталь от дальнейшей коррозии.
Медь также играет ключевую роль в производстве деталей для систем возобновляемой энергии. Поскольку медь является отличным проводником тепла и электричества, системы, работающие на меди, передают энергию более эффективно и с меньшим воздействием на окружающую среду.
4. Полипропилен
Металлы — не единственные доступные коррозионно-стойкие материалы. Полипропилен — один из самых популярных пластиков в обрабатывающей промышленности, особенно часто используемый для производства автомобильных запчастей. Это также один из самых устойчивых к коррозии пластиков.
Эту термопластичную полимерную смолу прозвали «сталью пластмассовой промышленности» за ее прочность, способность выдерживать высокие уровни физического давления и устойчивость к широкому спектру коррозионных элементов, таких как масло, растворители, вода, бактерии и т. Д. .Полипропилен высокой плотности (HDPE) обеспечивает более высокую прочность на разрыв и расширенный диапазон рабочих температур.
Полипропилен можно найти практически во всем — в веревках, ковровых покрытиях, автомобильных аккумуляторах, многоразовых контейнерах, спортивной одежде, лабораторном оборудовании и многом другом. Однако высокая воспламеняемость и высокий тепловой коэффициент этого материала ограничивают его пригодность для применения в условиях высоких температур. Также важно отметить, что полипропилен подвержен окислению, разложению под действием УФ-излучения и некоторым хлорированным растворителям.
5. Политетрафторэтилен (ПТФЭ)
ПТФЭ, обычно именуемый торговой маркой Тефлон, представляет собой химический и коррозионно-стойкий технический термопласт с самым низким коэффициентом трения среди всех известных твердых материалов. ПТФЭ гидрофобен, что означает, что он не впитывает воду, и обладает хорошей электроизоляционной способностью как в горячей, так и во влажной среде.
ПТФЭ наиболее известен своим коммерческим и медицинским применением — он создает антипригарные покрытия для кастрюль и сковородок и обеспечивает антифрикционное покрытие для медицинских и промышленных применений.Благодаря низкому трению этот материал используется для производства подшипников, шестерен, пластин скольжения, уплотнений и других мелких деталей, которые имеют решающее значение для промышленного применения. PTFE также часто используется в композитах из углеродного волокна и стекловолокна.
Тем не менее, у ПТФЭ есть свои ограничения. Этот материал трудно соединить, он чувствителен к ползучести, истиранию и радиации. Кроме того, пары, выделяемые ПТФЭ, могут быть токсичными в закрытых помещениях. Прежде чем принимать какие-либо важные решения по материалам, лучше проконсультироваться с опытным партнером-производителем.
Получите консультацию специалиста по выбору материалов
Коррозионная стойкость — чрезвычайно желательная характеристика, особенно в полупроводниковой, энергетической, аэрокосмической и автомобильной промышленности. На выбор предлагается широкий спектр коррозионно-стойких материалов, включая вышеупомянутые пять, и продуктовые группы должны проявлять должную осмотрительность при выборе материалов, чтобы убедиться, что они выполняют свои уникальные проектные требования.
Опытный партнер по цифровому производству, такой как Fast Radius, может помочь группам разработчиков ответить на самые сложные вопросы в процессе разработки продукта. Что лучше: металл или пластик? Полипропилен так же хорош, как нержавеющая сталь? Наша команда имеет многолетний опыт работы с аддитивным и традиционным производством, и мы поможем каждому клиенту выбрать коррозионно-стойкий материал, который надолго защитит их детали. Свяжитесь с нами сегодня чтобы начать.
Для получения дополнительной информации о материалах в аддитивном производстве и о том, как выбрать лучший из них для вашего следующего проекта, ознакомьтесь с соответствующими статьями блога в центре обучения Fast Radius.
Антикоррозионные покрытия — Области применения и типы
Твердые металлические поверхности, а иногда и неметаллы защищаются путем нанесения антикоррозионных покрытий. Чтобы правильно выбрать систему защиты от коррозии, необходимо определить характеристики коррозионной среды, которая угрожает вашим активам, нуждающимся в защите, таким как здания, мосты, транспортные средства, заводское оборудование, корабли и трубопроводы. Окружающая среда, в которой требуются эти покрытия, может быть сельской, городской или в таких областях, как открытая атмосфера, под землей, под почвой. Эти покрытия также могут использоваться в горнодобывающей, морской или промышленной отраслях. В Secoa Technology мы предлагаем ряд антикоррозионных покрытий, которые могут помочь вам обеспечить важную защиту ваших промышленных активов.
Выбор одного или нескольких антикоррозионных покрытий должен основываться на самом материале основы, а также на типах условий, в которых материал будет находиться в полевых условиях.
Опции защиты от коррозии
Мы предлагаем различные виды продукции для защиты деталей от веществ, вызывающих коррозию, таких как химические вещества, вода и воздух. Некоторые из этих антикоррозионных покрытий включают:
Plascoat
Вместо использования нержавеющей стали Plascoat можно наносить на стандартную сталь для обеспечения необходимой защиты от коррозии. Это оптимальный выбор для применения в архитектурной, коммунальной и пищевой промышленности.
Нейлон
В различных областях применения можно эффективно использовать нейлоновое полимерное покрытие.Он используется для обеспечения эффективной устойчивости промышленного оборудования к коррозии. В автомобильной, медицинской и ИТ-отраслях используются нейлоновые порошковые покрытия. В частности, мы предлагаем покрытие Rilsan ® Nylon 11 для эффективных результатов.
Эпоксидная
Независимо от того, используются ли водяные клапаны или очистка сточных вод, эпоксидное антикоррозионное порошковое покрытие идеально подходит для тонких и тяжелых конструкций.
Прочие полимеры
Полимерные покрытия эффективны для различных промышленных применений.Они известны своими антикоррозийными и прочными характеристиками. Применения, которые включают насосы, трубопроводы, предложения и клапаны, могут выиграть от этих покрытий. В частности, некоторые из наших продуктов включают PFA, PTFE, Halar, KF Polymer и ETFE.
Если вам нужна защита от коррозии для ваших продуктов или оборудования от химикатов или других элементов, мы можем предоставить антикоррозионные покрытия, которые могут выполнить свою работу.
Для получения дополнительной информации о том, как мы можем удовлетворить ваши потребности в антикоррозийном покрытии, позвоните нам сегодня по телефону 706.272.0133 или заполните нашу контактную форму.
Антикоррозийное покрытие | Антикоррозийное покрытие для стали | Антикоррозийные покрытия
Антикоррозийное покрытие | Антикоррозийное покрытие для стали | Коррозионно-стойкие покрытия | Secoa TechnologyУлучшенные антикоррозионные покрытия
Наши антикоррозионные средства можно использовать по-разному; это включает горячее флокирование, электростатический слой, псевдоожиженный слой и множество фторполимеров (высокоструктурные влажные покрытия).Наша текущая линейка антикоррозионных и химических продуктов включает:
Полиэстер
Современные полиэфирные порошковые покрытия обеспечивают исключительную защиту от коррозии и ультрафиолетового излучения, имеют сравнительно низкую стоимость и доступны в широком спектре цветов. Хотя полиэстер по своей природе устойчив к коррозии, его характеристики могут быть улучшены за счет сочетания его с цинковой или эпоксидной грунтовкой.
Рилсан ® нейлон 11
Технический полимер с высокими эксплуатационными характеристиками.Полученный в результате ряда сложных химических операций, это один из немногих существующих полимеров, производимых из «зеленого» сырья. Эта система заслужила статус предпочтительного материала в самых требовательных областях применения, во многом благодаря превосходному сочетанию тепловых, физических, химических и механических свойств. Он имеет диапазон толщины от 0,005 дюйма до 0,050 дюйма.
Эпоксидный
Может использоваться для обработки отходов, водяных клапанов и других металлических покрытий, от тонких до тяжелых
Термопласты высокой конструкции
Может применяться для обработки стали в качестве замены нержавеющей стали, что делает ее идеальной для коммунальной, архитектурной и пищевой промышленности. Отличные УФ-свойства.
Халар (ECTFE)
Частично фторированный полукристаллический полимер, который обеспечивает универсальность, обеспечивая при этом проницаемость, химическую и термическую стойкость.
ЭТФЭ
Термопластический сополимер, полученный в результате полимеризации мономеров этилена и тетрафторэтилена. Эти материалы чрезвычайно прочны и устойчивы к истиранию, обладают превосходной химической стойкостью и непрерывными рабочими температурами до 150 ° C (302 ° F).ETFE также является отличным электроизолятором, обладает хорошими антипригарными свойствами и низким коэффициентом трения.
Рубиново-красный PFA
Версия порошкового покрытия PFA, в котором используются наполнители для создания почти непроницаемого слоя защиты. Этот продукт следует учитывать всякий раз, когда считается, что проницаемость представляет собой значительный риск для характеристик обычных фторполимерных покрытий.
Коррозионно-стойкие покрытия для многих областей применения
Если вам нужно профессиональное решение для вашей промышленной обработки металла, мы можем помочь.Имея за плечами многолетний опыт, мы можем выполнить широкий спектр вариантов антикоррозионного покрытия. Если вы ищете антикоррозийное покрытие для стали, мы сделаем вашу работу.
Наши услуги по нанесению металлических покрытий включают антикоррозионные и антикоррозийные покрытия, а также ряд других вариантов. Мы предлагаем высококачественные варианты различных металлических покрытий по конкурентоспособным ценам, обеспечивая исключительное качество и стоимость заказов любого размера.
Стальное покрытие помогает защитить его от повреждений, которые может вызвать длительный контакт с водой.Вода может не только повредить компоненты, но и снизить производительность, увеличивая вероятность отказа в решающий момент. Мы можем предоставить антикоррозийное покрытие для стали, обеспечивающее необходимую защиту, позволяющую вашему продукту хорошо работать даже в сложных условиях.
Чтобы узнать больше или обсудить свои требования к
, позвоните нам по телефону Этот веб-сайт использует файлы cookie для улучшения вашего опыта. Мы надеемся, что это не проблема, но вы можете отказаться, если хотите.Настройки файлов cookie ПРИНЯТЬПолитика конфиденциальности и использования файлов cookie
Покрытия для защиты от коррозии — Промышленные антикоррозионные покрытия
Необработанные компоненты часто подвергаются той или иной форме коррозии, которая может негативно повлиять на производственные возможности, привести к потере ценных ресурсов, вызвать загрязнение и ограничить удобство использования. Увеличьте срок службы материалов с помощью высокоэффективных антикоррозионных покрытий Delta Coatings.
Преимущества покрытия, устойчивого к коррозии
Антикоррозийные покрытия могут помочь предотвратить деградацию материала, вызванную окислением, влажностью и химическим воздействием, среди прочего. Они действуют как барьер, предотвращающий контакт между агрессивными материалами и химическими соединениями. Дополнительные преимущества антикоррозионных покрытий:
- Защита от ржавления
- Тепловая защита
- Защита от эрозии
- Сопротивление адгезии
Применение покрытий, устойчивых к коррозии
Delta Coatings — ведущий поставщик покрытий и футеровок для промышленного применения для нефтегазовой отрасли, альтернативной энергетики, очистки сточных вод, полупроводников и химической обработки.Наша команда сочетает в себе многолетний опыт с инновационными технологиями, чтобы ваши активы работали без коррозии.
Мы предлагаем широкий спектр антикоррозионных покрытий, специально разработанных для обеспечения превосходной элементарной защиты материалов, используемых в суровых условиях. В нашей линейке антикоррозионных покрытий
- Xylan®
- Эпоксидная
- ПТФЭ
- PPS / Ryton®
- FEP
- PVDF / Dykor®
- ECTFE / Halar®
- ЭТФЭ
- PFA
Хотя все эти покрытия защищают от коррозии, они производятся из разного сырья и обеспечивают разный уровень эксплуатационных характеристик и устойчивости.
Типы покрытий, устойчивых к коррозии
Ксилан®
ПокрытияXylan® — это семейство фторполимерных покрытий, предназначенных для предотвращения коррозии компонентов оригинального оборудования (OEM). Покрытия Xylan®, изготовленные из износостойких фторполимерных композитов с низким коэффициентом трения и армирующих связующих смол, обычно наносятся в виде тонких пленок.
Эпоксидная
Эпоксидная смола обеспечивает быстросохнущее, прочное и защитное покрытие. Он создается в результате химической реакции с использованием эпоксидной смолы и полиминового отвердителя.Когда эти два химиката объединяются, жидкое эпоксидное покрытие становится прочным и долговечным, устойчивым к высоким температурам и химическим воздействиям.
ПТФЭ
Политетрафторэтилен, или ПТФЭ, представляет собой синтетический фторполимер, полученный из тетрафторэтилена. Это покрытие является инертным и прочным, что позволяет ему противостоять коррозии и уменьшать трение и износ. Он широко используется в трубопроводах, трубной продукции и нефтехимии.
PPS / Ryton®
Составыполифениленсульфида Ryton® или PPS обладают улучшенной термической стабильностью, химической стойкостью, стабильностью размеров и огнестойкостью.Полифенилен Ryton®, созданный из чередующихся атомов серы и фениленовых колец, имеет исключительно высокий модуль упругости и сопротивление ползучести, а также может выдерживать широкий спектр агрессивных химических сред.
ФЭП
Антипригарные покрытия из фторированного этиленпропилена или FEP плавятся и растекаются во время выпечки, образуя гладкие пленки с превосходной стойкостью к истиранию. Непористое покрытие обладает высокой химической стойкостью, не смачивает и имеет очень низкий коэффициент трения.Это покрытие обладает отличными антиадгезионными свойствами и часто используется в качестве антиадгезионного покрытия. FEP идеально подходит для антипригарных, устойчивых к коррозии и химически стойких применений. Другое использование включает в себя обожженную облицовку для покрытия резервуаров.
PVDF / Dykor®
ПокрытияDYKOR® PVDF могут наноситься на большинство металлических поверхностей и обеспечивают исключительную химическую, коррозионную и ультрафиолетовую стойкость. Этот тип покрытия, производимый путем комбинирования смол из поливинилидена или ПВДФ и таких наполнителей, как графит и слюда, обладает превосходной стойкостью к большинству растворителей и химикатов.Общие области применения включают полупроводниковую, медицинскую и химическую промышленность.
ECTFE / Halar®
Halar® ECTFE — это частично фторированный полукристаллический полимер, который обеспечивает превосходную химическую, проницаемость и огнестойкость. Другие характеристики включают низкую проницаемость, отличную атмосферостойкость и отличную стойкость к истиранию. Это покрытие часто используется в качестве футеровки в антикоррозионных устройствах, таких как трубопроводы. Улучшенные свойства огнестойкости и химической стойкости делают Halar® ECTFE идеальным для применения в проводах и кабелях.
ЭТФЭ
Этилентетрафторэтилен, или ETFE, представляет собой частично фторированный сополимер этилена и тетрафторэтилена. Это покрытие обладает превосходной ударной вязкостью, истиранием и сопротивлением порезам, улучшая его способность противостоять физическому насилию. ETFE подходит для рабочих колес насосов или движущихся частей оборудования, работающих в химически агрессивных средах.
PFA
Перфторалкокси, или PFA, обладает хорошими механическими свойствами и обрабатываемостью в расплаве без ущерба для тепловых характеристик и химической стойкости.Покрытие этого типа химически инертно, имеет очень низкий коэффициент трения, устойчиво к ультрафиолетовому излучению и одобрено Управлением по санитарному надзору за качеством пищевых продуктов и медикаментов США. Его часто используют, когда требуются ясность, гибкость и более высокий непрерывный диапазон рабочих температур.