9100700001 Антикор серый 1л 910 BODY — 9100700001 BODY
9100700001 Антикор серый 1л 910 BODY — 9100700001 BODY — фото, цена, описание, применимость. Купить в интернет-магазине AvtoAll.Ru Распечатать14
1
Артикул: 9100700001еще, артикулы доп.: BODYскрыть
Код для заказа: 030386
Есть в наличииДоступно для заказа — >10 шт.Данные обновлены: 02.04.2021 в 04:30
Код для заказа 030386 Артикулы 9100700001, BODY Производитель BODY Ширина, м:Описание
Антикор BODY-910 (серый) 1 кг .
Тиксотропный материал на основе битума с отличными антикоррозионными и антигравийными свойствами.
Подходит для нанесения на колесные арки, днище автомобиля и т.д.
Состав имеет прекрасную адгезию, быстро сохнет и может быть окрашен любыми типами красок.
Наносится кистью или пистолетом под давлением 5-6 бар, может разбавляться на 10-20% нитроразбавителем.
В упаковке 6 шт.
Масса 1 кг.
Страна-производитель: (Греция)
Отзывы о товаре
Сертификаты
Обзоры
Статьи о товаре
- Антикоррозийная обработка — лучшая защита автомобиля от ржавчины 8 Мая 2013
Одним из страшнейших врагов металла является коррозия. Даже приобретая дорогую иномарку, не говоря уже об отечественных автомобилях, необходимо сразу же позаботиться об антикоррозийной защите. Действительно, кузов начинает разрушаться буквально в первые месяцы эксплуатации авто, поэтому медлить нельзя.
Новости о товаре
- Масла, автохимия, жидкости, стали еще доступней. 12 Августа 2014
Уважаемые покупатели! Спешим сообщить вам, что с сегодняшнего дня в интернет магазине AvtoALL.RU проводится акция, благодаря которой вы сможете приобрести любые масла, автохимию, жидкости по закупочным ценам*!

Цены и наличие товара во всех магазинах и складах обновляются 1 раз в час. При достаточном количестве товара в нужном вам магазине вы можете купить его без предзаказа.
Интернет-цена — действительна при заказе на сайте или через оператора call-центра по телефону 8-800-600-69-66. При условии достаточного количества товара в момент заказа.Цена в магазинах — розничная цена товара в торговых залах магазинов без предварительного заказа.
Срок перемещения товара с удаленного склада на склад интернет-магазина.
Представленные данные о запчастях на этой странице несут исключительно информационный характер.
b074f4b07cac81247fe2bfdbbb416895
Добавление в корзину
Доступно для заказа:
Кратность для заказа:
ДобавитьОтменить
Товар успешно добавлен в корзину
!
В вашей корзине на сумму
Закрыть
Оформить заказBody Антикор 950 (серый) 1 л.
Артикул: 9501с
Наличие на складе: Есть в наличии
Описание:
Специальный антикоррозийный антигравийный состав Body 950 на основе каучука и синтетических смол.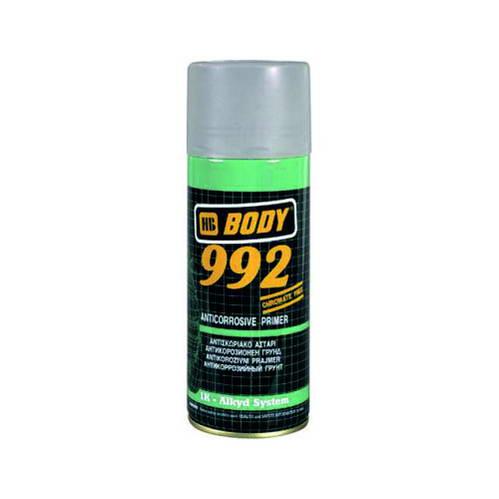
Характеристики товара
- Бренд Body
- Объем 1 л.
- Цвет
- Техническая документация Открыть
- Штук в коробке 6
- Страна Греция
- Статус Есть в наличии
BODY 910 СЕРЫЙ Антикор Мастика 1 кг
BODY 910 СЕРЫЙ Антикор Мастика 1 кг | Avto-палитраАвтоэмали, подбор, материалы и оборудование для кузовного ремонта
ПроизводительBody

Этот сайт использует файлы cookies для более комфортной работы пользователя. Продолжая просмотр страниц сайта, вы соглашаетесь с использованием файлов cookies. Если вам нужна дополнительная информация или вы не хотите соглашаться с использованием cookies, пожалуйста, посетите страницу «О cookies».
Антикоррозийная краска (серая) -продукты — SHEN
- Серый
- Высокая зона покрытия
- Устойчивость к истиранию и ударам
- УФ и атмосферостойкий
Смолы алкидные пентафтальные, наполнители антикоррозионные, пигменты, уайт-спирит.
Рекомендуемое использованиеПредназначен для окраски металлических поверхностей и защиты от коррозии. Используется для защиты стальных, чугунных и других поверхностей из черных металлов, в том числе слегка заржавевших. Краска обеспечивает прочную и надежную защиту металлических конструкций, трубопроводов от коррозии.
Подготовка поверхностиОкрашиваемая поверхность должна быть чистой, сухой и запыленной, масляной, краской. бесплатно.
заявка- Тщательно перемешайте перед использованием.
- Использование для разведения уайт-спирит или другие бензольные растворители.
- Краску наносить кистью, валиком или распылителем.
- Покраска должна быть выполнена при температуре не ниже + 5 ° С.
- При температуре окружающей среды + 20 ° C, влажность — 65%, второй слой наносить ориентировочно. через 4-6 часов.
- Когда работа закончена или взвешенные, тщательно промойте инструменты растворителем.
- Утилизируйте металлический контейнеры в соответствии с местным законодательством.
Температура базы при нанесении | из От + 5 ° С до + 30 ° С |
Краска расход на один слой Подробнее точнее, расход краски зависит от гладкости покрываемой поверхности. | 1л / 8-10 м² 3,785 л / 30-40 м² 20л / 180-200 м²
|
Финал высыхание краски при температуре окружающей среды + 20 ° C градус, влажность — 65%
| 24 часы |
Доступные размеры
Металлические контейнеры объемом 3785 литров и 20 литров.
Место храненияХранить в закрытом виде при температуре не ниже + 5 ° С в течение 12 месяцев после даты изготовления, указанной на упаковке.
Условия эксплуатации- Беречь от огня.
- Беречь от солнечных лучей.
- Хранить в недоступном для детей месте.
- При окраске больших поверхностей защищать органы дыхания. органы в защитной маске.
- Избегайте контакт с кожей.
- При попадании в глаза обратиться к врачу.
- Когда
работая в условиях, отличных от нормальных, характеристики могут отличаться от
указанные выше.
- Если металлическая поверхность предварительно пропитана маслом, покраска Работы можно производить только после снятия масляного слоя с поверхности.
- производитель не несет ответственности за работу с нарушением инструкций.
Аэрозольная краска антикоррозионная серая Antiruggine grigia САКС
Помня ваши настройки, нам не нужно вас просить: e.грамм. страна каждый раз, когда вы посещаете наш сайт. Ваши настройки также говорят нам о том, какое оборудование вы используете. Таким образом, мы можем настроить сайт так, чтобы обеспечить максимальное удобство для пользователей. Чтобы еще больше оптимизировать ваш опыт, мы собираем данные о ваших передвижениях и использовании сайта.
Эти файлы cookie обычно имеют срок действия в будущем и остаются в вашем браузере до тех пор, пока срок их действия не истечет или не будут удалены вручную.Мы используем постоянные файлы cookie для таких функций, как тикбок «Оставаться в системе», что упрощает доступ для пользователя в качестве зарегистрированного пользователя. Мы также используем постоянные файлы cookie, чтобы лучше понимать привычки наших пользователей и улучшать веб-сайт в соответствии с вашими привычками. Эта информация анонимна — мы не видим информацию об отдельных пользователях. Используемый файл cookie — site_cookie_info и хранится в течение одного года.
Статистические файлы cookie путем анонимного сбора и отправки данных помогают владельцам сайтов понять, как посетители взаимодействуют с сайтом. Это файлы cookie, которые обеспечивают веб-аналитику Beorol, анализ использования нашего сайта и измерение трафика, которые Beorol проводит для улучшения качества и содержания предлагаемых услуг.
Маркетинговые файлы cookie используются для отслеживания посетителей веб-сайтов. Они используются, чтобы показывать пользователям релевантную рекламу и побуждать их к участию, что важно для сторонних издателей и рекламодателей.Интернет-магазин Beorol использует объявления и файлы cookie Google Analytics, а также объявления / ga-audiences и сбор и файлы cookie Facebook.
Превращение нативной или корродированной поверхности сплава Mg в антикоррозионное покрытие в возбужденном CO 2
Реакция MgO с возбужденным CO
2 * при комнатной температуре Сообщалось, что электронный луч (электронный луч) может значительно повысить скорость реакции молекул газа с твердыми частицами за счет возбуждения частиц газа, адсорбированных на поверхности твердого реагента 21 , или эффекта электростатического поля, индуцированного электронами, с эффектом памяти для предшествующего облучения электронным пучком 22 .Вдохновленные этим, мы предлагаем использовать освещение электронным лучом внутри ПЭМ окружающей среды для активации адсорбированного CO 2 (например, чтобы превратить их в ионные фрагменты CO 2 + , CO 2 2+ , C + , O + и т. Д. 23 ; эти виды CO 2 с высокой химической активностью обозначены CO 2 * ) вокруг образца Mg, может инициироваться химическая реакция , т. е. MgO + CO 2 * → MgCO 3, при комнатной температуре.Схематический дизайн показан на рис. 1.
Схематическая диаграмма, показывающая, как преобразовать естественную поверхность в MgCO 3 . Микростолбик Mg с размером, прозрачным для электронного пучка, изготавливается сфокусированным ионным пучком (слева), а затем выдерживается на воздухе в течение 30 минут с образованием пленки естественного оксида (в центре). Ожидается, что после переноса в E-TEM сформированный воздухом поверхностный слой будет реагировать с возбужденным электронным пучком CO 2 * и образовывать компактный защитный слой MgCO 3 на поверхности столба без каких-либо дополнительных нагрев (справа)
Чтобы проверить возможность использования CO 2 * , возбуждаемого электронным пучком, для запуска реакции, мы сначала протестировали чистый MgO (синтезированный гидротермальным методом, более подробную информацию об обработке см. в разделе «Методы») .На рис. 2а показаны агрегированные чешуйки наноразмерных пластинок MgO, каждая из которых представляет собой монокристалл с гексагональной морфологией (см. Дополнительный рис. 1). Агрегированные хлопья MgO оставались стабильными после 14-минутного облучения электронным пучком (рис. 2b, интенсивность электронного пучка составляла ~ 0,1 А · см −2 ) в вакууме. Затем в камеру пропускали газ CO 2 (чистота 99,99%) с 2 Па. Через минуту грани кристаллического MgO начали искривляться. После этого хлопья начали сжиматься, и совокупность впоследствии свернулась в один цельный продукт реакции (рис.2в). Во время этого процесса в продукте было заключено много высокомобильных пузырьков CO 2 , прежде чем газ смог выйти. Выращенный продукт был аморфным, который позже кристаллизовался в нанокристаллы MgCO 3 посредством нагревания (до 400 ° C, с использованием нагревательного устройства Protochips in situ TEM), о чем свидетельствует соответствующая дифракционная картина на рис. 2d. Весь процесс реакции in situ был записан в дополнительном фильме 1. Чтобы дополнительно подтвердить, что возбужденный CO 2 * вместо других факторов (например.грамм. Нагрев электронным пучком, создание дефектных участков при облучении электронным пучком 24 или эффект электростатического поля в оксидной пленке 22 ) имеют решающее значение для реакции, были также проведены следующие эксперименты. Мы заблокировали электронный пучок и нагрели образцы MgO от комнатной температуры до 300 ° C в атмосфере CO 2 2 Па. Хлопья MgO не показали видимых изменений после выдержки при 300 ° C в течение 15 минут. Пока температура опускалась до комнатной температуры, хлопья MgO вступали в реакцию с CO 2 * сразу после облучения электронным пучком (см. Дополнительный рис.2 и дополнительный фильм 2). Продолжающаяся реакция MgO с возбужденным CO 2 * прекратилась, как только было прекращено облучение электронным пучком (см. Дополнительный рисунок 3), что позволяет предположить, что эта реакция не проявляет очевидного эффекта памяти 22 для предшествующего электрона. лучевое облучение. Это явление не может быть объяснено дефектами 24 , вызванными облучением электронным пучком, или эффектом электростатического поля 22 внутри оксидной пленки. Следовательно, разумно предположить, что реакцию MgO с CO 2 при комнатной температуре следует отнести к стимулированному электронным пучком возбуждению частиц CO 2 , адсорбированных на поверхности оксида Mg.
Проверка предложенного принципа действия. — ПЭМ-изображение чешуек кристаллов MgO, синтезированных гидротермальным методом. b Чешуйки MgO не изменились после облучения электронным пучком 300 кэВ, 0,1 А / см 2 в течение 14 мин. c Введение 2 Па CO 2 атмосферы приводит к реакции, т. е. MgO + CO 2 → MgCO 3 , происходит бурно. Конечным продуктом является то, что хлопья MgO превратились в кусок аморфного продукта с множеством пузырьков внутри. d После нагревания до 400 ° C в вакууме в течение 2 минут аморфный продукт кристаллизовался. На вставке в выбранной области электронограммы (SAED) показано, что это нанокристаллический MgCO 3 . e — h Эволюция поверхности Mg-столба, изготовленного из FIB, во время воздействия CO 2 Па 2 и облучения электронным пучком. Изображения ПЭМ, показывающие процесс преобразования слоя естественного оксида в компактный нанокристаллический слой MgCO 3 и MgO.Масштабные линейки: d 200 нм, h 10 нм
Формирование слоя MgCO
3 на поверхности столба Mg Далее мы демонстрируем, что слой MgCO 3 действительно может быть сформирован на поверхности Mg. / Магнезиальные сплавы. Образцы Mg были специально изготовлены в виде цилиндрических микростолбиков для облегчения наблюдения в реальном времени и получения изображений с помощью E-TEM (см. Рис. 1). Стойки из номинально чистого магния с электронно-прозрачными размерами были изготовлены с использованием сфокусированного ионного пучка (FIB).Подробный процесс изготовления описан в разделе «Методы». После 30-минутной выдержки на воздухе эти столбы были перенесены в E-TEM. Как видно на рис. 2д, сформированный воздухом слой имеет толщину около 8 нм. Он кажется сплошным и плотным, потому что толщина достаточно мала, чтобы выдержать рассогласование решеток. Затем мы обработали столбы из FIBed Mg в атмосфере CO 2 при 2 Па с интенсивностью электронного пучка ~ 0,1 А · см −2 . Примерно через 10 мин на поверхности появились небольшие кристаллические грани (отмечены оранжевыми пунктирными линиями) (рис.2е). Затем контраст этих граней уменьшился, и некоторые наноблистеры начали формироваться и расти (рис. 2g). После 18 минут воздействия CO 2 пузыри перестали увеличиваться в размерах, а область пузырей постепенно сглаживалась. Последний поверхностный слой после реакции выглядел более компактным, чем исходный слой оксида / гидроксида, и контраст его границы раздела с металлической подложкой уменьшился, как показано на фиг. 2h. Последний слой MgCO 3 является кристаллическим, как показано на ПЭМ-изображении высокого разрешения (дополнительный рис.4), который представляет собой увеличенный вид области в рамке на рис. 2h. Анализ спектроскопии потерь энергии электронов (EELS) выполняли для определения состава конечного продукта реакции (далее именуемого шкалой). После реакции появился очевидный край C-K (дополнительный рис. 5а), который указывает на наличие углерода в отложениях. Электронная дифракция на выбранной площади (SAED) и ПЭМ-анализ высокого разрешения подтвердили присутствие как кристаллического MgCO 3 , так и MgO после реакции (дополнительный рис.5b, дополнительный рис. 6).
Вышеупомянутые явления можно объяснить следующим образом. Сначала молекулярный CO 2 был адсорбирован на поверхности естественного оксида, а затем они были возбуждены электронным пучком, образуя частицы CO 2 (CO 2 * ). CO2 под электронным облучением 6 .Возбужденный CO 2 * может также реагировать с оставшимся Mg (OH) 2 через Mg (OH) 2 (с) + CO 2 * = MgCO 3 (с) + H 2 O (г) одновременно. Следует отметить, что вместе с реакцией вновь образованный MgCO 3 был плотным и достаточно компактным, чтобы остановить утечку ранее введенного газа CO 2 , который накапливался, образуя поверхностные пузыри. Когда поверхностный слой был полностью преобразован в компактный MgCO 3 , реакция прекратилась, потому что адсорбированный CO 2 * на поверхности столбов больше не мог взаимодействовать с внутренним оксидом.Однако заключенный CO 2 * будет потребляться непрерывно, вместе с исчезновением наполненных газом блистеров. Эти вновь образованные MgCO 3 и остаточный оксид составляют поверхностный слой.
Стоит отметить, что по сравнению с более бурной реакцией возбужденного CO 2 * со свободно стоящим MgO (рис. 2b – d и дополнительный рис. 7, оксидная оболочка отделена от столба), которая дает аморфные продукты, реакция со слоем MgO на металлическом Mg более умеренная, и конечный продукт является кристаллическим.Предположительно, это связано с тем, что скорость реакции зависит от удельной поверхности реагентов. Большая удельная поверхность способствует адсорбции возбужденных частиц CO 2 * , что, в свою очередь, может ускорить процесс реакции. С термодинамической точки зрения, более высокая скорость реакции имеет тенденцию к образованию аморфной фазы из-за сильно неравновесных условий реакции, в то время как более низкая скорость реакции более способствует образованию кристаллического MgCO 3 , поскольку условия реакции ближе к равновесию.
Эффект ингибирования коррозии защитной пленки MgCO
3 Испытания на погружение в водную среду были проведены для проверки коррозионной стойкости выращенных пленок MgCO 3 . Обычно раствор NaCl с концентрацией 3,5 мас.% Является первым выбором в качестве коррозионной среды. Однако, чтобы сократить время микротехнологии, толщина Mg-материала, на котором опоры были изготовлены FIB, обычно была менее 5 мкм. Мы обнаружили, что тонкая область растворяется в 3.5 мас.% Раствора NaCl в течение всего 10 с. Учитывая это, мы выбрали деионизированную воду в качестве коррозионной среды и в основном сосредоточили внимание на различии между столбами из Mg, обработанными волокном, и столбами, обработанными в CO 2 . После погружения в течение 3 минут столбы из чистого Mg, обработанные методом FIB, подверглись сильной коррозии, в то время как те, что были обработаны в CO 2 , остались нетронутыми (рис. 3a). Это ясно демонстрирует, что шкала MgCO 3 эффективна для защиты металла Mg. То же самое было обнаружено и для сплавов Mg на примере сплава ZK 60 Mg с небольшими выделениями (рис.3б). Электронный пучок сводился только к верхней половине столба ZK 60. После погружения в деионизированную воду на 3 мин, на изображении ПЭМ можно увидеть очевидную границу между двумя частями: обработанная верхняя половина была хорошо защищена от водной среды, а нижняя половина серьезно корродировала. Это напрямую продемонстрировало, что именно CO 2 адсорбируется на пористом поверхностном слое естественного оксида вместо свободно движущихся молекул газа CO 2 , которые активируются электронным лучом.В то же время можно сделать вывод, что пленка MgCO 3 является эффективным барьером для защиты сплавов Mg / Mg от воздействия окружающей среды в водной среде.
Превращение поверхности самородного сплава Mg в защитное покрытие. a ПЭМ-изображения двух Mg столбов (Mg столба as-FIBed и столба, обработанного CO 2 ) до и после погружения в деионизированную воду на 3 мин. b Только половина столба из сплава ZK 60 Mg была облучена электронным пучком в CO 2 .Обработанная верхняя половина была хорошо защищена от водной среды и оставалась неповрежденной, о чем свидетельствует вставка дифракционной картины, в то время как нижняя половина серьезно корродировала. Ореолы на вставке дифрактограммы указывают на аморфный продукт коррозии. Масштабные линейки: a 100 нм, b 200 нм
Продукты коррозии Тьюринга для MgCO
3 защитный слой Вышеупомянутые обсуждения относятся к Mg (и ZK 60), имеющему только его естественный оксид на поверхности.Продукты коррозии сплавов Mg во влажном воздухе или в воде обычно представляют собой смесь MgO и Mg (OH) 2 6,25,26 . Поскольку возбужденный CO 2 * может реагировать с MgO при комнатной температуре, он должен быть способен реагировать с продуктами коррозии на сплаве Mg с образованием также MgCO 3 . Чтобы подтвердить это, мы предварительно подвергли коррозии некоторые опоры из магниевого сплава. Стойка из сплава Mg с добавлением FIB (рис. 4а, дополнительный рис. 8) была погружена в деионизированную воду на 1 мин, а затем высушена на воздухе в течение 1 часа.Время погружения контролировали, чтобы обеспечить достаточное количество продуктов коррозии на поверхности, избегая при этом обширной коррозии внутри. Для лучшего сравнения мы намеренно выбрали длинный столб (рис. 4б), который не подвергся коррозии полностью, т.е. весь столб, за исключением его части со свободным концом, был покрыт пушистым Mg (OH) 2 (MgO). Коррозия, вероятно, началась с базовой части столбов, которую можно рассматривать как резервуар с водой, а затем процесс коррозии расползался по столбу.Вставка дифракционной картины от нижней части столба показывает, что металлическая подложка остается монокристаллической, несмотря на ее корродированную поверхность. Затем нижнюю часть с пушистыми продуктами коррозии облучали электронным пучком в атмосфере CO 2 4 Па в течение 20 мин. Пушистая пленка вокруг столба сжалась из-за реакции с CO 2 * . Продукт реакции наматывается на нижнюю часть столба, в результате получается гладкая поверхность (рис. 4c). Более подробная информация представлена в дополнительном фильме 3.На рисунке 4d показан этот образец после погружения в деионизированную воду на две минуты. Голая верхняя часть была сильно корродирована, в то время как часть, защищенная MgCO 3 , осталась нетронутой. Дальнейшая выдержка во влажном воздухе (относительная влажность: 65–80%, температура: 18–26 ° C) в течение 20 дней также подтвердила защитный эффект шкалы MgCO 3 (рис. 4д). Таким образом, даже когда на поверхности имеются значительные ранее существовавшие продукты коррозии, они будут реагировать с возбужденным CO 2 * с образованием компактной окалины MgCO 3 , которая защищает от дальнейшей коррозии.
Другими словами, вместо того, чтобы механически счищать предшествующие продукты коррозии, можно непосредственно преобразовать их в новый защитный поверхностный слой. Толщину шкалы MgCO 3 можно регулировать, регулируя время коррозии Mg и его сплавов. Помимо защиты сплавов Mg от воздействия окружающей среды, пленка MgCO 3 может эффективно снизить скорость окисления Mg при повышенных температурах (дополнительный рисунок 9).
Превращение корродированной поверхности сплава Mg в защитное покрытие. — стойка As-FIBed из сплава ZK 60 Mg и соответствующая выбранная зона для дифракции электронов (SADP). b После погружения в деионизированную воду на 1 минуту на поверхности столба образовалось рыхлое количество продуктов коррозии Mg (OH) 2 & (MgO). Обратите внимание, что верхняя часть была голой. c После того, как корродированный столб подвергался воздействию CO 2 и атмосферы облучения электронным пучком в течение 20 минут (электронным пучком была облучена только часть с пушистыми продуктами коррозии), вновь образованный MgCO 3 покрыл дно. часть столба. d После погружения в воду корродировала только верхняя часть столба. Область покрытия MgCO 3 осталась неизменной. e Верхняя часть подверглась дальнейшей коррозии, а защищенная часть осталась нетронутой после выдержки во влажном воздухе (относительная влажность: 65–80%, температура: 18–26 ° C) в течение 20 дней. Масштабная линейка, 200 нм
Механические испытания
Керамическое покрытие поверхности после анодирования или напыления обычно довольно хрупкое 10 , что может ухудшить механические характеристики сплавов Mg.Следовательно, важно оценить, насколько сильно изменится механическое поведение в результате применения шкалы MgCO 3 . Удивительно, но сформированный защитный слой не только имеет очень хорошую адгезию к своей подложке во время пластической деформации, но также заметно улучшает механические свойства небольших образцов Mg с точки зрения предела текучести и деформации сжатия до разрушения, как показано на рис. 5. Инженерные кривые зависимости деформации от сжатия двух типовых образцов показаны на рис.5а. Предел текучести обработанного столба (черный) намного выше, чем у заводского (красного) столба Mg.
Влияние обработанного поверхностного слоя на механические свойства образцов. a Типичные инженерные кривые напряжения-деформации при сжатии для сразу после изготовления столба из Mg (красный) и столба, обработанного CO 2 (черный). Обратите внимание, что предел текучести и способность к пластической деформации значительно улучшены. b Электронно-микроскопические изображения в светлом поле Mg-столба, обработанного в CO 2 (в черной рамке), и готового Mg-столба (в красной рамке) до и после сжатия.Защитный слой MgCO 3 показал отличную адгезию к своей подложке и отличную способность к совместимой деформации. c Статистика предела текучести и деформации сжатия в сравнении с Mg столбами. В отличие от тех столбов из Mg заводского изготовления, которые разрушаются из-за большого смещения при сдвиге, столбы с защитным слоем MgCO 3 деформируются однородно с плавным пластическим потоком с максимальной деформацией сжатия до 22%. Планки погрешностей представляют собой два стандартных отклонения. Шкала 200 нм
Морфология до и после сжатия (рис.5b) предполагают, что защитный слой MgCO 3 не только замедляет пластическую нестабильность, но также имеет отличную адгезию к своей подложке во время пластической деформации. Предположительно, это связано с тем, что скользящие дислокации блокируются прочной, но пластичной пленкой MgCO 3 , и их скопление или взаимодействие приводит к высокому напряжению текучести / текучести, деформационному упрочнению и однородному пластическому течению. На рис. 5с сравниваются напряжение текучести и деформация сжатия двух видов опор. Очевидно, предел текучести обработанных столбов почти вдвое выше, чем у необработанных. Деформация до разрушения (судя по появлению большого смещения при сдвиге) Mg-столбов как FIBed довольно низка (2–4%). Интересно, что для обработанных столбов мы постепенно увеличивали степень сжатия и обнаружили, что они деформировались с плавным пластическим течением, а защитная окалина не растрескивалась даже тогда, когда максимальная пластическая деформация достигала ~ 23%, что свидетельствует об адекватной адгезии с Mg-подложкой. Предположительно, это связано с тем, что окалина MgCO 3 достаточно тонкая, чтобы течь, с компактной начальной структурой без значительных недостатков.Должна быть критическая толщина, выше которой окалина MgCO 3 будет вести себя так же, как ее хрупкий массивный аналог. См. Дополнительные данные в дополнительном рис. 10.
Средства защиты от коррозии | АНТИКОРИТ | FUCHS SCHMIERSTOFFE GMBH
Незащищенные неизолированные металлические поверхности теряют коррозию, в частности, окисление, что часто приводит к значительному ухудшению состояния рабочей поверхности.
Это не только ухудшение внешнего вида, но часто также нарушение правильного функционирования подключенного устройства.
Степень коррозии в основном зависит от:
- состава и предварительной обработки материалов (особенно коррозионных, например ковкий или серый чугун)
- качества поверхности заготовки (коррозионное воздействие быстрее на шероховатых поверхностях, чем на гладких поверхностей)
- климатические воздействия
- другие внешние воздействия
Ингибиторы коррозии, такие как ANTICORIT от FUCHS, служат для защиты металлических поверхностей от воздействия атмосферы в самом широком смысле и, таким образом, предотвращают превращение металлов в их соединения, в частности оксиды.
В принципе, можно различать постоянную защиту от коррозии и временную защиту от коррозии.
Постоянная защита от коррозии, например, краски, гальванические покрытия и эмали.
Их трудно удалить механическими или специальными химическими процессами. Часто это невозможно без изменения или повреждения металлических поверхностей.
Продукция АНТИКОРИТ относится к группе временных ингибиторов коррозии.
Их можно относительно легко удалить с помощью растворителей или подходящих промышленных чистящих средств без повреждения защищаемых поверхностей.
Важно, чтобы защита от коррозии, как правило, была оптимально совместима с предыдущими этапами процесса и используемыми там продуктами.
Наша рекомендация: совместимые ингибиторы коррозии ANTICORIT из комплексной программы защиты от коррозии от FUCHS.
Критерии выбора средств защиты от коррозии
Относительно большое количество средств защиты от коррозии ANTICORIT является результатом совершенно разных технических требований.
В следующей таблице дается краткий обзор основных аспектов выбора подходящего средства защиты от коррозии для конкретного применения.
аспекты | критерии | примечание: |
---|---|---|
Срок защиты | недель, месяцев, лет | Сроки защиты должны рассматриваться с полным знанием складских помещений, средств транспортировка и упаковка. |
Тип пленки | маслянистая, масляно-тиксотропная, жирная, воскообразная, лакокрасочная | Дренажные свойства, сцепление, пылеподавление, гладкость, совместимость с упаковкой, липкость. |
Способ нанесения | кисть, погружение, распыление, капля | Геометрия поверхности, размер деталей, отдельные детали или серия, размеры и пространство, контроль толщины пленки, выпуск растворителей. |
Состояние деталей при нанесении | сухой, влажный, влажный, чистота, температура, движение | Обезвоживание, совместимость со смазочными материалами, использованными в предыдущем процессе формовки, цикл, производительность. |
Дальнейшая обработка | обработка, формовка, обработка поверхности, сборка | Адгезия в цанговых патронах, формовочная смазка, свариваемость, аварийная смазка, совместимость со смазочными материалами.![]() |
Удаление | протирка, водные щелочные чистящие средства, водно-нейтральные чистящие средства, водно-кислые чистящие средства, растворители — жидкие, растворители — паровая фаза | Обычно, чем выше эффект защиты, тем труднее удаление. |
Условия хранения | Чистота, транспортабельность, штабелирование, осязание, измеримость и тестируемость, внешний вид | Условия хранения должны быть определены и соблюдены с использованием четких критериев для достижения оптимального эффекта защиты. |
Транспортировка | наземные перевозки внутри компании, морские перевозки и воздушные перевозки | Высокая влажность воздуха и климатические условия ниже точки росы влияют на срок защиты. |
Экономическая эффективность | Затраты на землю, экономия в использовании, затраты на применение, затраты на удаление, степень повреждения из-за потенциальных жалоб | Только сумма всех затрат является мерой экономической эффективности. |
ДОГОТУЛС
ЩЕТКА 3 «ДОГОТУЛС
Код: DP4005
Бренд: DOGOTULS
Minimun Упаковка: 12
Смеситель краски универсальный 90x8x500мм оцинкованный
Код: HJ4010
Бренд: DOGOTULS
Minimun Упаковка: 6
ОЧКИ, СПОРТИВНЫЕ ЗАЩИТНЫЕ ОЧКИ, ПРОЗРАЧНЫЙ ТИП
Код: HM3050
Бренд: DOGOTULS
Minimun Упаковка: 12
НЕЙЛОНОВАЯ ПЕРЧАТКА С ЧЕРНЫМ НИТРИЛОВЫМ ПОКРЫТИЕМ
Код: HW3021
Бренд: DOGOTULS
Minimun Упаковка: 12
МАСКИРОВКА, ШИРИНА 3/4 ДЮЙМА Х ДЛИНА 50 М
Код: IP2002
Бренд: DOGOTULS
Minimun Упаковка: 48
РУЧНОЙ ПИСТОЛЕТ HVLP 350W
Код: JN2002
Бренд: DOGOTULS
Minimun Упаковка: 1
УДЛИНИТЕЛЬ МЕТАЛЛИЧЕСКИЙ, 1.

Код: KB4001
Бренд: DOGOTULS
Minimun Упаковка: 6
ТЕХНИЧЕСКИЕ ДАННЫЕ И ХАРАКТЕРИСТИКИ ИЗДЕЛИЯ
Код: KB4005
Бренд: DOGOTULS
Minimun Упаковка: 4
ПЛАСТИКОВАЯ РУЧКА С МЕТАЛЛИЧЕСКОЙ КАРКАСКОЙ, 9 «РАЗМЕР
Код: KB4010
Бренд: DOGOTULS
Minimun Упаковка: 6
СПРЕЙ КРАСКА, ЯРКО-ЧЕРНЫЙ ЦВЕТ
Код: PA4001
Бренд: DOGOTULS
Minimun Упаковка: 6
СПРЕЙ КРАСКА, ЯРКО-ЧЕРНЫЙ ЦВЕТ ГЛАЗАННЫЙ
Код: PA4002
Бренд: DOGOTULS
Minimun Упаковка: 6
СПРЕЙ КРАСКА, ЯРКО-КОРИЧНЕВЫЙ ЦВЕТ
Код: PA4003
Бренд: DOGOTULS
Minimun Упаковка: 6
СПРЕЙ КРАСКА ЯРКОГО ВЕРМИЛИОННОГО ЦВЕТА
Код: PA4006
Бренд: DOGOTULS
Minimun Упаковка: 6
СПРЕЙ КРАСКА ЯРКИЙ ТОМАТНЫЙ КРАСНЫЙ ЦВЕТ
Код: PA4007
Бренд: DOGOTULS
Minimun Упаковка: 6
СПРЕЙ КРАСКА, ЯРКО-ОРАНЖЕВЫЙ ЦВЕТ
Код: PA4008
Бренд: DOGOTULS
Minimun Упаковка: 6
СПРЕЙ КРАСКА, ЯРКОГО ЦВЕТА РОЯЛЬНО-СИНИЙ
Код: PA4009
Бренд: DOGOTULS
Minimun Упаковка: 6
СПРЕЙ КРАСКА ЯРКО-СИНИЙ ИСПАНСКИЙ ЦВЕТ
Код: PA4010
Бренд: DOGOTULS
Minimun Упаковка: 6
СПРЕЙ КРАСКА ЯРКОЕ ЛЕСНО-ЗЕЛЕНЫЙ ЦВЕТ
Код: PA4013
Бренд: DOGOTULS
Minimun Упаковка: 6
СПРЕЙ КРАСКА ЯРКОГО ЭКОЛОГИЧЕСКОГО ЗЕЛЕНОГО ЦВЕТА
Код: PA4015
Бренд: DOGOTULS
Minimun Упаковка: 6
СПРЕЙ КРАСКА ЯРКАЯ CATERPILLAR ЖЕЛТАЯ ЦВЕТА
Код: PA4017
Бренд: DOGOTULS
Minimun Упаковка: 6
СПРЕЙ КРАСКА, ЯРКИЙ АЛЮМИНИЕВЫЙ ЦВЕТ
Код: PA4023
Бренд: DOGOTULS
Minimun Упаковка: 6
СПРЕЙ КРАСКА ЯРКАЯ FORD СИНИЙ ЦВЕТ
Код: PA4030
Бренд: DOGOTULS
Minimun Упаковка: 6
СПРЕЙ КРАСКА, СИНИЙ ЦВЕТ МЕТАЛЛИК
Код: PA4037
Бренд: DOGOTULS
Minimun Упаковка: 6
СПРЕЙ КРАСКА ЗОЛОТОГО ЦВЕТА
Код: PA4038
Бренд: DOGOTULS
Minimun Упаковка: 6
Краска-спрей для акриловой эмали, 400 мл, 280 г Яркий хром
Код: PA4039
Бренд: DOGOTULS
Minimun Упаковка: 6
Акриловая эмаль-спрей краска, 400 мл, 280 г бронза
Код: PA4040
Бренд: DOGOTULS
Minimun Упаковка: 6
Акриловая эмалевая краска-спрей, 400 мл, 280 г Флуоресцентно-зеленый
Код: PA4041
Бренд: DOGOTULS
Minimun Упаковка: 6
Акриловая краска-спрей для эмали, 400 мл, 280 г Флуоресцентно-желтый
Код: PA4042
Бренд: DOGOTULS
Minimun Упаковка: 6
Акриловая эмалевая краска-спрей, 400 мл, 280 г Флуоресцентный оранжевый
Код: PA4043
Бренд: DOGOTULS
Minimun Упаковка: 6
Этот сайт использует файлы cookie для повышения производительности. Если ваш браузер не принимает файлы cookie, вы не можете просматривать этот сайт.
Настройка вашего браузера для приема файлов cookie
Существует множество причин, по которым cookie не может быть установлен правильно. Ниже приведены наиболее частые причины:
- В вашем браузере отключены файлы cookie. Вам необходимо сбросить настройки своего браузера, чтобы он принимал файлы cookie, или чтобы спросить, хотите ли вы принимать файлы cookie.
- Ваш браузер спрашивает вас, хотите ли вы принимать файлы cookie, и вы отказались.Чтобы принять файлы cookie с этого сайта, используйте кнопку «Назад» и примите файлы cookie.
- Ваш браузер не поддерживает файлы cookie. Если вы подозреваете это, попробуйте другой браузер.
- Дата на вашем компьютере в прошлом. Если часы вашего компьютера показывают дату до 1 января 1970 г., браузер автоматически забудет файл cookie. Чтобы исправить это, установите правильное время и дату на своем компьютере.
- Вы установили приложение, которое отслеживает или блокирует установку файлов cookie.Вы должны отключить приложение при входе в систему или проконсультироваться с системным администратором.
Почему этому сайту требуются файлы cookie?
Этот сайт использует файлы cookie для повышения производительности, запоминая, что вы вошли в систему, когда переходите со страницы на страницу. Чтобы предоставить доступ без файлов cookie потребует, чтобы сайт создавал новый сеанс для каждой посещаемой страницы, что замедляет работу системы до неприемлемого уровня.
Что сохраняется в файле cookie?
Этот сайт не хранит ничего, кроме автоматически сгенерированного идентификатора сеанса в cookie; никакая другая информация не фиксируется.
Как правило, в файлах cookie может храниться только информация, которую вы предоставляете, или выбор, который вы делаете при посещении веб-сайта. Например, сайт
не может определить ваше имя электронной почты, пока вы не введете его. Разрешение веб-сайту создавать файлы cookie не дает этому или любому другому сайту доступа к
остальной части вашего компьютера, и только сайт, который создал файл cookie, может его прочитать.
Влияние триполифосфата алюминия на защитные свойства акриловой краски на водной основе, нанесенной на ржавую сталь
Защитные свойства акриловой краски на водной основе, нанесенной на ржавую сталь, в условиях полного погружения, были исследованы с помощью электрохимического метода. техники.На покрытии после 500 часов погружения не было ржавчины, пузырей, трещин или чешуек. Полученные данные позволили предложить защитный механизм. Специфические пигменты, используемые в составе исследуемой краски, могут выделять фосфаты, образуя защитный слой на металлической подложке, который может препятствовать доступу агрессивных веществ к поверхности подложки. Покрытия проявляли электрохимическую активность в начале погружения; затем образуется слой и увеличивается стойкость покрытия.
1. Введение
Коррозия железа и его сплавов приводит к ежегодным потерям в миллиарды долларов. Примерно 90% всех металлических поверхностей защищены органическими покрытиями [1] из-за их низкой стоимости, простоты нанесения и эстетической функциональности. Органические краски обычно состоят из связующих систем, антикоррозионных пигментов, наполнителей, растворителей и различных добавок [2, 3]. Антикоррозионная способность пленок покрытия зависит от обработки поверхности металла, типа и концентрации антикоррозионного пигмента, способа формирования покрытия и т. Д. [4–8].
В настоящее время правительство уделяет все больше внимания здоровью персонала и охране окружающей среды. Таким образом, к составу красок и их применению предъявляются более строгие требования. Однако традиционные краски находятся в неблагоприятном состоянии из-за того, что в них используются летучие органические соединения (ЛОС) в качестве растворителей и токсичные химические вещества в качестве антикоррозионных пигментов. Помимо хороших антикоррозионных свойств, краска отличного качества должна быть экологичной и легкой в строительстве.Чтобы лучше соответствовать требованиям развития промышленности, таких как авиация и судостроение, низкое содержание летучих органических соединений, нетоксичность и плохая подготовка поверхности являются направлением развития.
Однако из-за проблем, связанных с окружающей средой и безопасностью, была проведена значительная исследовательская деятельность для повышения растущего спроса на снижение выбросов летучих органических соединений (ЛОС) и вредных загрязнителей воздуха, что привело к увеличению усилий по разработке систем на водной основе для использования в качестве покрытий [9] . Наиболее известными и наиболее часто применяемыми нетоксичными антикоррозийными пигментами являются фосфатные пигменты.А фосфат цинка был самым важным видом фосфатных пигментов до 2004 г. [10–12]. Но пигменты на основе фосфатов цинка были классифицированы в соответствии с Европейской директивой 2004/73 / EU как опасные для окружающей среды вещества в 2004 году [13]. В результате разработкой «безцинкового» ингибитора с низким или нулевым содержанием цинка занимаются производители. Триполифосфат алюминия — один из лучших вариантов [14–16].
Подготовка поверхности — ключевой фактор перед окраской, и успех системы защитного покрытия зависит от ее правильного выполнения.Традиционная теория считает, что плохая подготовка поверхности с последующей хорошей системой покрытия обычно дает худшие результаты, чем использование продуктов низкого качества на хорошо подготовленной поверхности. Ржавчина и оксиды на поверхности металла отрицательно влияют на поведение системы покрытий [17, 18]. Очистка, как правило, требует очень больших затрат и загрязняет окружающую среду. Преобразовательное покрытие может решить эту проблему. Его можно определить как соединение, образованное в результате химической реакции, которая превращает поверхность металлической подложки в соединение, которое стало частью покрытия.
Теперь наша команда разработала новую краску, в которой используются незагрязняющие ингибиторы, вода в качестве растворителя и которая может соответствовать плохой подготовке поверхности. Чтобы лучше продемонстрировать защитную функцию покрытия, поведение этой акриловой краски на водной основе, наносимой на ржавую сталь, изучается с помощью электрохимических методов.
2. Экспериментальная
2.1. Образцы
Изучено поведение новой акриловой краски, произведенной в нашей лаборатории. В таблице 1 приведены наиболее важные технические характеристики этой краски.В качестве металлической основы использовалась низкоуглеродистая сталь Q235. Исследуемые образцы представляли собой прямоугольные образцы размером 100 мм × 150 мм × 1 мм. Образцы шлифовали абразивной бумагой SiC зернистостью до 240, промывали по очереди дистиллированной водой и ацетоном, а затем сушили на воздухе. После этого образцы опрыскивали раствором 3,5% NaCl в течение 15 дней для образования ржавчины. Перед покраской плавающая ржавчина образца была очищена абразивной бумагой SiC. Затем краску наносили кистью до толщины 130 мкм мкм, а сравниваемые образцы эпоксидной антикоррозионной краски составляли 160 мкм мкм.Формы царапин соответствуют EIS, а линии — LEIS. Все царапины нанесены универсальным ножом длиной 10 мм и шириной 50 мкм м. Расстояние от царапины до каждого края образцов было более 20 мм.
|
2.

Измерения EIS проводились в растворе 3,5 мас.% NaCl с помощью системы PARSTAT 2273 в диапазоне частот от 10 5 Гц до 10 −2 Гц при потенциале холостого хода, с 20 возмущение потенциала мВ. Внутренняя параллельная емкость измерительной машины была меньше 5 пФ. Использовали трехэлектродную схему, состоящую из насыщенного каломельного электрода (SCE) в качестве электрода сравнения, платинового электрода в качестве противоэлектрода и образца с покрытием в качестве рабочего электрода.Для рабочего электрода площадь экспонирования составляла 3,14 см 2 , что уменьшило бы величину измеренного импеданса и позволило бы избежать выхода за пределы измерительной аппаратуры, особенно на средних и высоких частотах. Площадь Pt-электрода была примерно равна размеру рабочего электрода, около 4 см 2 . Подгонка спектров импеданса производилась с помощью программного обеспечения ZsimpWin.
Измерения LEIS были выполнены на образцах покрытий, погруженных в 3,5% раствор NaCl, с помощью сканирующей электрохимической станции PAR Model 370.Таким образом, тестовый раствор для измерений LEIS представлял собой 0,001 М раствор NaCl. Микрозонд наступали на обозначенный участок поверхности электрода. Сканирование проводилось в виде плоского растра. Размер шага контролировали, чтобы получить график 32 линии × 21 линию. Сигнал возмущения переменного тока составлял 100 мВ, а частота возбуждения для измерений импеданса была зафиксирована на уровне 5 кГц. Все измерения LEIS проводились при температуре окружающей среды (~ 22 ° C). Каждый тест проводился как минимум дважды, чтобы подтвердить повторяемость.
3. Результаты и обсуждение
3.1. Испытания на погружение
На рис. 1 показан микрорельеф коррозии окрашенного образца, погруженного в раствор 3,5 мас.% NaCl на 21 день. Как можно видеть, на покрытии не было ржавчины, пузырей, трещин или чешуек, что указывает на то, что покрытие обладает замечательной стойкостью к коррозии.
В таблице 2 представлено сравнение морфологии коррозии между эпоксидной антикоррозионной краской и нашей краской в зависимости от времени воздействия.Результат показывает, что исследуемое покрытие показало хорошие антикоррозионные свойства. После 24 часов воздействия на царапину эпоксидного антикоррозионного покрытия наблюдалась явная ржавчина, но никаких изменений в исследуемом покрытии. Царапина исследуемого покрытия все еще не имела видимой ржавчины через 8 дней воздействия; однако в образце антикоррозионного эпоксидного покрытия и даже в пузырях была обнаружена серьезная коррозия.
|
Из приведенных выше результатов исследованное покрытие показывает функцию ингибирования до 3.5% раствор NaCl после погружения. В частности, по сравнению с эпоксидным антикоррозионным покрытием легко увидеть, что исследуемое покрытие обладает способностью к самовосстановлению. Это будет подробно рассмотрено в следующих разделах.
3.2. Спектроскопия электрохимического импеданса
На рис. 2 показаны диаграммы EIS, соответствующие испытаниям, выполненным на окрашенных образцах после того, как они подверглись испытаниям разной продолжительности. Полученные данные показывают, что в первые 12 часов погружения произошли интересные изменения.Диаграммы Найквиста системы за 1 час состояли из половины дуги емкостного реактивного сопротивления высокой частоты и дуги емкостного сопротивления низкой частоты. Через 2 ч они превратились в единую емкостную арку. Наблюдалось значительное уменьшение дуги, которая появлялась на диаграммах Найквиста в первые 2 часа и увеличивалась через 4 часа. Параллельно наблюдалось уменьшение модуля импеданса на диаграммах Боде в первые 2 часа и увеличение через 4 часа. Это уменьшение импеданса предполагает, что в течение первых часов погружения в систему в этот период увеличивается активность.Рисунок 2 (b) показывает, что диаграммы Найквиста представляют единственную емкостную арку, и арка непрерывно увеличивается от 1 дня до 21 дня.
На рис. 3 представлены диаграммы EIS, соответствующие испытаниям, проведенным на образцах исследуемой краски с царапинами после испытаний разной продолжительности. Диаграммы Найквиста представляют собой единую емкостную дугу. Параллельно неповрежденным окрашенным образцам наблюдалось значительное уменьшение дуги, которая сначала появлялась на диаграммах Найквиста, а затем увеличивалась.В отличие от этого, диаграммы Найквиста эпоксидных антикоррозионных покрытий с царапинами (рис. 4) также представляли единственную емкостную дугу, но со временем она уменьшалась. Нетрудно видеть, что модуль упругости образцов исследуемого покрытия с царапиной на диаграммах Боде уступал таковому эпоксидной антикоррозийной краске при инициировании. Но после 8 дней погружения произошла инверсия. Рисунок 5 наглядно показывает это явление. Это в соответствии с результатом погружения
Чтобы гарантировать плохую подготовку поверхности и хорошие антикоррозионные свойства нашей краски, в нее добавлено много специфических пигментов.Эти специфические пигменты являются химически активными, поэтому модуль покрытия находится на низком уровне. Специфическим пигментом, используемым в рецептуре исследуемого покрытия, является трифосфат алюминия. Механизм действия этого соединения четко не установлен.
В последние десятилетия пигменты на фосфатной основе часто используются в покрытиях для повышения их коррозионной стойкости [19–22]. Когда вода проникает в покрытие, пигменты на основе фосфат-анионов могут выделять фосфаты, образуя защитный слой на металлической подложке, который может препятствовать доступу агрессивных частиц к поверхности подложки [22, 23].В частности, триполифосфат алюминия может гидролизоваться с образованием H + , что может минимизировать образование гидроксильных групп на металлической подложке и замедлить распад катода, чтобы продлить срок службы органических покрытий [14].
Через 1 час диаграммы Найквиста системы состояли из одной половины емкостной дуги на высоких частотах и другой половины емкостной дуги на низких частотах. Один на высоких частотах может быть объяснен реакцией между водой и большим количеством трифосфата алюминия, хорошо диспергированного в матрице покрытия.Эквивалентная схема, показанная на рисунке 6 (а), была выбрана для моделирования данных за 1 час. После 2 часов погружения, поскольку трифосфат алюминия продолжает реагировать с водой, образуется более плотный защитный слой, который закрывает каналы от проникновения воды и приводит к повышению барьерных свойств покрытия. В результате диаграмма Боде системы продемонстрировала только одну постоянную времени, как показано на рисунке 2. По этой причине была выбрана эквивалентная схема, показанная на рисунке 6 (c). В схеме представляет собой сопротивление между рабочим электродом и электродом сравнения, обычно связанное с омным сопротивлением электролита.и связаны с емкостью двойного слоя и сопротивлением переносу заряда химически активных пигментов соответственно. связано с емкостью покрытия. представляет собой сопротивление пор и является мерой пористости вследствие разрушения покрытия.
Изучение эволюции диаграмм EIS во времени погружения позволяет сделать анализ изменения защитной способности окрашенных образцов. В нашем случае, исходя из соответствия экспериментальных диаграмм предложенной эквивалентной схеме, были рассчитаны значения емкости, и сопротивления, связанного со слоем краски (таблица 3).На рисунке 7 представлена динамика этих параметров в течение первых 24 часов воздействия. На этом рисунке можно увидеть, как с увеличением времени воздействия сопротивление покрытия сначала уменьшалось, а затем увеличивалось. Благодаря антикоррозийным свойствам триполифосфата алюминия количество дефектов покрытия уменьшается по мере образования защитного слоя. В первые 2 ч выдержки емкость покрытия увеличивается, так как вода проникает в покрытие и увеличивается проводимость покрытия.Однако трифосфат алюминия выделяет фосфаты, образуя защитный слой на металлической подложке, препятствуя доступу агрессивных частиц и коррозии. Таким образом, проводимость снижается, а емкость снижается.
|
На рис. 3 показаны EIS-диаграммы наших окрашенных образцов с царапинами после испытаний в разное время. Диаграммы Найквиста все время представляют одну емкостную петлю.Наблюдается значительное уменьшение дуги, которое сначала появляется на диаграммах Найквиста, а затем увеличивается. Причина этого явления заключается в том, что трифосфат алюминия выделяет фосфаты, образуя защитный слой на металлической подложке, когда вода поступает из дефекта. Вначале реакции вызывают уменьшение дуги диаграммы Найквиста и выбирают эквивалентную схему рисунка 6 (b). Вместе с иммерсионным расширением защитный слой уплотняется и свод увеличивается. По этой причине выбрана эквивалентная схема, показанная на Рисунке 6 (c) (Таблица 4).Пропускная способность покрытия сначала значительно увеличивается, а затем уменьшается. Между тем сопротивление покрытия ведет себя наоборот (рис. 8).
|
Для образцов с антикоррозийным эпоксидным покрытием с царапинами на диаграммах Найквиста также представлена единственная емкостная дуга (рис. 4). Но графики из диаграмм Боде показывают две постоянные времени, а низкочастотный импеданс уменьшался с течением времени, потому что вода и агрессивные ионы диффундируют на границе раздела подложка / покрытие. Таким образом, выбрана эквивалентная схема, показанная на рисунке 6 (d) (таблица 5).
|
3.3. Картирование локализованного электрохимического импеданса
Как указано в проекции LEIS эпоксидного антикоррозионного покрытия (Рисунок 9), на начальной стадии погружения значение импеданса в дефекте было намного ниже, чем у соседнего неповрежденного покрытия из-за коррозии неизолированного металла в дефект. Когда время погружения увеличивается, импеданс в соседнем покрытии уменьшается, что объясняется проникновением коррозионного раствора из дефекта и, как следствие, расслоением покрытия, что визуально наблюдается после испытания, и вокруг дефекта появляется множество пузырей (Рисунок 11). .
Настоящая работа (рисунок 10) показывает, что, в отличие от результатов измерения импеданса эпоксидного антикоррозионного покрытия, значение импеданса на дефекте было не ниже, чем у соседнего неповрежденного покрытия исследуемого образца покрытия на всем протяжении погружения. время. В соответствии с результатами спектроскопии электрохимического импеданса, значение импеданса исследуемого покрытия со временем увеличивалось, поскольку пигменты на основе фосфат-анионов могут выделять фосфаты с образованием защитного слоя на металлической подложке, что может препятствовать доступу агрессивных частиц к подложке. поверхность.Результаты LEIS показывают, что исследуемые покрытия обладают лучшими самовосстанавливающимися и антикоррозионными свойствами.
4. Выводы
Поведение в условиях полного погружения акриловой краски на водной основе, нанесенной на ржавую сталь, было изучено с помощью электрохимических методов. Набор полученных данных позволил разработать механизм антикоррозионных свойств покрытия.
Это покрытие обладало хорошими антикоррозионными свойствами. После 21 дня полного погружения на покрытии не было ржавчины, пузырей, трещин или чешуек.По сравнению с образцами эпоксидной антикоррозийной окраски исследованные покрытия показали лучшие самовосстанавливающиеся и антикоррозионные свойства.